Page 1 of 9
my next Project
Posted: Tue Aug 28, 2012 9:39 pm
by CraigLam
I was going to call this my fifth project, but, I wanted to stop counting. I got like a million I want to do. Any way, here it is.
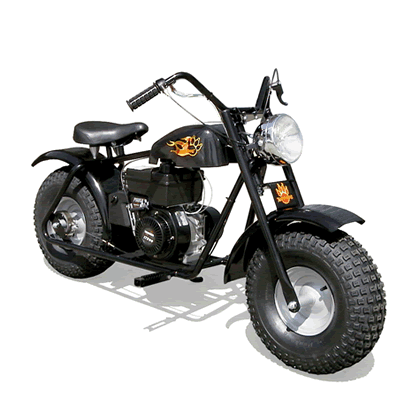
I was searching for mini bikes on the web, and most were the Taco 22 style. They weren't bad, but, when I saw the Yerf-dog, I had to have this. I mean, hey, if you know how to weld, why not? I needed a tube bender, though. Not so easy.The dies alone were $200.00 and up. So, I found a web site where there was a DIY tube bender. They recommend that you use seamless tube. With this bender, I'm pretty sure you don't have to. I'm using 8/4 oak and plowing it out with a 7/8" router bit for 7/8" pipe. Since all of this is mig welded, I need an argon bottle. The generator is on hold for now. All the parts I can get from ebay and are amazingly cheap.
Re: my next Project
Posted: Tue Aug 28, 2012 9:54 pm
by delraydella
pipe bending dies have to take a lot of pressure and i'm not sure oak could handle that,not even at 8/4. You can buy fairly cheap hydraulic pipe and tube benders and rollers from Harbor Freight. While they are nowhere near production run quality, they will certainly handle a few jobs.
I have rolled thinwall tube and conduit on plywood forms, but it can be a big pain because the tube will not conform to the proper size. It will spring back so you have to calculate the amount of springback and and make your form that much smaller.
Re: my next Project
Posted: Wed Aug 29, 2012 3:10 pm
by CraigLam
I called the lumber store where I buy my materials and told him the situation. He said oak might work. I asked if he could recommend a harder wood. Hard rock maple. I don't know why I didn't think of this before. It's also closed grain. Anything harder, I would have to get into the exotics. I'm going to use this once or twice. It should hold up. If it does hold up well, I may make a few Yerf-dogs and some Taco 22's and sell them.
Re: my next Project
Posted: Fri Aug 31, 2012 11:03 pm
by CraigLam
I shifted gears, so to speak. The pipe bender project is under way, but, I chose a different mini bike.
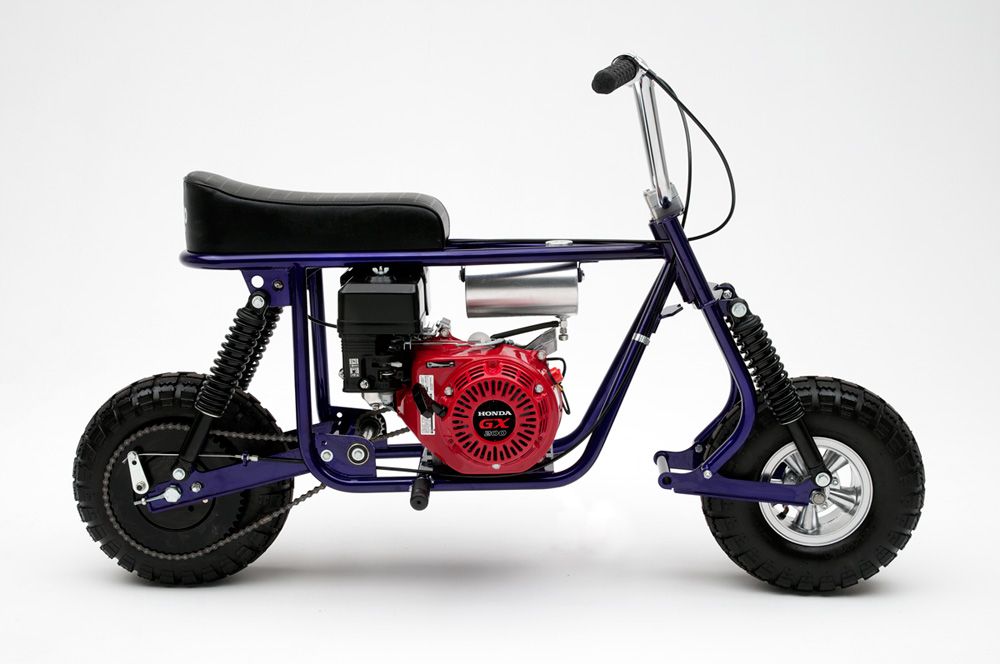
I chose this mini bike it has more of a motor cycle appearance to it. The suspension is way cooler and it has a seperate handle bar system. The handle bars are not bent and connected to the axle. This has a swing arm to it. Speaking of bent, can you recognize this?
