Tig welding tips, questions, equipment, applications, instructions, techniques, tig welding machines, troubleshooting tig welding process
Hollywood1
- Hollywood1
-
Ace
-
Posts:
-
Joined:Mon Feb 23, 2015 9:05 am
-
Location:Washington
I am using 3/32 tungsten and 1/16th er70s2 filler for 120 wall dom 1 and 3/4 tubing. Fit up is tight. It seems to be too much filler. I was thinking about trying .045 instead any opinions? Thanks John.
Hollywood1
- Hollywood1
-
Ace
-
Posts:
-
Joined:Mon Feb 23, 2015 9:05 am
-
Location:Washington
I use 1/16" often, are you Welding .095" wall?
I weld stainless, stainless and more stainless...Food Industry, sanitary process piping, vessels, whatever is needed, I like to make stuff.
ASME IX, AWS 17.1, D1.1
Instagram #RNHFAB
ASME IX, AWS 17.1, D1.1
Instagram #RNHFAB
- dynasty200sd
-
Guide
-
Posts:
-
Joined:Sat Mar 08, 2014 10:39 pm
-
Location:Holley, FL
With 0.120" wall tubing being welded to 0.120" wall tubing, each leg of your fillets should be 0.120" for the strongest weld without over-welding.
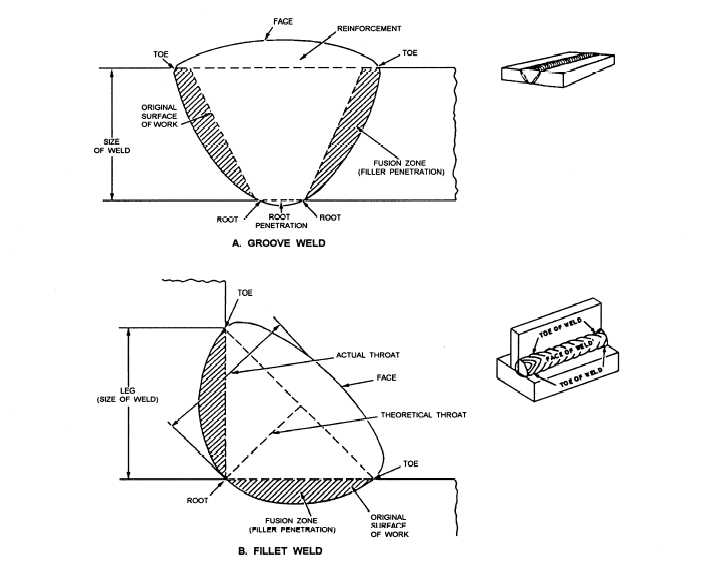
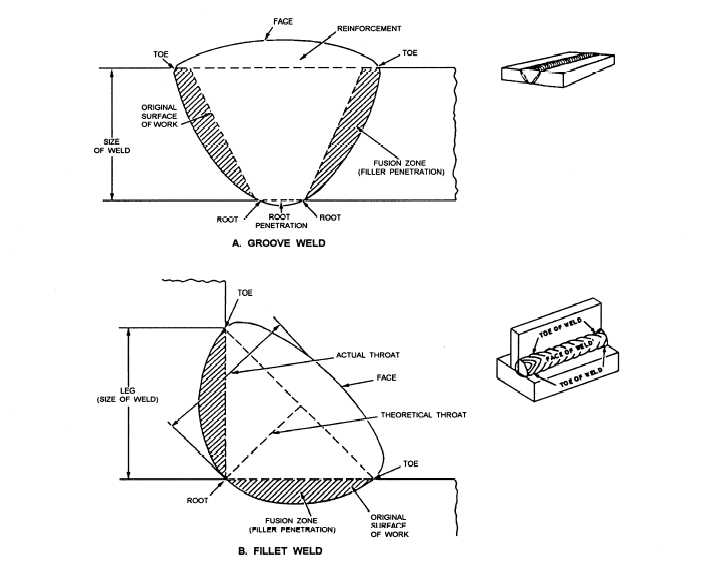
Hollywood1
- Hollywood1
-
Ace
-
Posts:
-
Joined:Mon Feb 23, 2015 9:05 am
-
Location:Washington
Welding .120 to a smaller wall horizontal seatbelt tube around .60 to.80 or so. Fit up is perfect. No gap.
AFR_Autoworks
- AFR_Autoworks
-
Workhorse
-
Posts:
-
Joined:Mon Nov 30, 2015 2:35 am
-
Location:Red Deer, Alberta, Canada
What amperage are you welding at? On my old welder I would weld .095 DOM at about 110amp with a trigger setup so it was all in. I also use 1/16 er70s-2. The biggest advice I can give (not knowing your current skill level) it make sure your tungsten is sharp. Any time I get even the slightest imperfection in the tungsten I re sharpen or change it. Also, ensure that your base material is puddled before you add filler. Everyone builds and welds roll cages differently but I love all my material to be surgically clean before I weld. I even go as far as polishing the inside of the coped tube. Do you have any pictures of the welds in question?
