Page 1 of 1
Tig welding thin steel
Posted: Wed Jul 15, 2015 2:29 am
by SonOfAnarchy ZA
Hi guys this is my first post, I've only just started to learn how to tig weld and think I have started on a difficult project for a beginner.
So I have a drift car and have recently pulled the motor and would like to neaten up the engine bay build new boost pipes and exhaust from stainless steel but I'm finding it very difficult to do the first job on my list. What I am try to do is fill all the unnecessary holes in the engine bay before I respray it. The metal I am welding is super thin around 0.7mm thick and I keep burning holes

and spend most of the time filling the bigger holes I have created

this is the setup I'm using:
Ark welder.
17v tig torch electrode negative.
#5 cup.
2.4mm tungsten 2% thoriated
1.6mm ER70S filler.
9l/m flow of argon.
And I've tried different amperage and struggling to come right I scratch start(20amp) and immediately it makes a hole

so I tried starting with filler right there that seemed to help a bit but once I've got a bit of filler the amperage seems to low to created a nice puddle any higher current and as soon as I move the puddle I burn away the thin steel

another thing that adds to the challenge is I'm working outside and the is wind from time to time. Any ideas?
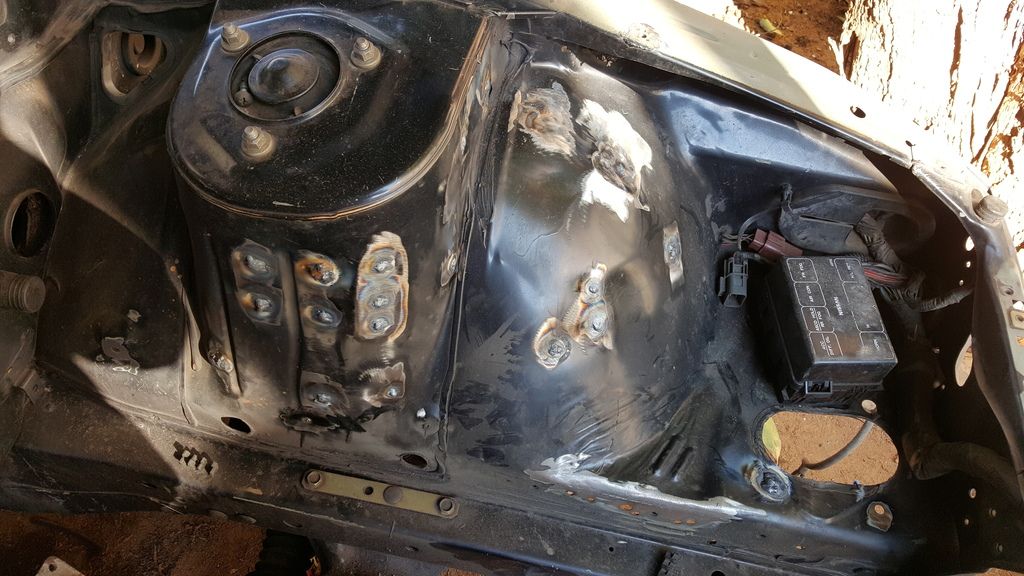
Re: Tig welding thin steel
Posted: Wed Jul 15, 2015 8:21 am
by big gear head
In my opinion you are using the wrong process. I've filled a lot of holes in sheet metal. I use a copper block on the back side and a MIG welder to fill in the hole. The copper block takes a lot of the heat away and supports the back side of the weld for a smooth finish. The MIG welder is quicker and puts less heat into the metal. Short tack welds joined together fills the holes quick without making the holes larger.
Re: Tig welding thin steel
Posted: Wed Jul 15, 2015 8:29 am
by SonOfAnarchy ZA
Problem is all i have is tig