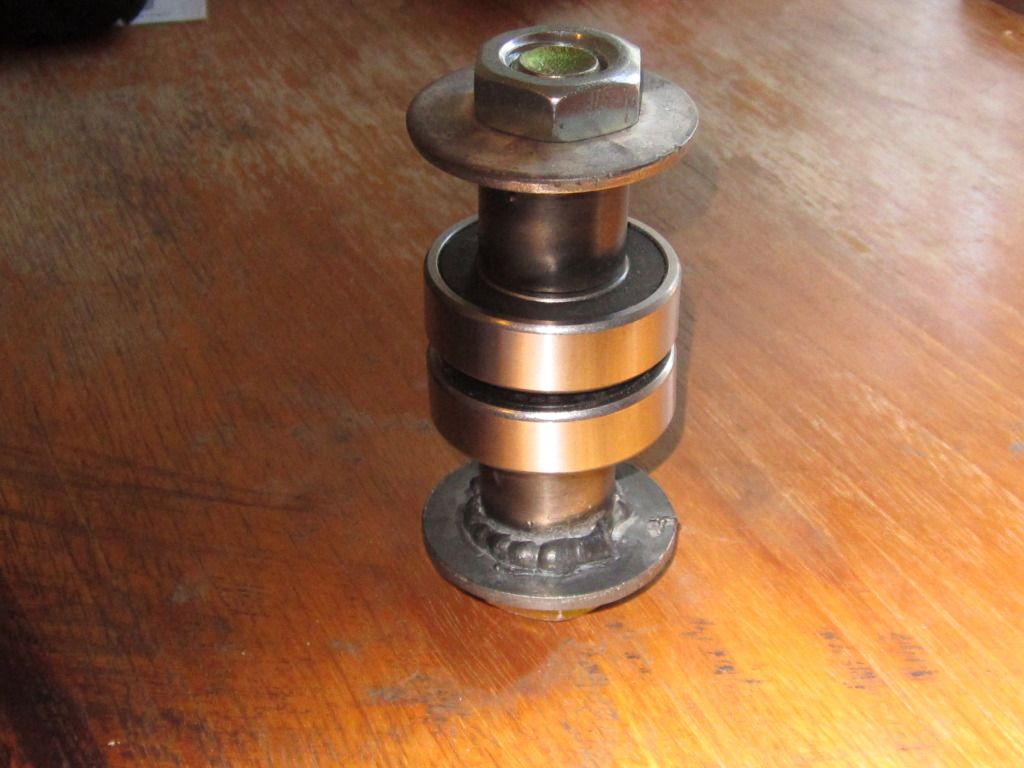
It's the center to the roller arm that swings around to bend the pipe. The bearings go in the center and the pressing arm(not made yet) seat against the pipes above and below the bearings. That crushes the die against the pipe to cause tangent pressure. Wish me luck. I'll post again after I make the dies.
Re: my next Project
Posted: Sat Sep 01, 2012 9:14 am
by Mike
Re: my next Project
Posted: Sat Sep 01, 2012 5:56 pm
by Otto Nobedder
If you're building your dies from hard-rock maple (or hardwood in general), mineral oil is an excellent treatment/lubricant for the die faces.
The easiest source is the local pharmacy, in the laxative section. Baby oil is the same thing, but usually costs more, and doesn't smell very "manly" in a shop.
Steve S.
Re: my next Project
Posted: Sun Sep 02, 2012 7:58 pm
by CraigLam
And people wonder why I love this post. You guys crack me up! Update. I have the follower and tomorrow, I'll have the stationary part done. I checked with Kevin, the head guy at Austin and he says Hickory is actually better. The lubricant is a very good idea. The less friction, the less kinking and the smoother the bend. Tuesday, I'm gonna go down and see if they have any thinwall 7/8" at Philips Steel. I called Jax Cycle Shop and they said that all the bicycles and mini bikes are made from 7/8" tube. Unless they are a custom frame type. The accessories, like the handle grips are made for 7/8". Anyway, here's the follower.
