What welding projects are you working on? Are you proud of something you built?
How about posting some pics so other welders can get some ideas?
How about posting some pics so other welders can get some ideas?
Used an old hand-sledge we found out shooting. Came out okay.
- Attachments
-
- DSCN4595.JPG (123.13 KiB) Viewed 41066 times
Last edited by Nils on Sat Feb 16, 2013 5:33 pm, edited 2 times in total.
Everlast PowerTig 250EX, PowerTig 185 Micro, PowerArc 160STH, Miller Trailblazer 301G, Millermatic 140 Auto-Set
- Otto Nobedder
-
Weldmonger
-
Posts:
-
Joined:Thu Jan 06, 2011 11:40 pm
-
Location:Near New Orleans
ArcherAndy
- ArcherAndy
-
New Member
-
Posts:
-
Joined:Thu Feb 21, 2013 2:21 pm
-
Location:Morgantown, Indiana
I really like that idea! I have been wanting to try and build a 3rd hand. Very resourceful use of materials.
Miller Syncrowave 250 water cooled TIG
noddybrian
- noddybrian
-
Weldmonger
-
Posts:
-
Joined:Thu Jan 24, 2013 12:13 pm
Ok - slightly different outlook on the 3rd hand thingy ! I'd never worried too much about it , but recently when altering a mirror finished stainless steel part it arced badly on the bench & made me say " DARN " ! so the hammer head was laying under the bench as was the 1/2" & 3/4" square - I figured making it touch at 3 points would be naturally more stable & the hammer head can be slid up & down to excert more weight if needed - the feet are rounded in 1 direction but flat across giving more choice - their clad in copper sheet to improve conductivity - I also bolted a bit of 1/4" flat copper on to "light up on" after grinding the tungsten as I manage to sweep them off the bench otherwise.
- IMG_1114.JPG (92.73 KiB) Viewed 40867 times
- IMG_1115.JPG (93.26 KiB) Viewed 40867 times
- Otto Nobedder
-
Weldmonger
-
Posts:
-
Joined:Thu Jan 06, 2011 11:40 pm
-
Location:Near New Orleans
That's sweet! I like the sliding weight.
Do you have the copper bonded to the steel in any way? Solder, or something?
Steve S
Do you have the copper bonded to the steel in any way? Solder, or something?
Steve S
noddybrian
- noddybrian
-
Weldmonger
-
Posts:
-
Joined:Thu Jan 24, 2013 12:13 pm
Yes- the copper is soft soldered to the legs for conductivity - but could be changed if necessary.
Weber Sarge
- Weber Sarge
-
New Member
-
Posts:
-
Joined:Thu Jan 24, 2013 2:05 pm
Here is one I made last winter with a sliding weight -
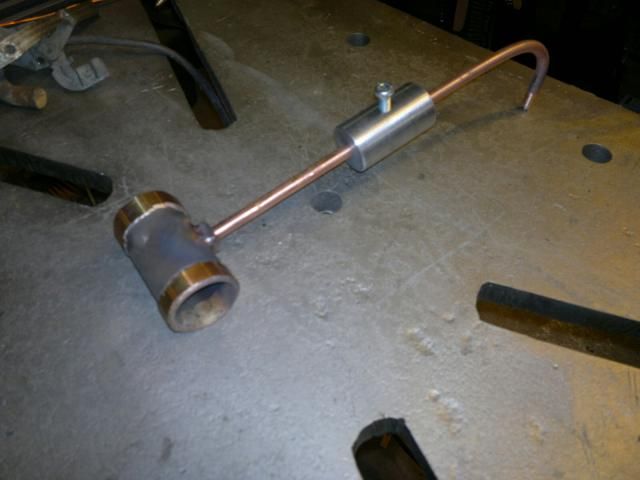
The tip and ground faces on the round tubing are copper building wire that were tig welded directly to the steel , then turned down in the lathe . No more arc marks on work , big help for sure .
