Page 1 of 1
large beads on thin aluminum
Posted: Wed Jun 08, 2016 2:27 pm
by vernd
I have seen a lot of race car related aluminum welds on thin material where the weld bead seems very wide or large , however burn through on the back side is non existent. Specifically on pit pal products ( utility trays and the like from 16 gage). How do they accomplish this. I would normally use wire size same as material thickness ( 1/16 in this case) Do you think a larger filler wire would give this effect?
Re: large beads on thin aluminum
Posted: Wed Jun 08, 2016 2:59 pm
by RamboBaby
You'll probably need a backing plate. Stainless or copper. If you have an inverter welder then triangle mode is designed for welding thin aluminum. Clamp it down good or its will bow up on you. You might wanna try pulsing with the peddle too.
Re: large beads on thin aluminum
Posted: Wed Jun 08, 2016 5:24 pm
by BigD
If you can, turning the frequency down helps too. Here's a pic of when I was goofing around with frequency. The narrow bead is 200 or 400 I forget now, the wide is like 40.

- welding-frequency.png (380.41 KiB) Viewed 1842 times
Re: large beads on thin aluminum
Posted: Wed Jun 08, 2016 6:00 pm
by Oscar
Re: large beads on thin aluminum
Posted: Thu Jun 09, 2016 12:06 pm
by Sandow
Great info Oscar. The only thing I'd add is that tip shape has a dramatic impact on melt pool width as well. A sharp point will produce a shallower and wider pool then a ball or blunt point. I agree with a backing plate being the way to go but a perfect set up requires pretty much all of this stuff to be at least considered.
-Sandow
Re: large beads on thin aluminum
Posted: Sat Jun 11, 2016 7:14 pm
by ajlskater1
You can accomplish that appearance if you pulse foot pedal as you dip and back off quickly after or use pulse function on the machine but I prefer to manually do it, I get better timing being in control vs a machine telling you when to dip.

- 20150220_212120.jpg (56.59 KiB) Viewed 1683 times
Re: large beads on thin aluminum
Posted: Tue Jun 14, 2016 2:27 pm
by Oscar
Sandow wrote:Great info Oscar. The only thing I'd add is that tip shape has a dramatic impact on melt pool width as well. A sharp point will produce a shallower and wider pool then a ball or blunt point. I agree with a backing plate being the way to go but a perfect set up requires pretty much all of this stuff to be at least considered.
-Sandow
Ask and you shall receive...
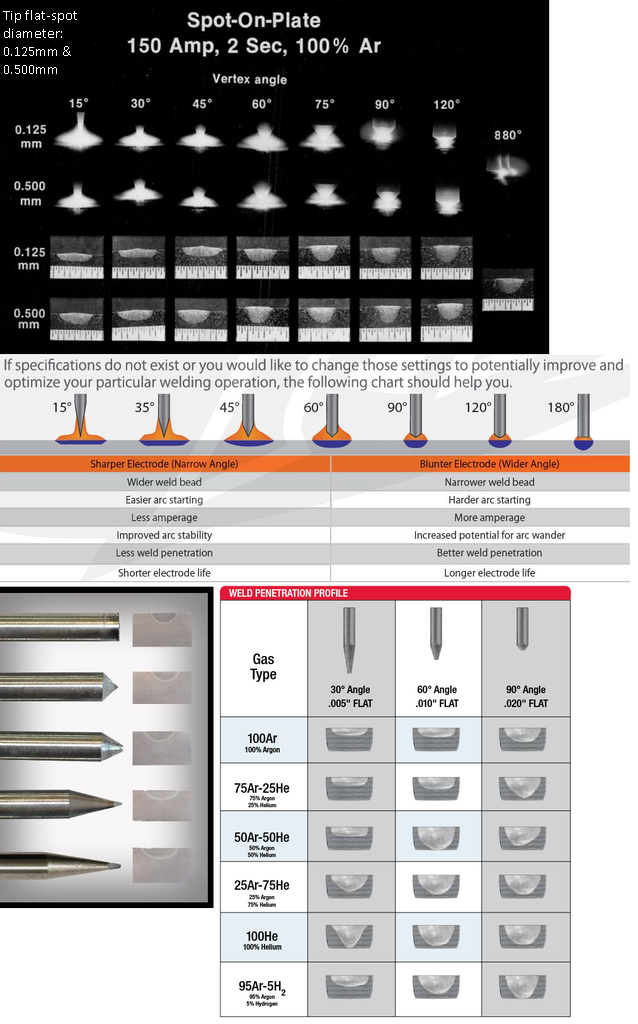
Re: large beads on thin aluminum
Posted: Tue Jun 14, 2016 4:17 pm
by rick9345
"Oscars'" posts.