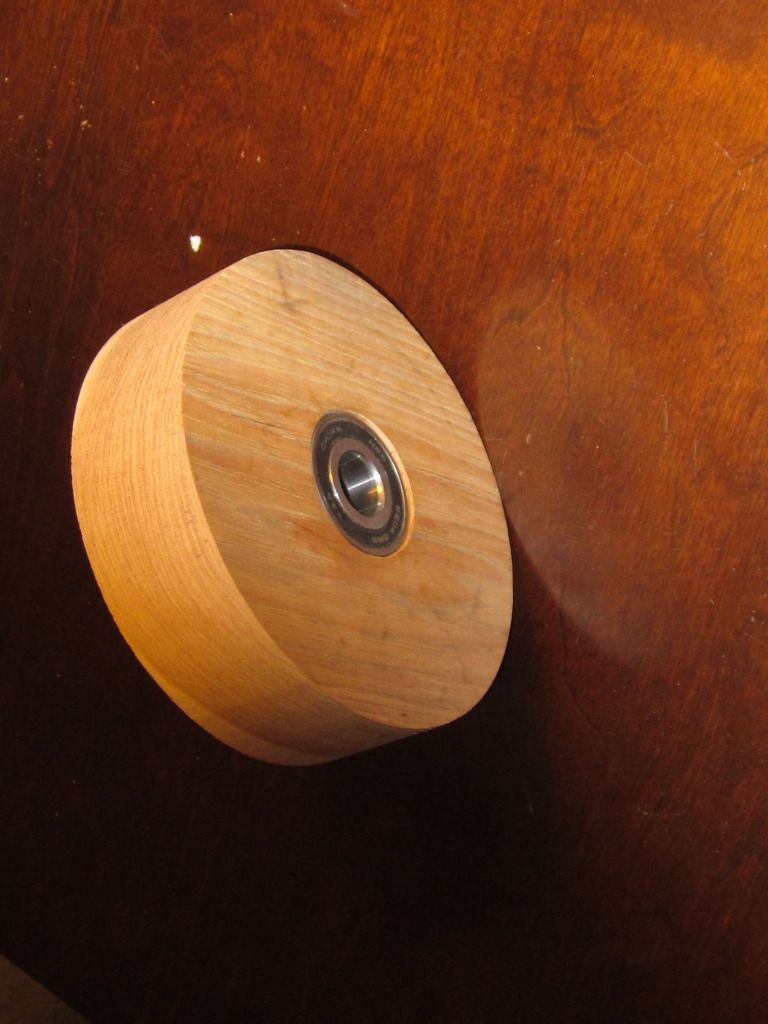
Re: my next Project
Posted: Sun Sep 02, 2012 8:13 pm
by delraydella
Be careful when rolling thinwall tubing, the tighter your bends, the more the tube walls will want to flatten out giving you an oval shape. You can try filling the tube with sand and capping the ends to help keep it round when rolling it. I've never tried this before, but I've talked to people who've done it and they say it works.
Other Steve
Re: my next Project
Posted: Sun Sep 02, 2012 8:36 pm
by Otto Nobedder
Sand works very well, and thanks for posting. I don't believe that trick escaped my addled brain!
Unless the bend is very close to the end of the tube, it doesn't need more than some masking tape for a cap.
Tape one end of the tube, pour sand in from the other, and "tamp" the tube on the table, add more sand, repeat. This works almost as well as a mandrel for keeping the tube from collapsing while bending.
Good thinking, Other Steve!
Steve S.
Re: my next Project
Posted: Mon Sep 03, 2012 1:15 am
by CraigLam
Dudes, thanks! I never would have thought of that. Tomorrow I'll make the stationary part. I'll post a picture of that. I ordered the 7/8" carbide bit on ebay and they said it will be here by the 6th. I have to set up the router to plow the center. When I do, I have to make sure that each part is routered from one side then those sides are facing the same way. Keep in mind that the dies are not exactly one half, but, alittle shy. When the unit is put together and the halves are pressed together, there should be a little gap so the dies compresses the tube not each other.