need to make it work

Re: Tig welding thin steel
Posted: Wed Jul 15, 2015 9:49 am
by TRACKRANGER
Welcome to the forum
You may also be able to use a copper block backing plate method with TIG
However, if you are just starting out, practice on some scrap steel of similar thickness first. If you want to plug holes in very thin gauge with TIG, you'll definitely need something to draw the heat away. It will be more difficult with TIG. Sorry, just stating facts.
Trev
Re: Tig welding thin steel
Posted: Wed Jul 15, 2015 9:53 am
by big gear head
Use the copper block behind the hole. Hold the wire against the edge of the hole. Strike your arc on the end of the wire instead of the sheet metal. Melt the wire and then flow it into the metal.
Re: Tig welding thin steel
Posted: Wed Jul 15, 2015 9:55 am
by SonOfAnarchy ZA
thanks for the replies would aluminium backing work?
Re: Tig welding thin steel
Posted: Wed Jul 15, 2015 10:09 am
by Braehill
S-O-A ZA,
First off, welcome to the forum.
My first question is, is your welder a DC welder? You said electrode negative but if your welder is an AC only machine it makes no difference when it comes to scratch start tig, you need DC.
Is it an inverter welder? Some inverters have circuits that lend themselves well to stick welding but are not Tig friendly. They are made that way so when the rod sticks it opens a circuit or boosts the output if it picks up a voltage change.
If it is indeed a DC welder, try starting at about 30-40 amps on a similar sized piece of scrap. Remember it needs to be down to bright shiny metal and if there's paint on the under side it will make vapors that enter the shield gas envelope. When this happens you end up with bigger holes.
You have indeed picked a pretty hard starting point to learn to Tig weld, even with top shelf equipment.
Len
Re: Tig welding thin steel
Posted: Wed Jul 15, 2015 10:17 am
by SonOfAnarchy ZA
Braehill wrote:S-O-A ZA,
First off, welcome to the forum.
My first question is, is your welder a DC welder? You said electrode negative but if your welder is an AC only machine it makes no difference when it comes to scratch start tig, you need DC.
Is it an inverter welder? Some inverters have circuits that lend themselves well to stick welding but are not Tig friendly. They are made that way so when the rod sticks it opens a circuit or boosts the output if it picks up a voltage change.
If it is indeed a DC welder, try starting at about 30-40 amps on a similar sized piece of scrap. Remember it needs to be down to bright shiny metal and if there's paint on the under side it will make vapors that enter the shield gas envelope. When this happens you end up with bigger holes.
You have indeed picked a pretty hard starting point to learn to Tig weld, even with top shelf equipment.
Len
thanks len yes the welder is a dc inverter but was initially made for ark welding. I did grind the paint down but now that you mention it the other side of the steel is left untouched in some parts as it is difficult to get a grinder or sand paper there. ive got some 1.2 mm sheet metal at home think i must practice abit more
Re: Tig welding thin steel
Posted: Wed Jul 15, 2015 10:34 am
by Braehill
If you don't mind include a first name or a nickname for our responses to be more personal, we wouldn't think of reporting you as an anarchist.
If you can't get to the back side with a grinder, once you're able to keep an arc without melting the base metal, make a small circle around the hole with the torch to melt the paint. If you can get in there with a wire brush and remove the burnt paint, if you can't, let it smoke off before you actually try to weld it. A lot of body parts have rubberized undercoat which makes it even worse, try to scrape it off if it's present.
You can also use a backer piece if the back side is accessible that's cut a little larger than the hole. If you have a drill press, take a piece of scrap and get a hole saw an remove the center bit and cut discs. Trying this with a hand drill is pretty hard as it becomes unwieldy. You can spot weld a filler rod to the disc and pull it through the hole from the back side to hold it in place while you tack it, then just melt off the filler and start welding.
Len
Re: Tig welding thin steel
Posted: Wed Jul 15, 2015 10:39 am
by SonOfAnarchy ZA
Thanks for the tip Len i will give it a try
Jason

Re: Tig welding thin steel
Posted: Wed Jul 15, 2015 11:59 am
by big gear head
Aluminum backing should work. I have copper, so that's what I use.
Re: Tig welding thin steel
Posted: Fri Jul 17, 2015 11:31 pm
by GreinTime
If you walk into the driveway Braehill, you'll see that exact same strut tower on the drivers side of my car

Re: Tig welding thin steel
Posted: Sat Jul 18, 2015 12:43 am
by SonOfAnarchy ZA
GreinTime wrote:If you walk into the driveway Braehill, you'll see that exact same strut tower on the drivers side of my car

Aah a man of good taste:P
Re: Tig welding thin steel
Posted: Sat Jul 18, 2015 6:26 pm
by GreinTime
SonOfAnarchy ZA wrote:GreinTime wrote:If you walk into the driveway Braehill, you'll see that exact same strut tower on the drivers side of my car

Aah a man of good taste:P
I don't know about good taste, but I have one lol. I'm currently debating in whether to fix the rust on mine, or find a cleaner shell and start fresh. I have a complete S15 front end for it, I just don't know whether I want to invest the work in this particular chassis