
Starts with the foundation, which in this case is a welded mounting pad, angled to fit a transom edge of a boat. It will have fasteners from two directions, which is a good thing in this instance.
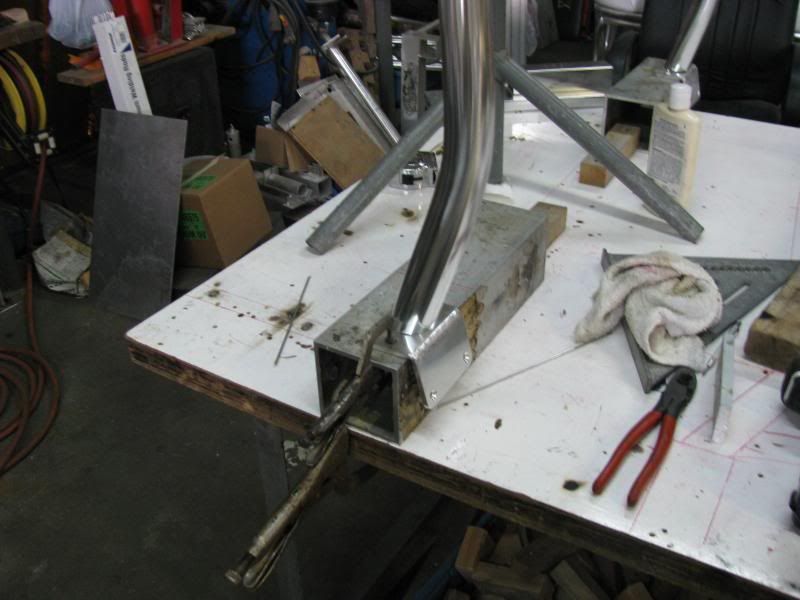
Then bend a hoop, with an arc across the top. I arch the pipe so when I weld the ski rope thimble on the center, it doesn't sink the pipe in the center, which ends up being really noticeable, at least to me.
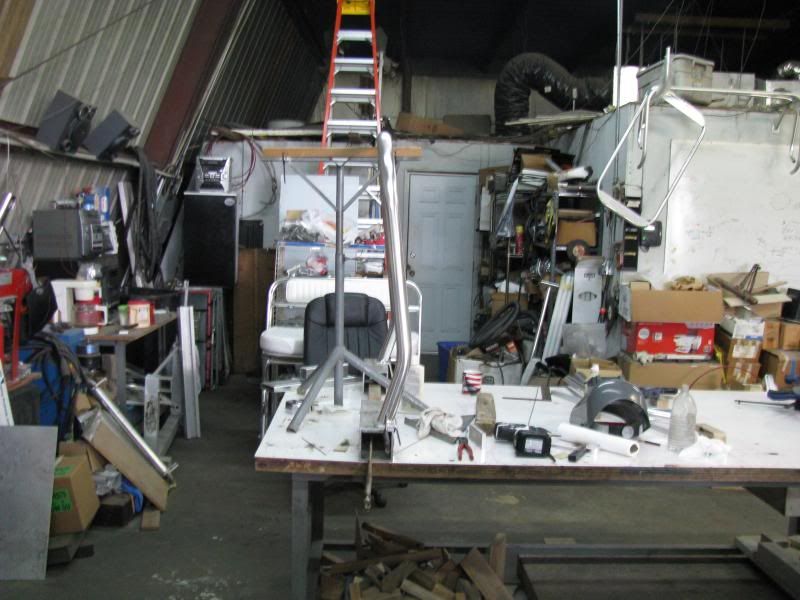
This thing tapers forward 9 degrees, so the front arch needs to be fabricated narrower than the rear. But it's Monday, and I am nailing my targets so far and I am happy about this. I was feeling cocky so I added kink bends near the bottom which means the bends will need to be articulated to fit the 9 degree taper.
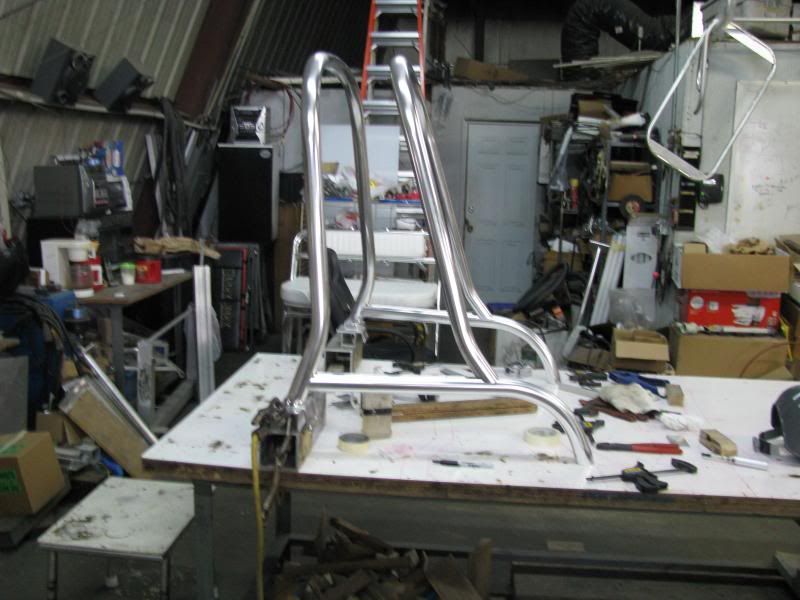
And then to have the arc of arches line up with one leaning back 10 degrees (it's a different amount of arc to make this work) more than the other is something a lot of folks would not think about, but it matters.
