Advice on how to weld this
Posted: Wed Aug 19, 2015 4:04 am
These item are the crown wheel and hub from a BMW motorcycle.
The silver bit is the new hub and I cant tell if its stainless or a bright steel.
The crown wheel is whatever type of steel crown wheels get made out of.
Now I have NEVER heard or seen a crown wheel being welded to the hub before, this type is ensuring a complete rebuild and reshim when ever the wheel drive teeth on the hub wear out. Yes the Germans taught the Japanese everything they knew.
There is a shop in England that replaces the hubs, but dont do it if you live outside the UK.
They cant tell me what the material of the hub is made from and only that they use "normal" steel mig wire to replace the weld.
So over to the gurus.
My TIG skills are in serious need of a brush up, which I'll do before I go anywhere near this. I'm thinking TIG as the weld was only around a 1/8 " bead and I can possibly use a stainless filler to join these 2 bits together.
Old and new hubs
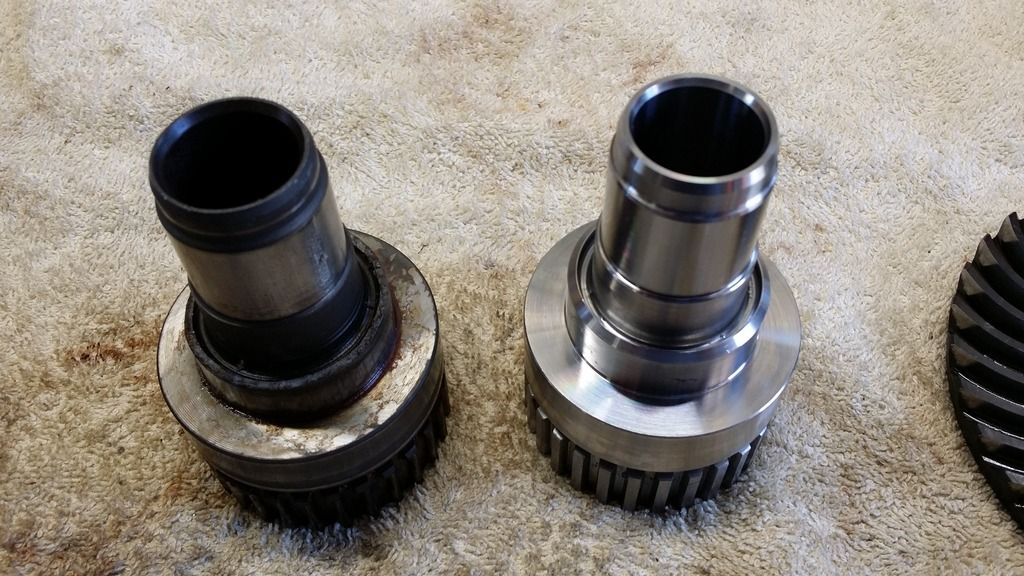
Crown wheel
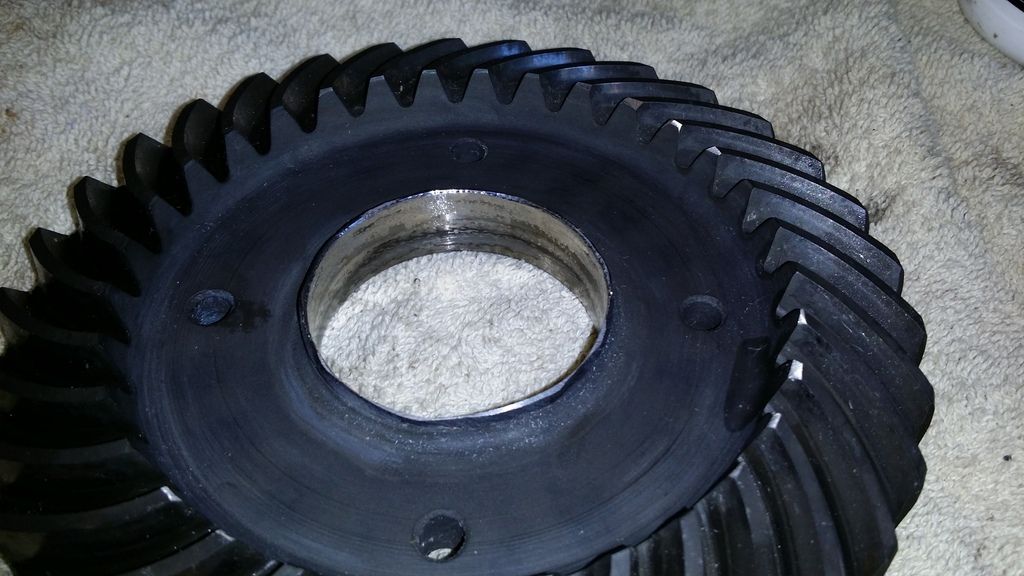
Pressed together

The bead is required around the shiny lip on the inside of the crown wheel, where the bevel on the hub meets it.
