First off, English is not my main language, but i'll do my best!
I'm 22 years old, live in Norway and just got my certificate of completed apprenticeship? as a pipefitter (2 years in school and 2 years in work)
Anyhow, this project started with replacing an old wooden pier with a longer, more solid steel pier (Galvanized).
So i had to weld 42 meters of T-bars on the sides, so that we could adjust the spacers for the boats
About 10cm of weld on top and underneath, NST 7016s 2,5 elektrodes, used about 400 all togheter. I should have gone for 3,2 electrodes

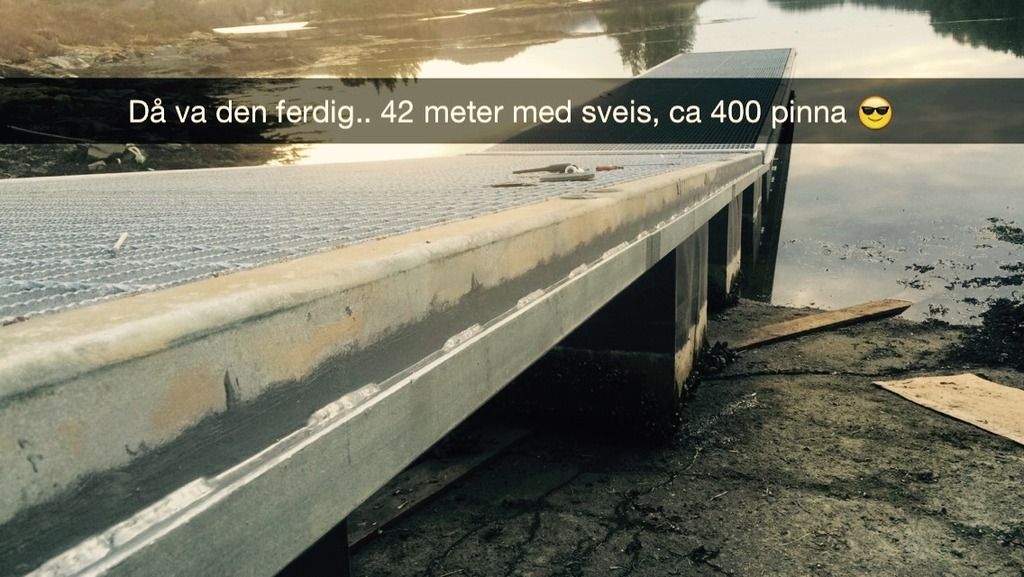
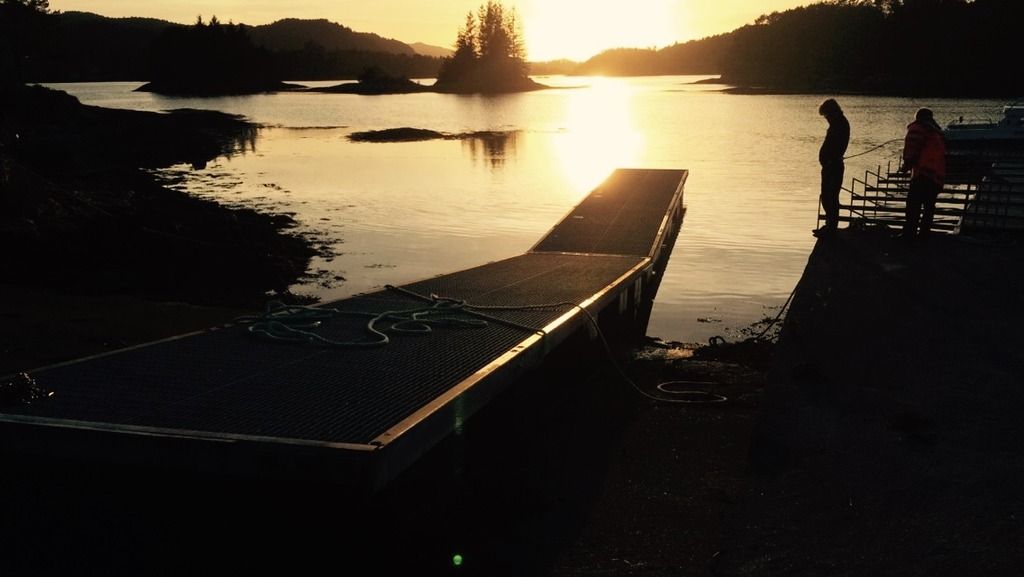
Meanwhile, we were looking for a aluminium gangway, but it costs around 2000$ - 3000$ , so i decided to make one for alot less, but with galvanized steel.