Re: my next Project
Posted: Mon Sep 03, 2012 4:58 pm
by CraigLam
Happy Labor Day, everyone. Not much excitement here. Went to the garage and worked on the stationary part of the bender. The setup that I used to make things perfectly round, worked pretty good. It has to be very close. If not, then the bender will wander. The roller part needs a little more work, it's not absolutely perfect. Next, are the metal pieces. That might have to wait 'till next week.

Roughed out on the band saw.
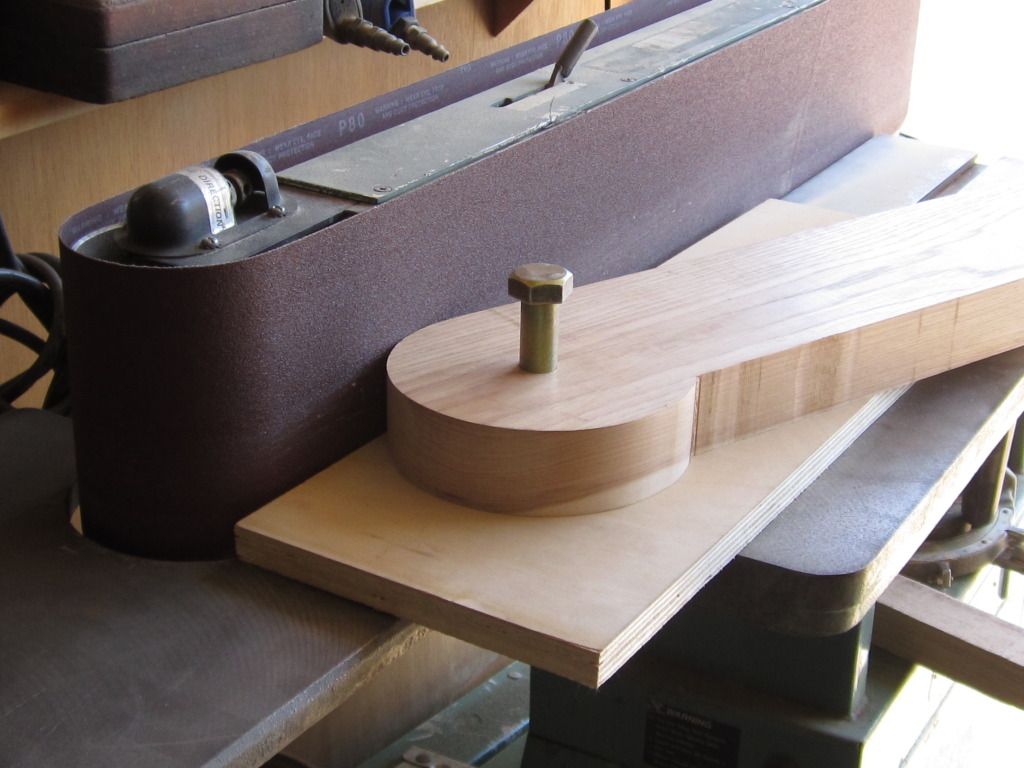
The ply is "T" nutted to the platten. Ply is tapped forward until the sanding belt just touches. Then spun around.