Hollywood1
- Hollywood1
-
Ace
-
Posts:
-
Joined:Mon Feb 23, 2015 9:05 am
-
Location:Washington
Here are a couple of pictures. I ended up using a little more amperage. Thanks for any opinions. john
- Attachments
-
- 20151201_113100.jpg (35.04 KiB) Viewed 4687 times
Hollywood1
- Hollywood1
-
Ace
-
Posts:
-
Joined:Mon Feb 23, 2015 9:05 am
-
Location:Washington
AFR_Autoworks
- AFR_Autoworks
-
Workhorse
-
Posts:
-
Joined:Mon Nov 30, 2015 2:35 am
-
Location:Red Deer, Alberta, Canada
That looks quite good! Glad you got it figured out. I used to use the 1 amp per .001" rule but found it was not hot enough. After I started welding hotter and slower my welds turned out allot better. I also found pulling the torch back to add filler helped too but that is just personal preference.
Hollywood1
- Hollywood1
-
Ace
-
Posts:
-
Joined:Mon Feb 23, 2015 9:05 am
-
Location:Washington
Thanks. I couldn't get the filler to melt right at first. Now with 130 amps works great. I appreciate the advice AFR.
Looks good, I agree more amps will help I find that is one of the largest mistakes, guys weld too cold.
Are you pulsing, or just moving the torch that far between dabs?
Are you pulsing, or just moving the torch that far between dabs?
I weld stainless, stainless and more stainless...Food Industry, sanitary process piping, vessels, whatever is needed, I like to make stuff.
ASME IX, AWS 17.1, D1.1
Instagram #RNHFAB
ASME IX, AWS 17.1, D1.1
Instagram #RNHFAB
Hollywood1
- Hollywood1
-
Ace
-
Posts:
-
Joined:Mon Feb 23, 2015 9:05 am
-
Location:Washington
- dynasty200sd
-
Guide
-
Posts:
-
Joined:Sat Mar 08, 2014 10:39 pm
-
Location:Holley, FL
From the AWS (American Welding Society), when welding fillets; each leg of the weld can equal the thinner wall of the tubes being welded together when welding two tubes of different wall thicknesses.Hollywood1 wrote:Welding .120 to a smaller wall horizontal seatbelt tube around .60 to.80 or so. Fit up is perfect. No gap.
Or, each leg can equal the wall thickness for that side of the weld (i.e., if leg A is against a tube with a wall of 0.125", and leg B is against a tube with a wall of 0.250"; you would weld leg A 0.125" away from the weld's throat, and leg B would be welded 0.250" away from the weld's throat).
AFR_Autoworks
- AFR_Autoworks
-
Workhorse
-
Posts:
-
Joined:Mon Nov 30, 2015 2:35 am
-
Location:Red Deer, Alberta, Canada
If you are using a manual pulse I know most guys run in the realm of 150 amps on .120 wall. So you may want to even experiment with more heat. I guess it would be related to how you pulse
I would recommend doing some etching and destructive testing to make sure you have enough penetration... Pulsing can be deceiving at times.Hollywood1 wrote:Thanks Rick. That is manual pulse. John.
I usually do not use pulse while doing cages or something structural.
I weld stainless, stainless and more stainless...Food Industry, sanitary process piping, vessels, whatever is needed, I like to make stuff.
ASME IX, AWS 17.1, D1.1
Instagram #RNHFAB
ASME IX, AWS 17.1, D1.1
Instagram #RNHFAB
Hollywood1
- Hollywood1
-
Ace
-
Posts:
-
Joined:Mon Feb 23, 2015 9:05 am
-
Location:Washington
Rick H. I have to thank you for your post. I just tried welding normally at 130 amps with no pulse and just got the best results yet. Iam confident now that there is plenty of penetration and the weld actually looks better. I cant tell you how many times ive heard people say do not pulse etc, and this whole time ive been manually pulsing and messing around with different pulse settings on the machine and my welding now looks better than any pulse settings. I guess its true. If you are a good enough welder u can weld just as well without the pulse or better in my opinion. thanks for all the tips. I have only been welding for almost a year now and with the help of this forum I am where I am at today with all of my welding thanks again. John
- Attachments
-
- 20150922_200726.jpg (35.55 KiB) Viewed 4016 times
-
- 20150907_193623.jpg (21.09 KiB) Viewed 4016 times
-
- 20150922_200726.jpg (35.55 KiB) Viewed 4016 times
Hollywood1
- Hollywood1
-
Ace
-
Posts:
-
Joined:Mon Feb 23, 2015 9:05 am
-
Location:Washington
Heres some stainless tubing to a header flange.