I used a gangway made by professionals as a starting point considering steel thickness and style. Mine was 2 meters longer so i added some millimeters on the frame and pipes. I used google sketchup to draw and figure out some measurments. I ordered all the material through my workplace, the cost was about 1000$.
Galvanized pipe 33,7 x 3,2 - 24 meter and 42,4 x 4,5 - 24 meter
Angle iron 75 x 50 x 8 - 18 meter
T-bars 50 x 50 x 6 - 6 meter
It's 8 meters long, and I decided to make two parts of 4 meters, so that the transportation when it was finished would go smoother.
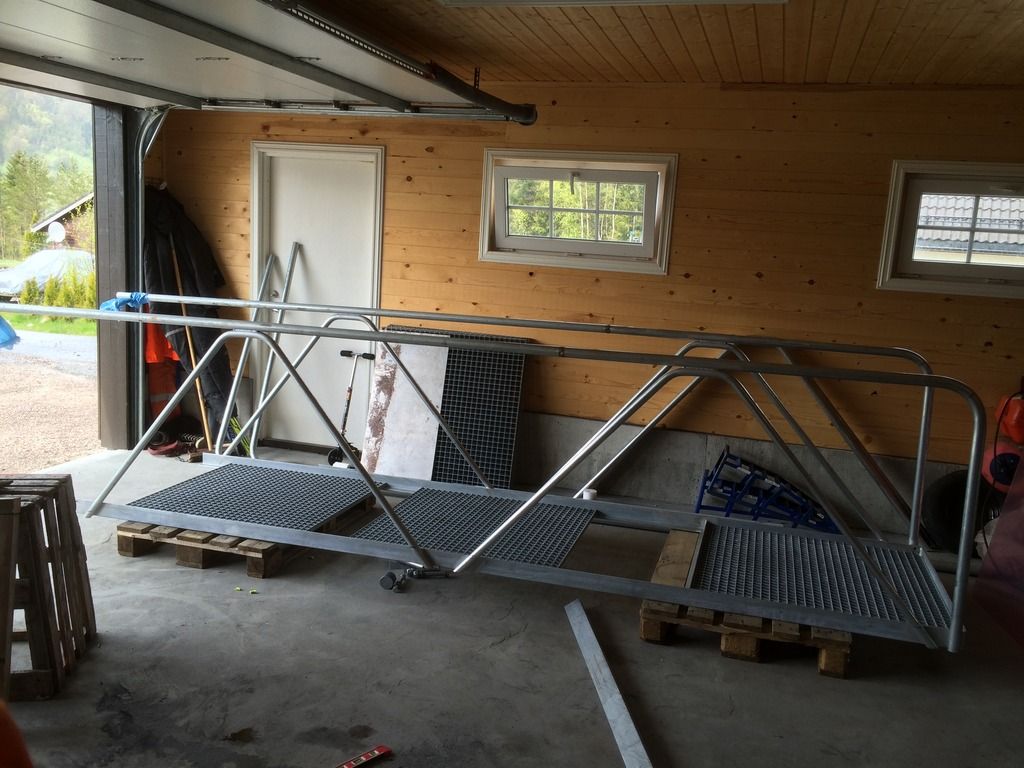
T-bars, One on each meter, making the frame less spaghetti, and works as "slots" for the gratings
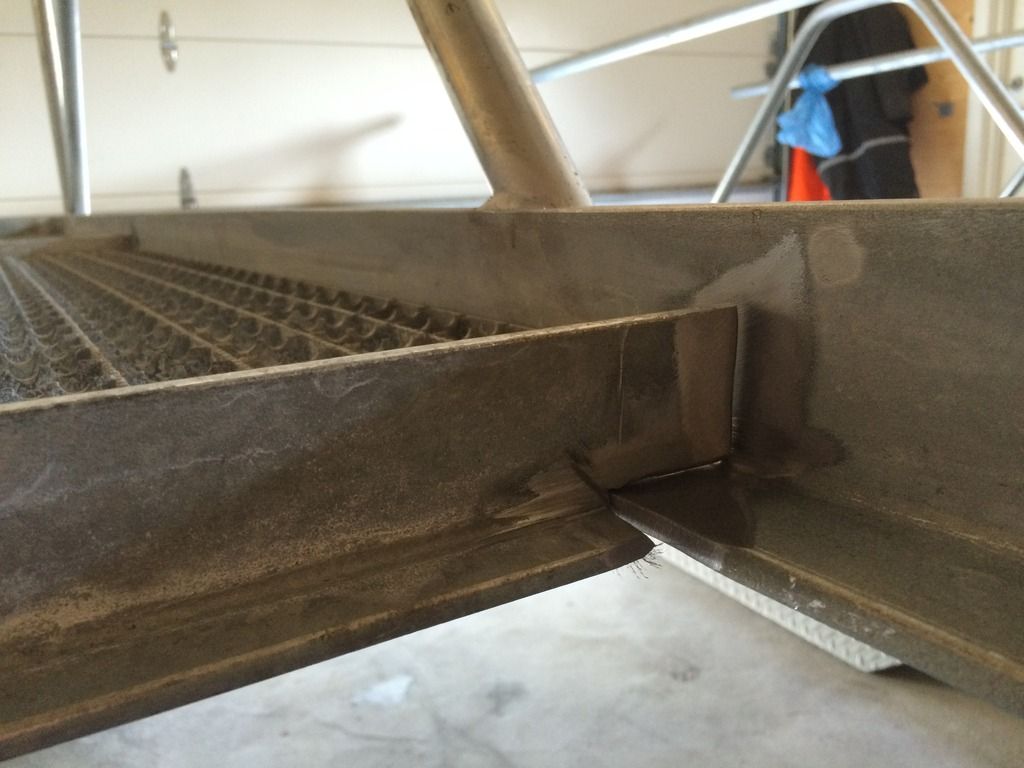
