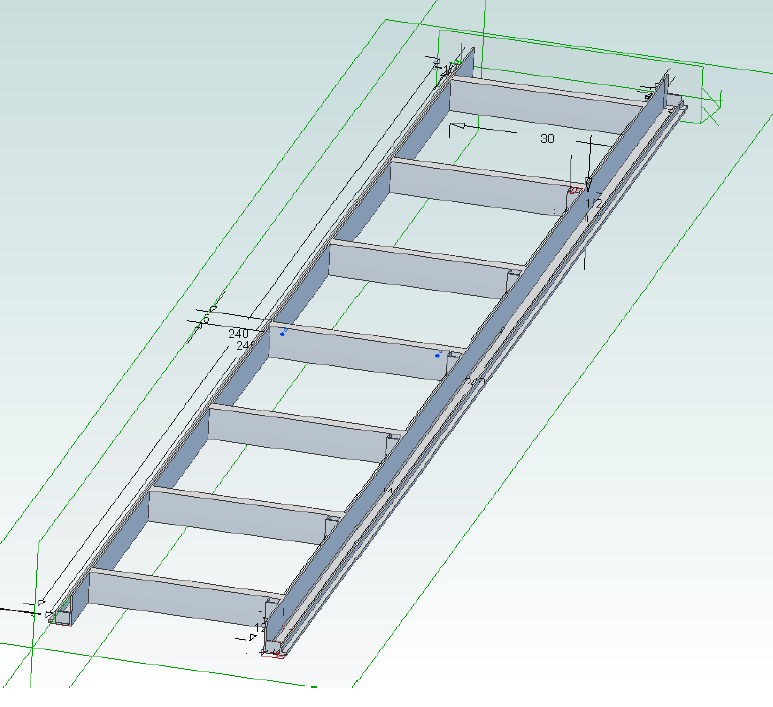
What welding projects are you working on? Are you proud of something you built?
How about posting some pics so other welders can get some ideas?
How about posting some pics so other welders can get some ideas?
I have accumulated all the necessary hardware to build my portable sawmill. The only thing left to buy is the structural steel. The main frame is 20 feet long with at least 6 cross braces. My concern is warpage along the entire length of the frame. Looking for suggestions. I am a hobbyist and have never tried anything on this scale before. All welding will be done with an ESAB stick welder.
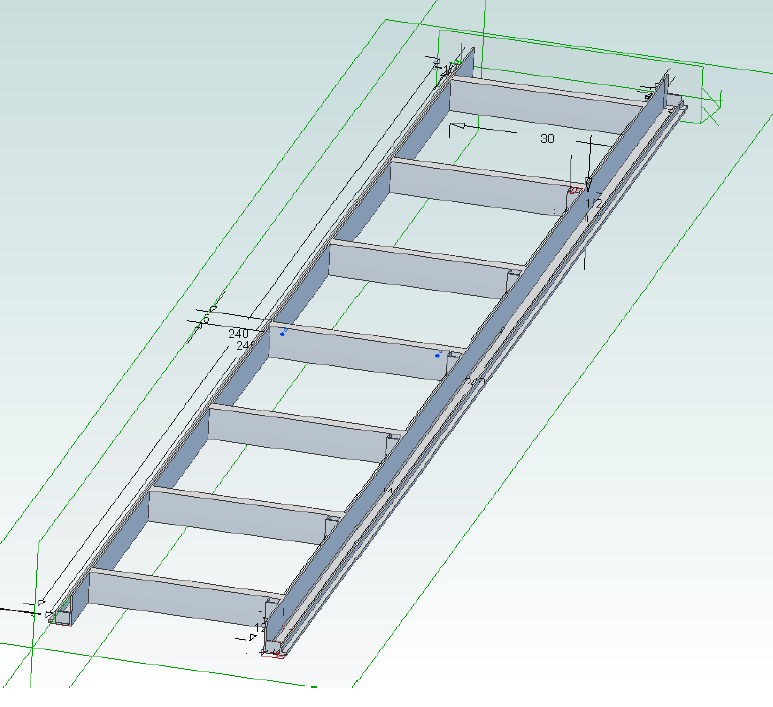
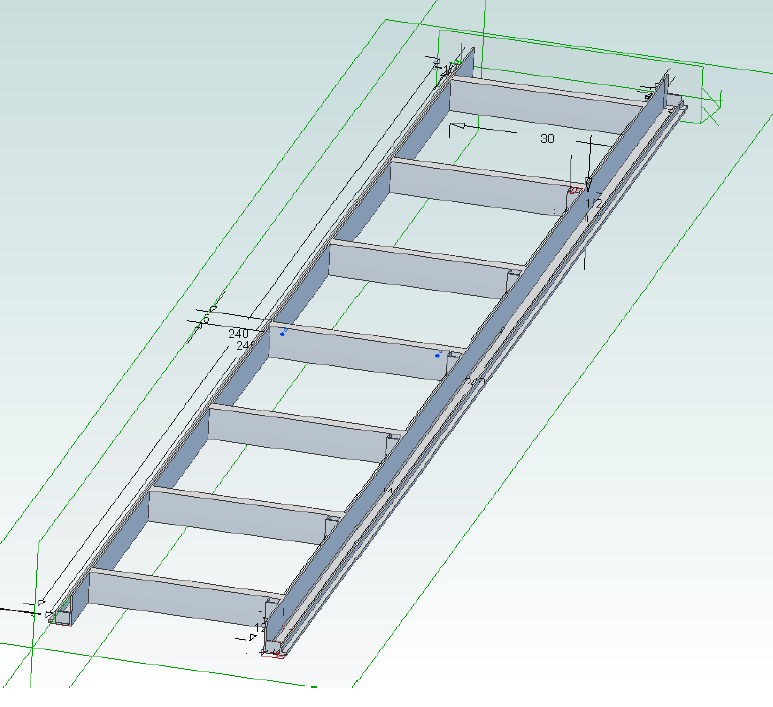
Sal Monella
- Sal Monella
-
New Member
-
Posts:
-
Joined:Sun Mar 01, 2015 9:08 am
Very best way is to eliminate most welding from the construction. You can weld sub-assemblies then bolt them to the frame rails.
I would start by redesigning you frame section to hopefully incorporate a single member, meaning one piece of stock, sufficiently stiff in the relevant directions, such a a t- bar, an angle section, a Jr. beam or a channel. Industry has moved to square or rectangular tube for frame sections because of simplicity of design due to it's resistance to bending in all directions as well as the simplicity of fabrication but the cost difference is significant and in your case it seems as if you need an edge to act as a rail.
If you must weld it, the basics are;
use as little weld as possible
skip weld
stagger your welds side to side
If you put equal amounts of weld on each side of a member, it will not bend.
Clamp the work securely to a good sized I or H beam.
Pre-bend the work in the opposite direction by inserting shims between the beam and the work.
Prepare to straighten the frame somewhat regardless, which is why I would bolt it together. As it is, you will likely need to straighten the stock before you weld it.
