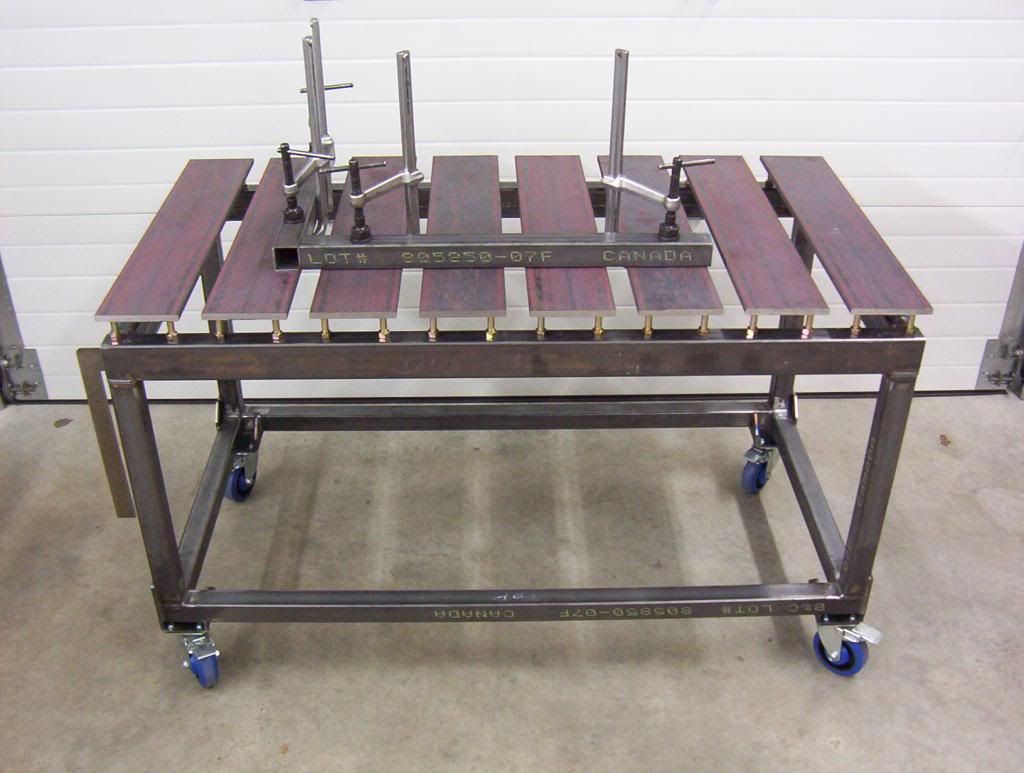
http://www.garagejournal.com/forum/show ... 45&page=2
I originally wanted to copy his design except counter sink allen head tapered bolts into the plate, tap threads into the tube, and have them adjust the plate up and down with jam nuts rather than weld the bolt head on the backside of the plate and hole saw tons of holes into the tubes for adjustment access.
Thing is, in his post he says the 1/2 plate is more rigid than I found out. It's also not flat. I grabbed a piece at work and pushed down on it with 1 hand across a 25" span and could see lots of flex. So my next idea is to use channel, but it would probably make clamping quite difficult. Rectangle tubing 2x6 I am considering also. Has to be flat and rigid.
Any ideas? I work as a fabricator by trade at a shop so I have access to lots of options for material.