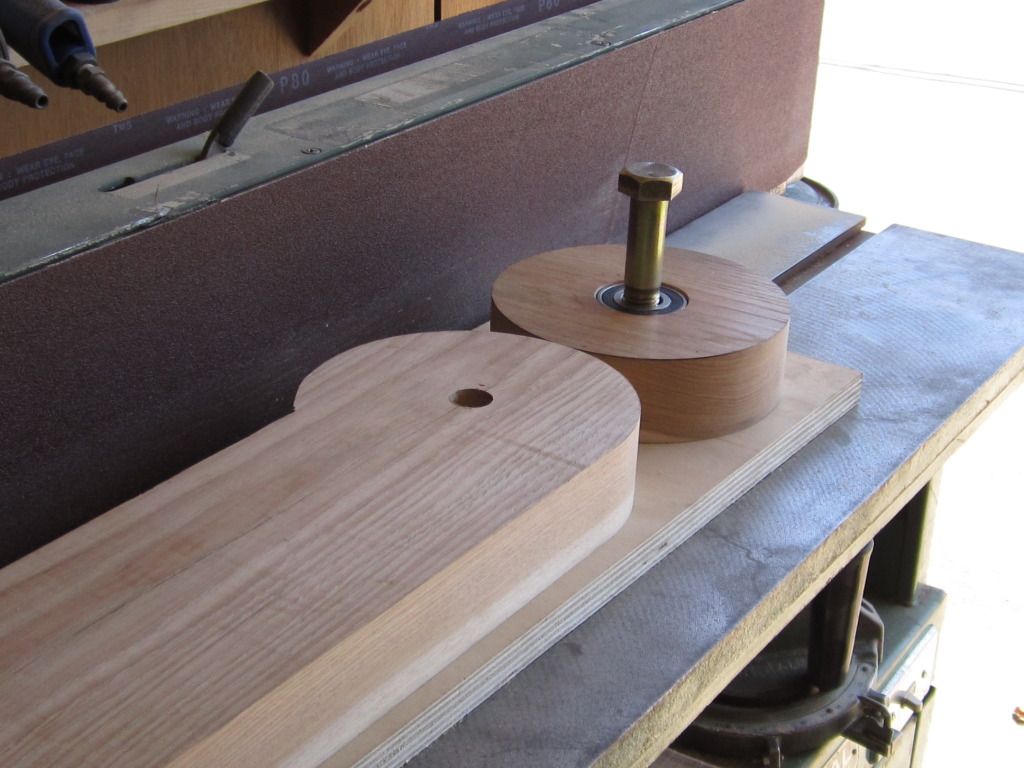
Re: my next Project
Posted: Tue Sep 04, 2012 6:19 am
by weldin mike 27
Hey there,
I would never in a million years thought of making a tube bender out of wood. I hope it works out for you.
Mick
Re: my next Project
Posted: Tue Sep 04, 2012 1:33 pm
by CraigLam
I think that most of the skepticism here, is that some people think that all wood is soft. Some of us, and alot of people on this forum, have worked with hardwood. Hickory is extremely hard. Most commonly, it's used for hammer handles. Almost impossible to drive a nail thru it. And when you get to the exotics, there are some woods that are ornamental only. You can't glue them or nail them. Why wood, then? Cost. The pieces you are looking at, is only half of what I bought. 7"x72"x1 3/4" th. costs about 30 bucks. Equivalent size in metal would be ridiculous. I saw some dies on the web that were made from plywood. Too soft. However, they did work. The only other difference between the wood and the metal, and it's a big difference, is wear. The metal will last alot longer than the wood. How long? I don't know. The only way, is to make like 10 mini bikes, and see how the die looks afterwards. The advice I got to fill the tubes with sand, was brilliant. The 7/8" core box router bit should come tomorrow. After I'm done routering, I'll post some more pictures.
Re: my next Project
Posted: Tue Sep 04, 2012 4:11 pm
by weldin mike 27
Hey,
When you put it like that, the light starts shining. Tool handles , of course, hard and strong. I guess im just conditioned when it comes to steel. Jarrah and Box Iron Bark are two hard woods from australia. They used to use Iron bark on the the bows of Icebreakers back in the old days.
Mick
Re: my next Project
Posted: Tue Sep 04, 2012 11:07 pm
by Ultralow787
This is an interesting idea! Keep the pictures coming. I'm anxious to see the complete bender in action!
Re: my next Project
Posted: Wed Sep 05, 2012 5:40 pm
by Otto Nobedder
I'm curious, too.
Considering the material costs, replacing dies should be rather inexpensive, assuming they hold up well to multiple bends. I'm also curious as to what cut (quarter-sawn, etc) and grain orientation hold up best.
Steve S.
Re: my next Project
Posted: Thu Sep 06, 2012 9:04 pm
by CraigLam
So, I'm working in the shop and the power goes out. Just my luck, it's not the breakers, but, something else. So, I went back in the house and the router bit came. Something good, finally. This will rout out the dies to 7/8". All bicycles, mini bikes, go karts, literally all things of this nature are made from 7/8" tubing. It's and industry standard, I guess. After I rout this, I'll sand it very fine, seal and coat it with a polymer. When I start to bend, I'll oil it up to reduce the friction. The follower arm is done and I'm in the middle of the stationary arm. Anyway, here's the router bit. Hopefully, the electrician will come tomorrow.