Sarge
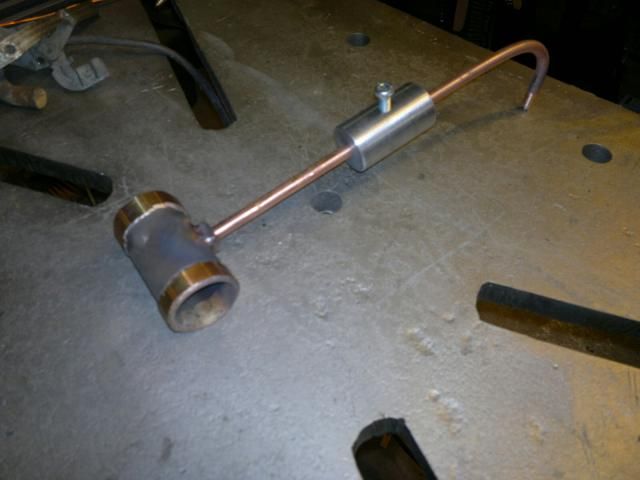
The tip and ground faces on the round tubing are copper building wire that were tig welded directly to the steel , then turned down in the lathe . No more arc marks on work , big help for sure .
Sarge
noddybrian
- noddybrian
-
Weldmonger
-
Posts:
-
Joined:Thu Jan 24, 2013 12:13 pm
Nice job - I like the sliding weight - looks good.
Wish I'd had more copper around when I made mine but it's not a material I really work with - had just a few offcuts of sheet under the metal shear so that had to do.
Glad to see someone else with a lathe - began to think I was the only member with one ( actually it's several plus Milling machines etc - someone recently called me a "low buck Keith Fenner" !! not sure how to take that & I don't have the weird beard thing going on ! )
Wish I'd had more copper around when I made mine but it's not a material I really work with - had just a few offcuts of sheet under the metal shear so that had to do.
Glad to see someone else with a lathe - began to think I was the only member with one ( actually it's several plus Milling machines etc - someone recently called me a "low buck Keith Fenner" !! not sure how to take that & I don't have the weird beard thing going on ! )
Very impressed with the sledge hammer third hand, but I can't resist commenting that the steel in a sledge hammer is (usually) high carbon content, and is very, very useful. I have even seen one used as an anvil for knife making. Ah well, you know where it is if you need the steel for something else. Well done.
No issues, and so far for the work I do, my adjustable Set-Tru (0.0002" TIR), 6.25" Bison 6-jaw is THE best upgrade (the DRO being the second) I have done to my lathe.blaz wrote:I see a 6 jaw chuck there. That will be my next chuck I think. Any issues?
LOL wish I had the room or even the money but when I can afford it I want my own machine shop and complete welding setup with plasma cutters and a 4'x8' CNC plasma table toonoddybrian wrote: Glad to see someone else with a lathe - began to think I was the only member with one
I come from the "other side". I am already a machinist, with a small machine shop (lathe, mill, accessories, etc.) and I am now starting on the welding, but it will take a long time and a LOT of saved money before I can have a "welding shop"Ranger wrote:LOL wish I had the room or even the money but when I can afford it I want my own machine shop and complete welding setup with plasma cutters and a 4'x8' CNC plasma table toonoddybrian wrote: Glad to see someone else with a lathe - began to think I was the only member with one

Will
- Responsible
-
New Member
-
Posts:
-
Joined:Sun Oct 20, 2013 5:33 pm
I built this one when I was practicing 'T' joints. Made setting up easy.
- Attachments
-
- Third Hand 2.JPG (238.95 KiB) Viewed 22346 times
-
- ThirdHand.JPG (175.97 KiB) Viewed 22346 times
Weber Sarge
- Weber Sarge
-
New Member
-
Posts:
-
Joined:Thu Jan 24, 2013 2:05 pm
Don't sweat the copper issue - it's just building wire stripped and sanded clean , it was "good enough" for a third hand project . I've got a nice old Enco 12x36 , a bit sloppy but for most of what I need it works great .noddybrian wrote:Nice job - I like the sliding weight - looks good.