I would start by redesigning you frame section to hopefully incorporate a single member, meaning one piece of stock, sufficiently stiff in the relevant directions, such a a t- bar, an angle section, a Jr. beam or a channel. Industry has moved to square or rectangular tube for frame sections because of simplicity of design due to it's resistance to bending in all directions as well as the simplicity of fabrication but the cost difference is significant and in your case it seems as if you need an edge to act as a rail.
If you must weld it, the basics are;
use as little weld as possible
skip weld
stagger your welds side to side
If you put equal amounts of weld on each side of a member, it will not bend.
Clamp the work securely to a good sized I or H beam.
Pre-bend the work in the opposite direction by inserting shims between the beam and the work.
Prepare to straighten the frame somewhat regardless, which is why I would bolt it together. As it is, you will likely need to straighten the stock before you weld it.
Return to “Welding Projects - Welding project Ideas - Welding project plans”
Jump to
- Introductions & How to Use the Forum
- ↳ Welcome!
- ↳ Member Introductions
- ↳ How to Use the Forum
- ↳ Moderator Applications
- Welding Discussion
- ↳ Metal Cutting
- ↳ Tig Welding - Tig Welding Aluminum - Tig Welding Techniques - Aluminum Tig Welding
- ↳ Mig and Flux Core - gas metal arc welding & flux cored arc welding
- ↳ Stick Welding/Arc Welding - Shielded Metal Arc Welding
- ↳ Welding Forum General Shop Talk
- ↳ Welding Certification - Stick/Arc Welding, Tig Welding, Mig Welding Certification tests - Welding Tests of all kinds
- ↳ Welding Projects - Welding project Ideas - Welding project plans
- ↳ Product Reviews
- ↳ Fuel Gas Heating
- Welding Tips & Tricks
- ↳ Video Discussion
- ↳ Wish List
- Announcements & Feedback
- ↳ Forum News
- ↳ Suggestions, Feedback and Support
- Welding Marketplace
- ↳ Welding Jobs - Industrial Welding Jobs - Pipe Welding Jobs - Tig Welding Jobs
- ↳ Classifieds - Buy, Sell, Trade Used Welding Equipment
- Welding Resources
- ↳ Tradeshows, Seminars and Events
- ↳ The Welding Library
- ↳ Education Opportunities