MIG welded the top and side railing
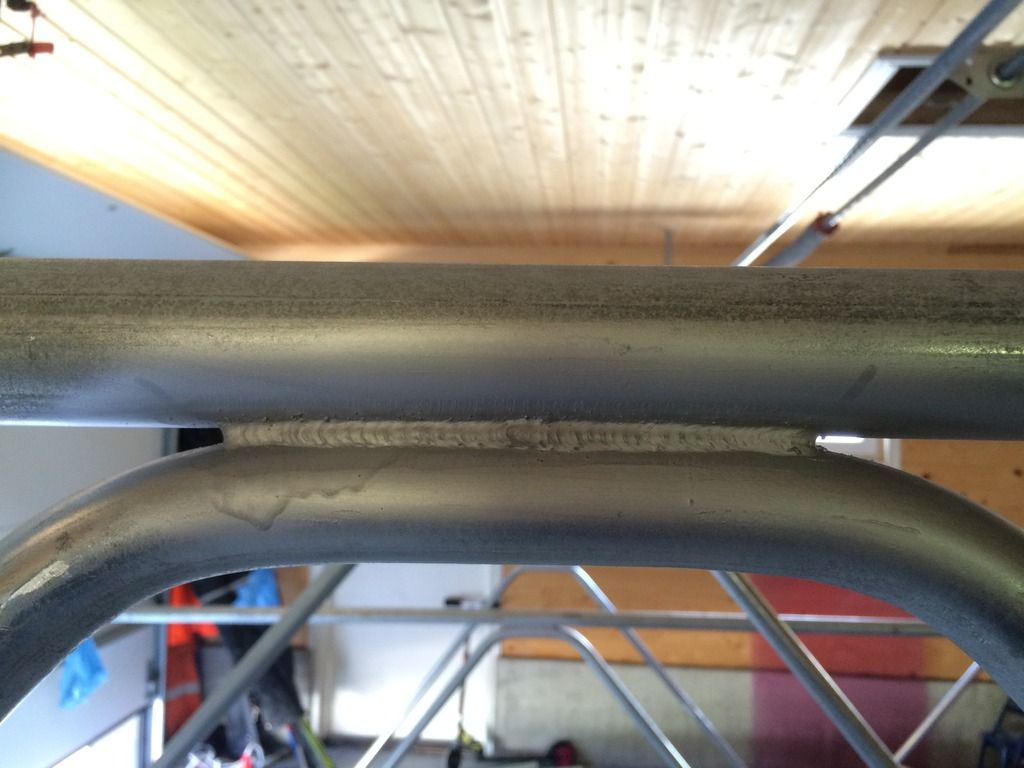
MIG welded railing to the frame, one pass downhill and the last one uphill
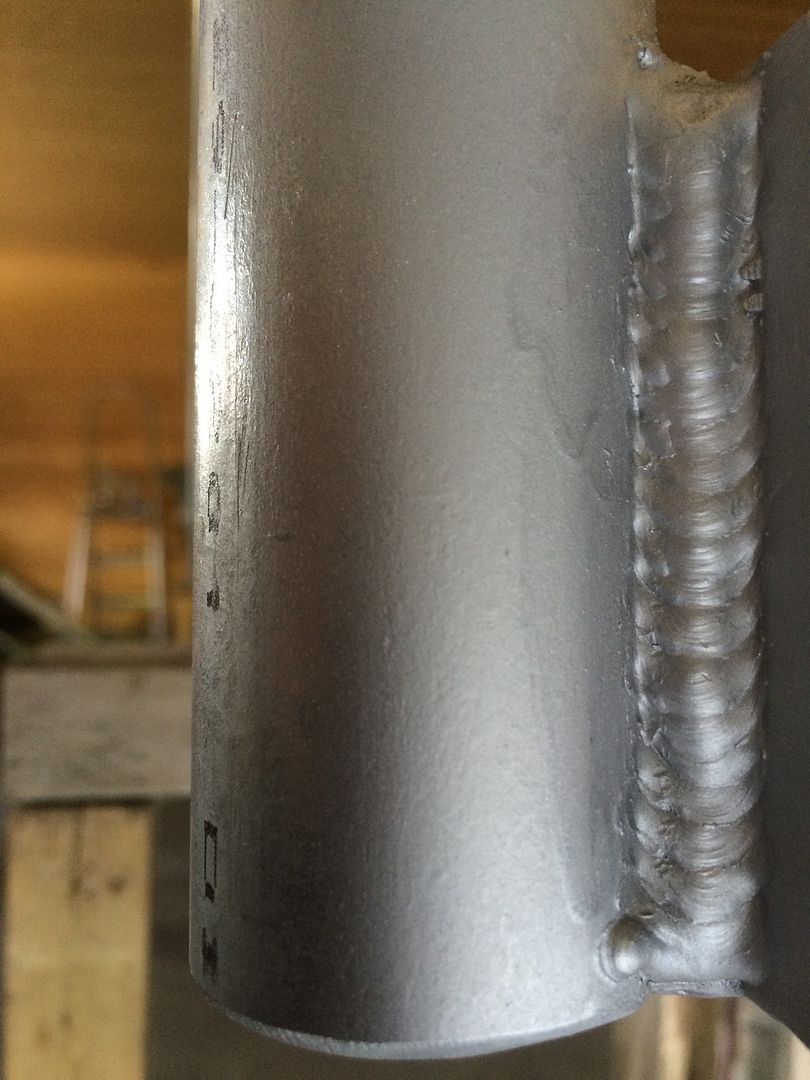
Some uphill stick welding, with a downhill mig first