Wish I'd had more copper around when I made mine but it's not a material I really work with - had just a few offcuts of sheet under the metal shear so that had to do.
Glad to see someone else with a lathe - began to think I was the only member with one ( actually it's several plus Milling machines etc - someone recently called me a "low buck Keith Fenner" !! not sure how to take that & I don't have the weird beard thing going on ! )
Sarge
- weldin mike 27
-
Weldmonger
-
Posts:
-
Joined:Fri Apr 01, 2011 10:59 pm
-
Location:Australia; Victoria
Hey,
I finally got around to making some 3rd hand tools. 1 monster, 1 smaller and 2 matching (sort of) ones,
Mick
I finally got around to making some 3rd hand tools. 1 monster, 1 smaller and 2 matching (sort of) ones,
Mick
- Attachments
-
- 2013-10-31_15-05-04_554.jpg (544.4 KiB) Viewed 24179 times
-
- 2013-10-31_15-04-16_767.jpg (562.01 KiB) Viewed 24179 times
- weldin mike 27
-
Weldmonger
-
Posts:
-
Joined:Fri Apr 01, 2011 10:59 pm
-
Location:Australia; Victoria
- MinnesotaDave
-
Weldmonger
-
Posts:
-
Joined:Sun Oct 27, 2013 10:57 pm
-
Location:Big Lake/Monticello MN, U.S.A.
I like them 
When I did mine, I noticed they would still make small black arc strikes on my aluminum. Jody showed the same and used silicon bronze for the ends I believe.
I did not have any so I used house electrical wire and tigged some copper on mine

When I did mine, I noticed they would still make small black arc strikes on my aluminum. Jody showed the same and used silicon bronze for the ends I believe.
I did not have any so I used house electrical wire and tigged some copper on mine

Dave J.
Beware of false knowledge; it is more dangerous than ignorance. ~George Bernard Shaw~
Syncro 350
Invertec v250-s
Thermal Arc 161 and 300
MM210
Dialarc
Tried being normal once, didn't take....I think it was a Tuesday.
Beware of false knowledge; it is more dangerous than ignorance. ~George Bernard Shaw~
Syncro 350
Invertec v250-s
Thermal Arc 161 and 300
MM210
Dialarc
Tried being normal once, didn't take....I think it was a Tuesday.
- weldin mike 27
-
Weldmonger
-
Posts:
-
Joined:Fri Apr 01, 2011 10:59 pm
-
Location:Australia; Victoria
Return to “Welding Projects - Welding project Ideas - Welding project plans”
Jump to
- Introductions & How to Use the Forum
- ↳ Welcome!
- ↳ Member Introductions
- ↳ How to Use the Forum
- ↳ Moderator Applications
- Welding Discussion
- ↳ Metal Cutting
- ↳ Tig Welding - Tig Welding Aluminum - Tig Welding Techniques - Aluminum Tig Welding
- ↳ Mig and Flux Core - gas metal arc welding & flux cored arc welding
- ↳ Stick Welding/Arc Welding - Shielded Metal Arc Welding
- ↳ Welding Forum General Shop Talk
- ↳ Welding Certification - Stick/Arc Welding, Tig Welding, Mig Welding Certification tests - Welding Tests of all kinds
- ↳ Welding Projects - Welding project Ideas - Welding project plans
- ↳ Product Reviews
- ↳ Fuel Gas Heating
- Welding Tips & Tricks
- ↳ Video Discussion
- ↳ Wish List
- Announcements & Feedback
- ↳ Forum News
- ↳ Suggestions, Feedback and Support
- Welding Marketplace
- ↳ Welding Jobs - Industrial Welding Jobs - Pipe Welding Jobs - Tig Welding Jobs
- ↳ Classifieds - Buy, Sell, Trade Used Welding Equipment
- Welding Resources
- ↳ Tradeshows, Seminars and Events
- ↳ The Welding Library
- ↳ Education Opportunities