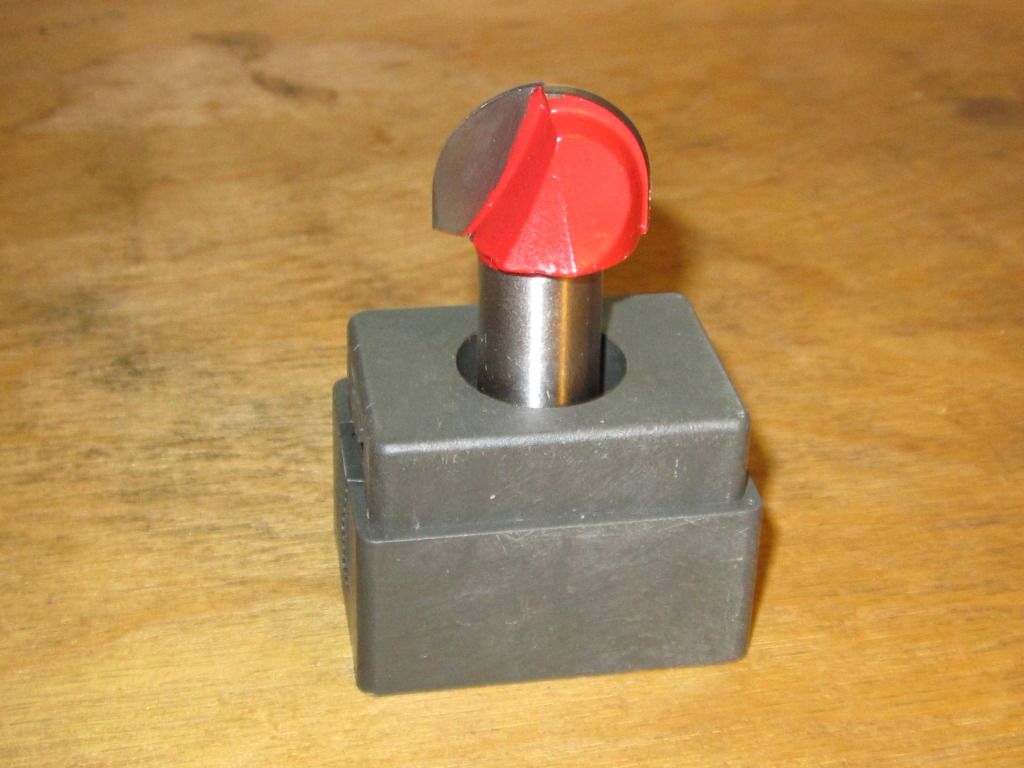
Re: my next Project
Posted: Thu Sep 06, 2012 9:21 pm
by delraydella
I only have 2 questions......
1.) How much was the bit?
2.) Is that a coffee cup stain on your bandsaw table?

Re: my next Project
Posted: Fri Sep 07, 2012 12:08 am
by CraigLam
1. The router bit was a special. $2.03
2. Yes, that's a coffee stain. I also have one on my drill press, table saw, edge sander, work bench and two on my shirt.
Now, that cost is brought up, I've spent $28.00 for the Hickory, $24.00 for the metal, $8.00 for the bearings, $10.00 for the bolts, and $2.03 for the bit. So far, that's $72.03. The only thing left is the allthread, 4 nuts, and the extension pipe, which I already have. Altogether, about $80.00 compete. The cheapest bender I could find, was about $150. And that was just for the dies. Hopefully, the juice will be back on tomorrow and I'll have the finished product for some photos.
Re: my next Project
Posted: Fri Sep 07, 2012 6:19 pm
by Otto Nobedder
Nice budget!
You *may* be dissapointed with allthread, though it costs little to find out. You may have to go to grade 5 hardware with a shank that matches the depth and diameter of your bearings to keep the tolerances you need. (Most readily available allthread is grade 3, the diameter will be a bit smaller than the stated size, and the ultimate strength will be the cross-section of the "bottom" of the threads.)
My $0.02, for what that's worth these days.
Steve
Re: my next Project
Posted: Fri Sep 07, 2012 8:34 pm
by delraydella
I agree with Steve/Otto, you will need something much stronger to take the pressure. Oil hardened drill rod might work very well for this, but it can be a pain to thread without a lathe. If you give me the diameter and threading I can make it out of drill rod for you,but i wouldn't be able to have it for you til next week.