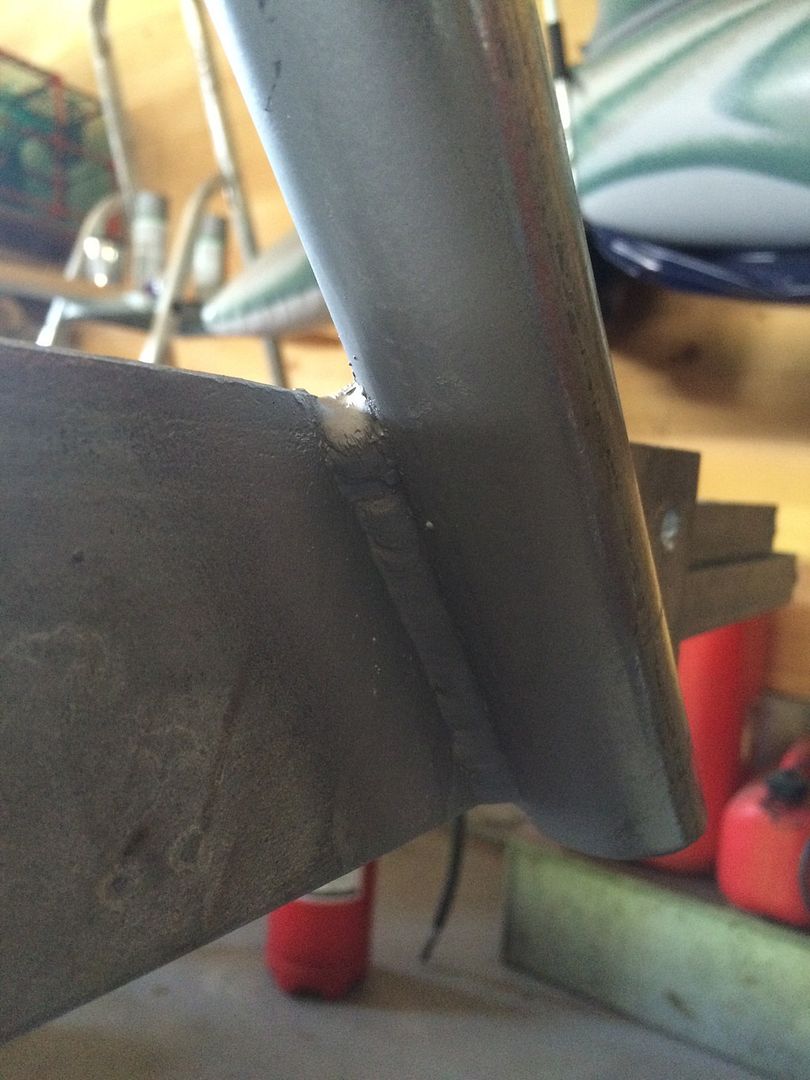
All the welds were cold galvanized shortly after welding, and later on we used some heave duty shipyard painting on all the welds. Everything were painted 1 stroke afterwards,
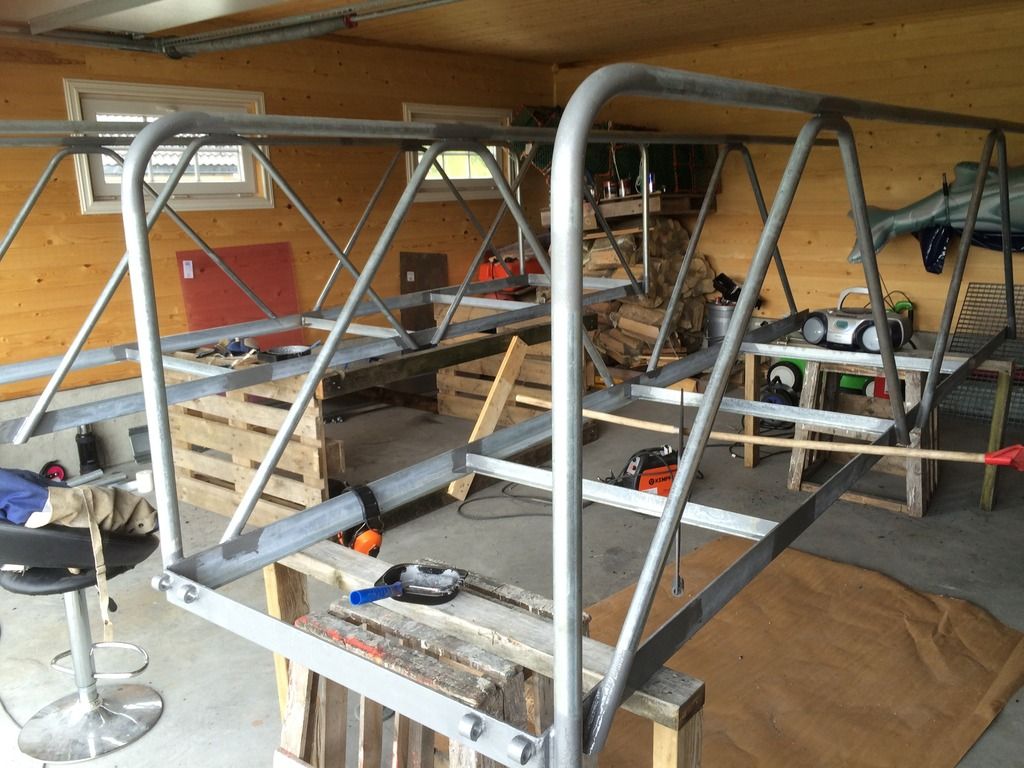