Sorry no arrows I a pc klutz.
Any advice you guys can give would be much appreciated.
The silver bit is the new hub and I cant tell if its stainless or a bright steel.
The crown wheel is whatever type of steel crown wheels get made out of.
Now I have NEVER heard or seen a crown wheel being welded to the hub before, this type is ensuring a complete rebuild and reshim when ever the wheel drive teeth on the hub wear out. Yes the Germans taught the Japanese everything they knew.
There is a shop in England that replaces the hubs, but dont do it if you live outside the UK.
They cant tell me what the material of the hub is made from and only that they use "normal" steel mig wire to replace the weld.
So over to the gurus.
My TIG skills are in serious need of a brush up, which I'll do before I go anywhere near this. I'm thinking TIG as the weld was only around a 1/8 " bead and I can possibly use a stainless filler to join these 2 bits together.
Old and new hubs
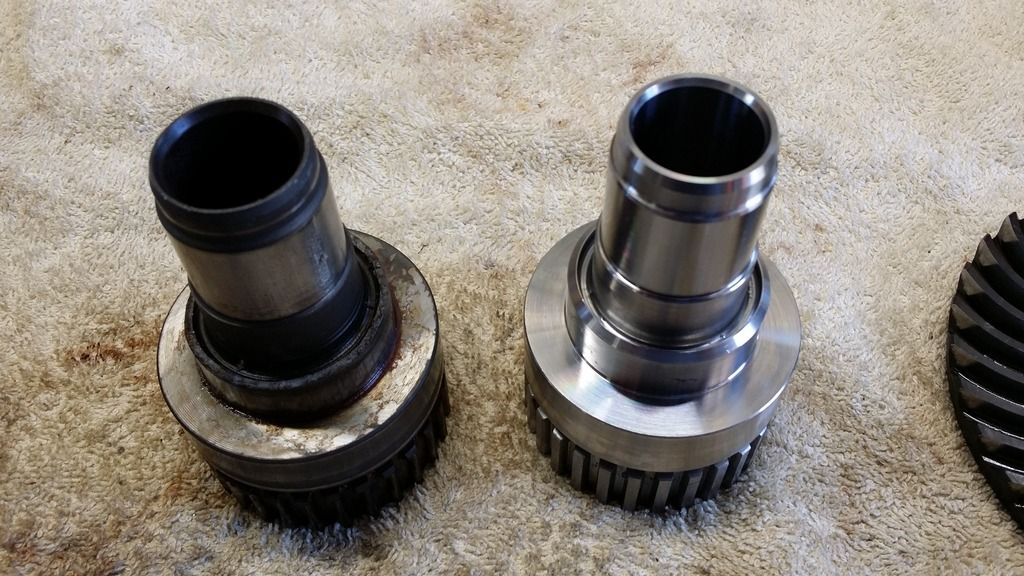
Crown wheel
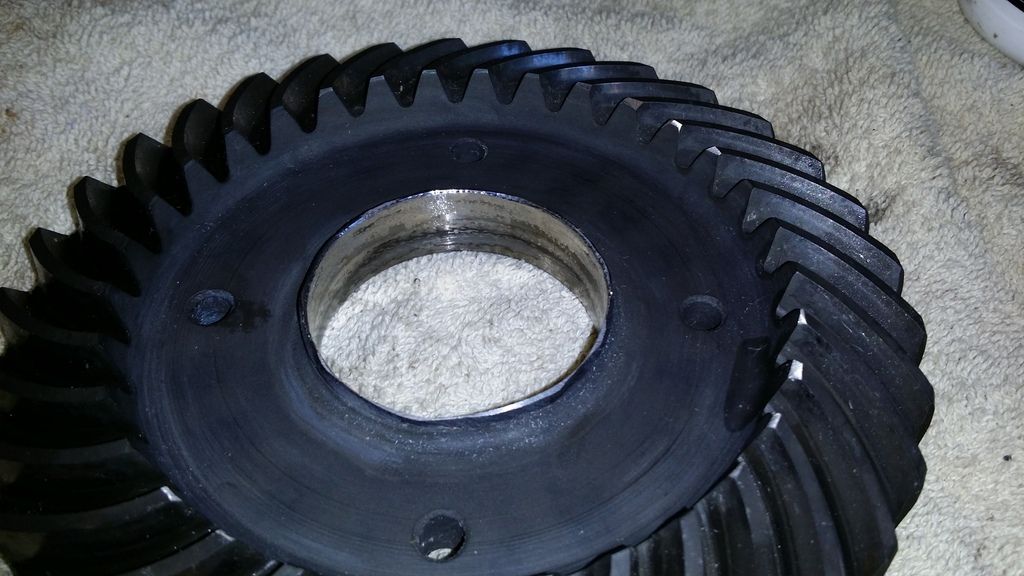
Pressed together

The bead is required around the shiny lip on the inside of the crown wheel, where the bevel on the hub meets it.
Sorry no arrows I a pc klutz.
Any advice you guys can give would be much appreciated.