Re: my next Project
Posted: Fri Sep 07, 2012 9:19 pm
by CraigLam
Re: my next Project
Posted: Tue Sep 11, 2012 11:38 pm
by CraigLam
I set up the router table today and routered the pieces. If you look at the side view, you can tell that when the pieces are 1/16th apart, it forms a circle. That will allow me to compress the tube and get good pressure to form the bend. I should try to bend my first tube by thursday, hopefully. I went on line and found one other guy that made his die from maple. He actually made two halves using a cove bit. It came out really good.
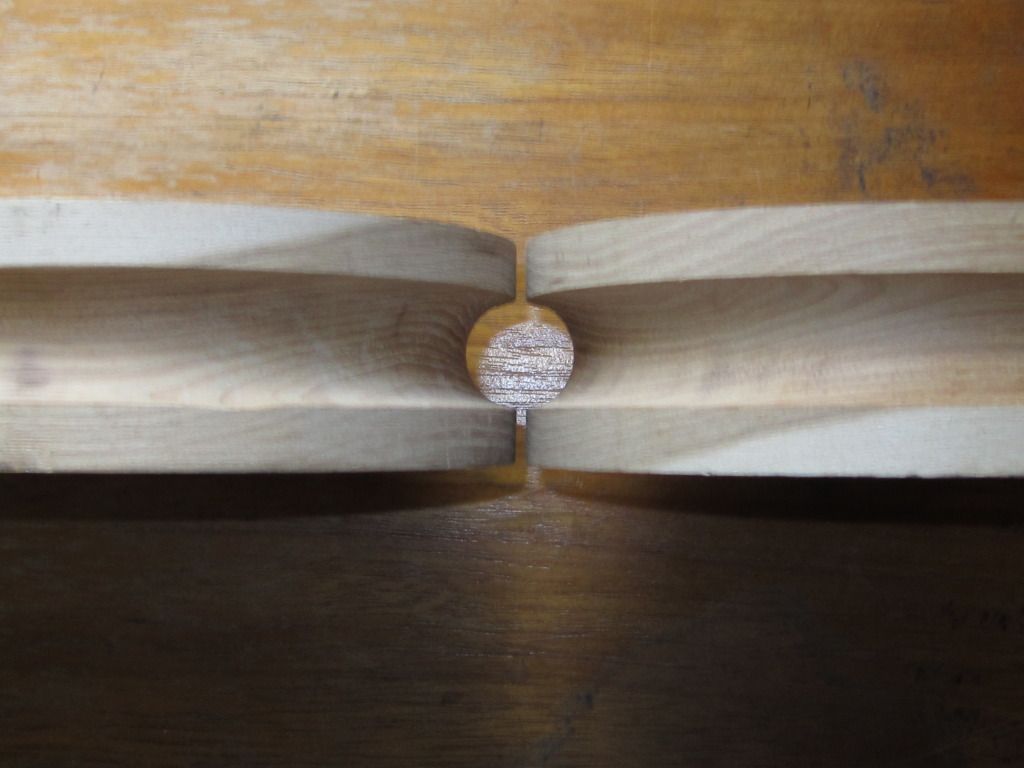
I also had to elongate the holes in the outer part so the wheel has room to move forward against the stationary wheel. Tomorrow I pick up the threaded rod,
1 1/4".
Re: my next Project
Posted: Wed Sep 12, 2012 2:11 am
by weldin mike 27
Hey there,
Looks a million bucks.
Mick
Re: my next Project
Posted: Wed Oct 03, 2012 8:09 pm
by CraigLam
Well, good news and not so good. First, the good news. My tube bender works! Not so good, it will only bend 7/8" thin wall (EMT). I'm gonna build a small mini bike first with the 3 h.p. in the photo. Thin wall should hold up. Later on, I'm gonna go to metal depot and pick up some thick aluminum, 1" or thicker, and make my own aluminum dies. I'm gonna use my drill press with a verticle tool rest and I have a set of high speed lathe tools. But, the bender worked well. I also welded a 2' leg on it for support. It needs a longer one.
http://s1207.beta.photobucket.com/user/ ... sort=6&o=2
You can see why the first dies didn't work.
http://s1207.beta.photobucket.com/user/ ... sort=6&o=0
http://s1207.beta.photobucket.com/user/ ... sort=6&o=4
This is the new die I made.
http://s1207.beta.photobucket.com/user/ ... sort=6&o=1
This is the new bender. I got it from u-tube.