Plate to be fitted on land, and ofcourse we painted it.....
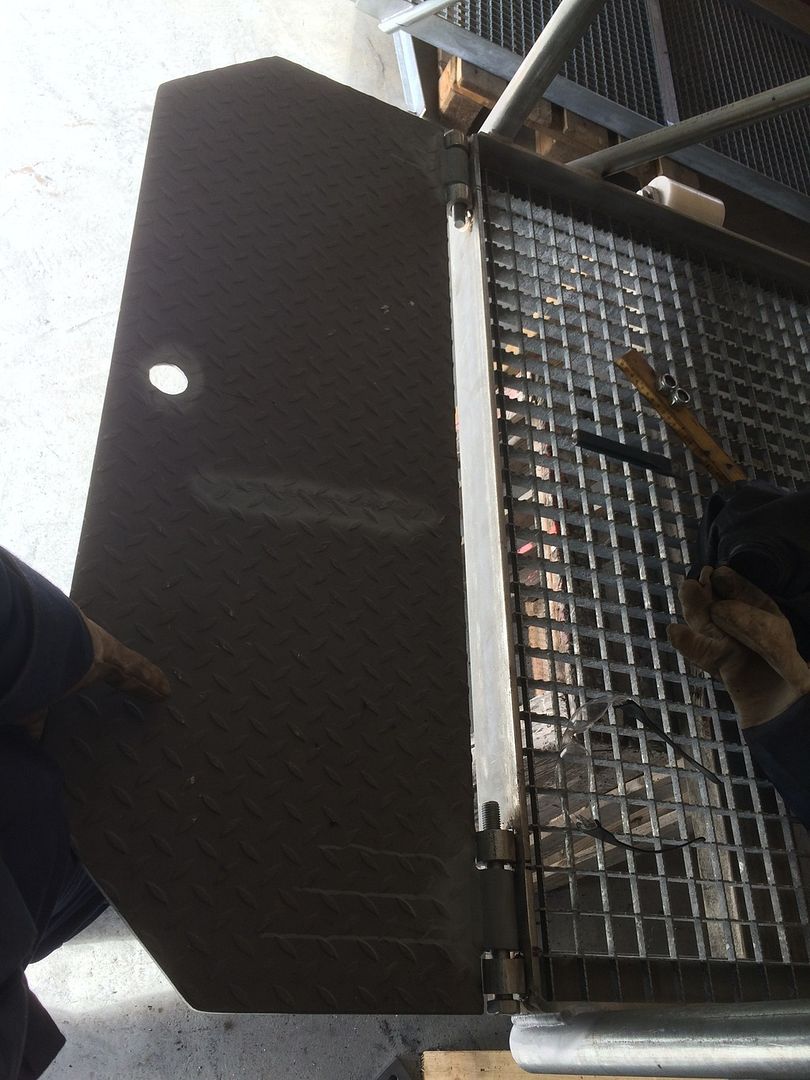
Transportation went smooth, both fitted in one car.
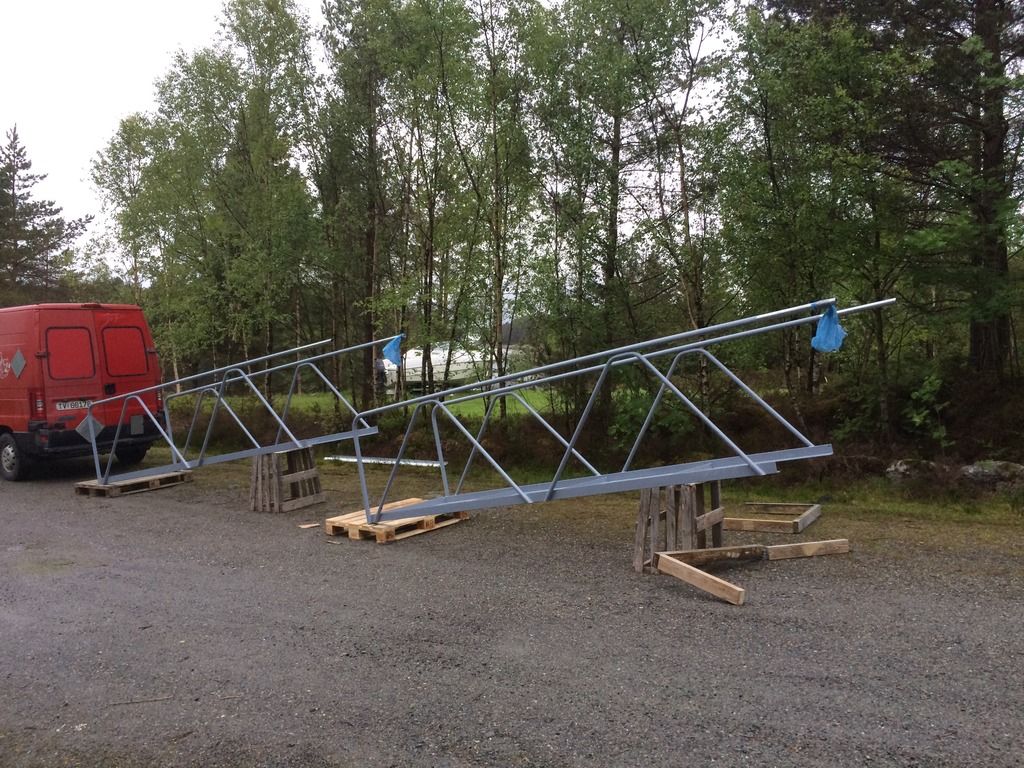
Feel free to comment, anything! And i will post more when it's all done!