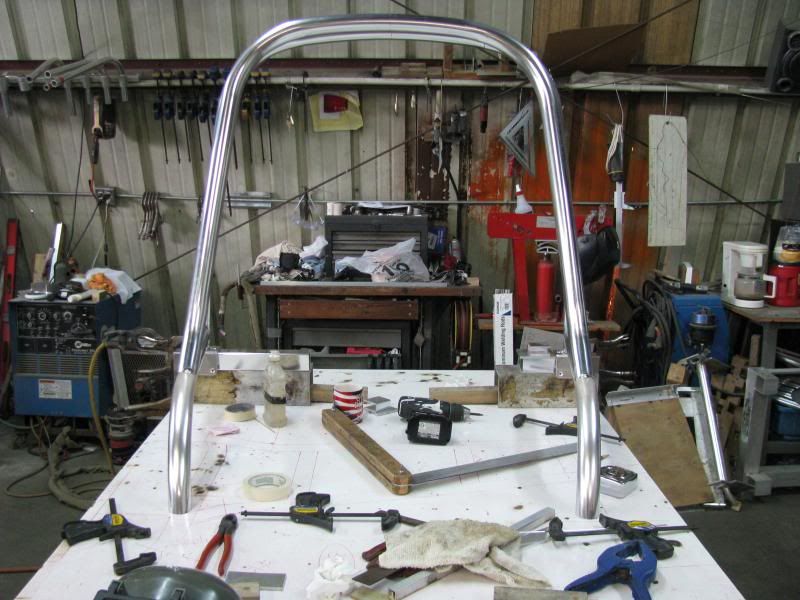
Otherwise, the top rungs will not be level with the side ones.
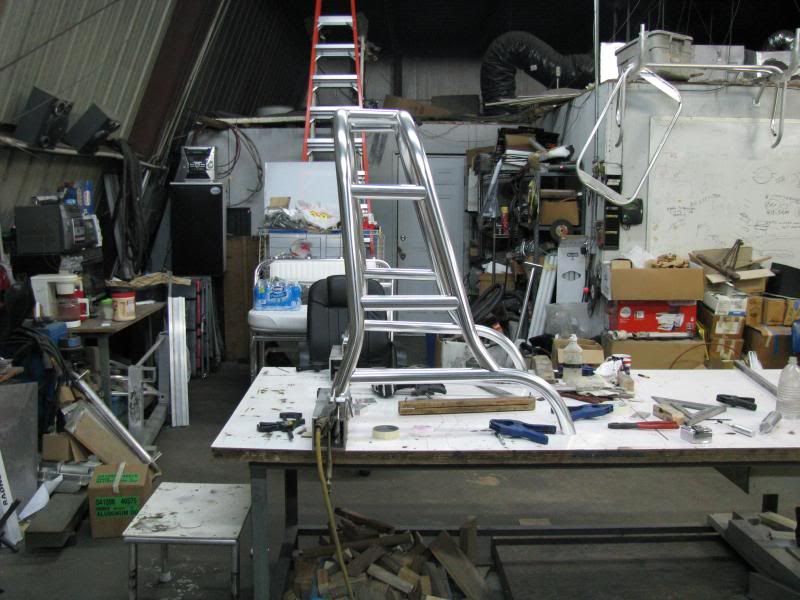
I even managed to think ahead to taper the top rungs as well, so that everything ends up graduating symmetrically. It's a wake board/ski arch for the back of a boat. It is to have folding seat backs on it as well. They need to fold so that the hatches under this thing can still be opened. The hatch layout is why this needed to be tapered in the first place. Tomorrow I get to weld it up. As it is, it sits on the boat as if it grew there. It had to clear hatches and the outboard motor tilted in all positions, a dive platform on the back of the boat as well.
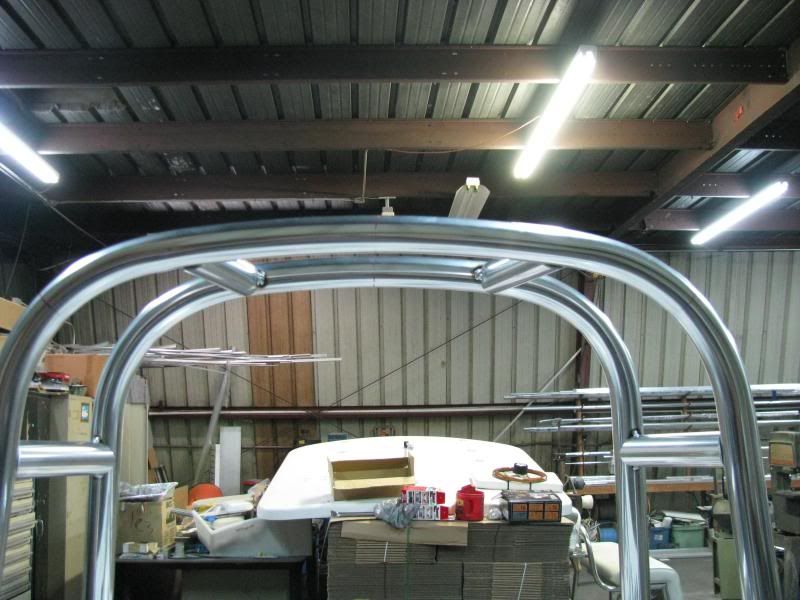
Anyway, it was a fun project. There was no extra pipe for errors and ended up using scrap for the rungs.