- Attachments
-
- DSCN0737 (2).JPG (58.21 KiB) Viewed 4015 times
- big gear head
-
Ace
-
Posts:
-
Joined:Thu May 07, 2015 11:46 am
-
Location:KY.
- MosquitoMoto
-
Weldmonger
-
Posts:
-
Joined:Sat Aug 01, 2015 8:38 am
-
Location:The Land Down Under
You're doing great work, Hollywood.
Hope I'm welding half as well as you are now when I have a year's experience under my belt.
Kym
Hope I'm welding half as well as you are now when I have a year's experience under my belt.
Kym
Hollywood1
- Hollywood1
-
Ace
-
Posts:
-
Joined:Mon Feb 23, 2015 9:05 am
-
Location:Washington
Thanks everyone for the kind words. Like I said, until now I discovered I can generally weld better without the pulse. Funny thing, I think I can just see the puddle better for starters. Other than running 120 - 150 Hz on a.c. and some cleaning action adjustments, I can say I will no longer be using pulse unless I have to bridge a big gap. I've tried all sorts of pyrex cups , standard cups, pulse, manual pulse, etc I weld with a #7 gas lens and that's what I use all the time period. All the videos and forum and people's great suggestions on the forum really helped. Thanks. Hey Kym looking forward to seeing some of your upcoming projects soon!
Hollywood1
- Hollywood1
-
Ace
-
Posts:
-
Joined:Mon Feb 23, 2015 9:05 am
-
Location:Washington
- big gear head
-
Ace
-
Posts:
-
Joined:Thu May 07, 2015 11:46 am
-
Location:KY.
Welded some bolt holes in a '65 Corvette intake manifold to repair some damaged threads. Welded a titanium fixture at work that had broke because the person who welded it before didn't use any filler wire. Welded some stainless steel wire racks. Nothing really interesting. I can't take pictures of anything that I do at work, which is where I do most of my welding. Most of the work in my shop lately has been building engines, transmissions and rear ends. I haven't had much weld work in my shop lately.
Your aluminum tanks are looking really good. You thought about building yourself a radiator?
Your aluminum tanks are looking really good. You thought about building yourself a radiator?
Freddie
Hollywood1
- Hollywood1
-
Ace
-
Posts:
-
Joined:Mon Feb 23, 2015 9:05 am
-
Location:Washington
That's pretty neat man. I just built my first nine inch ford. Took a while to get the pattern right. I commend you on that. Do you do any cage work and if so do u have any pointers or pictures Torvalds? Thanks John.
Hollywood1
- Hollywood1
-
Ace
-
Posts:
-
Joined:Mon Feb 23, 2015 9:05 am
-
Location:Washington
- big gear head
-
Ace
-
Posts:
-
Joined:Thu May 07, 2015 11:46 am
-
Location:KY.
I've done 6 cars. The last one I did was a '66 Nova that got a 4140 cage. I'll try to post some pictures of it later. The one thing that bothers me about a lot of chassis builders is that they want to use as little filler as possible. It scares me when I see some of the welds that they put on important pieces. I've asked why they do it and they tell me that they can cut 5 or 10 pounds out of the car if they don't use much filler. I've seen what happens to some of these welds when the car is damaged in a crash. One car had the bars broke off of the frame rails so clean that it could have been welded on again without any prep work. Just be sure that your welds are at least as thick as the thinnest tube that you are welding. Don't worry about saving weight in the welds, just be sure that the driver will survive a crash.
Freddie
Return to “Tig Welding - Tig Welding Aluminum - Tig Welding Techniques - Aluminum Tig Welding”
Jump to
- Introductions & How to Use the Forum
- ↳ Welcome!
- ↳ Member Introductions
- ↳ How to Use the Forum
- ↳ Moderator Applications
- Welding Discussion
- ↳ Metal Cutting
- ↳ Tig Welding - Tig Welding Aluminum - Tig Welding Techniques - Aluminum Tig Welding
- ↳ Mig and Flux Core - gas metal arc welding & flux cored arc welding
- ↳ Stick Welding/Arc Welding - Shielded Metal Arc Welding
- ↳ Welding Forum General Shop Talk
- ↳ Welding Certification - Stick/Arc Welding, Tig Welding, Mig Welding Certification tests - Welding Tests of all kinds
- ↳ Welding Projects - Welding project Ideas - Welding project plans
- ↳ Product Reviews
- ↳ Fuel Gas Heating
- Welding Tips & Tricks
- ↳ Video Discussion
- ↳ Wish List
- Announcements & Feedback
- ↳ Forum News
- ↳ Suggestions, Feedback and Support
- Welding Marketplace
- ↳ Welding Jobs - Industrial Welding Jobs - Pipe Welding Jobs - Tig Welding Jobs
- ↳ Classifieds - Buy, Sell, Trade Used Welding Equipment
- Welding Resources
- ↳ Tradeshows, Seminars and Events
- ↳ The Welding Library
- ↳ Education Opportunities