Today, I bend. The first real day I started the mini bike project. Every step of the way is recorded. Angles, bends, degrees of bends, everything. I'm not sure when I start selling these, to sell them complete, which is the best, or as kits. Some companies sell these as kits that people weld them together. That's nice, but, too much can go wrong. It's better to sell them already complete and you just assemble the parts. I'll figure out the plan when I make a few units.
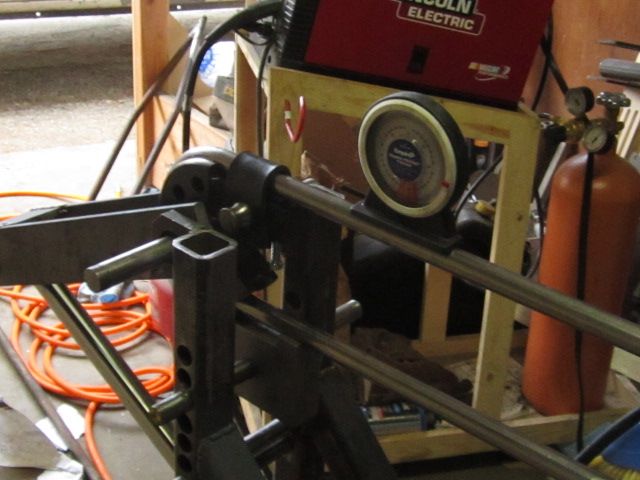
Here you can see the angle finder. Simple, but, it works good.
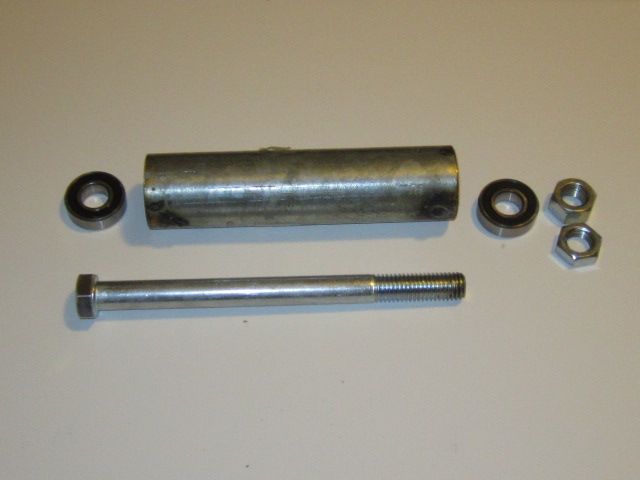
Fork pivot with bearings instead of just a 5/8" bolt.
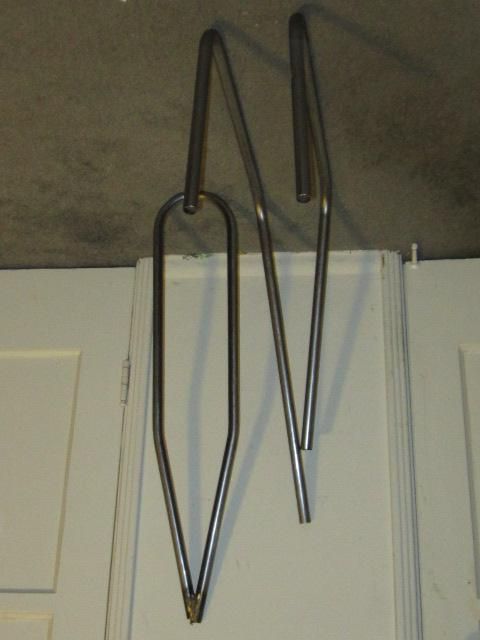
I've made the side frames. They are a compound angle. This took some layout. The back and the bottom rails are to be parallel. But they angle in at the fork pivot. The next step is to notch them to fit into the pivot tube. After this is the fork plates.