Page 1 of 1
tig cup welding cup size
Posted: Wed Aug 18, 2010 12:18 am
by Paisano
I don't claim to be an expert,so here goes.When tigging lets say 1/4 inch regular steel,does it make better sense to run a smaller size cup for better concentration of gas.If you can educate me on this I'd appreciate it.What size cup is best suited for what,stainless,alluminum,reg/steel in regards to thickness,etc.
Don't seem to find to much on this subject.
thanks, Paisano
Re: tig cup welding cup size
Posted: Wed Jan 05, 2011 5:17 pm
by WELDER 13
hey paisano not no expert either but a little experience when i run my tig rig i swapped out my standard cup and gas difusser for a gas lens set up sounds like your having problems with gas flow this will help out greatly evenly distrbutes the gas but the other hand i use a wide cup for aluminum since it needs to be balled at end more clearance for gas such as a 8 -10 depending on how thick of material and like a 5 -7 for stainless and mild steel hope this helps i run my ccf a little high at about 20 -25 u can set it at 10 to 15 hope this helps like i said not no expert and if you walkinf the cup you want a smaller one for root and larger for cap just to roll easier personal preferance is what it boils down too in my opinion hope this helps

Re: tig cup welding cup size
Posted: Thu Jan 06, 2011 6:07 pm
by jakeru
Miller has an online "TIG welding calculator" that gives recommended parameters (including shielding cup size and flow rate) for various weld joint types, materials, and thicknesses:
http://www.millerwelds.com/resources/ca ... ulator.php
CK Worldwide has a chart with similar information as the Miller calcualtor here:
http://www.ckworldwide.com/tech-6.pdf
Also, CK Worldwide has a useful "GUIDE FOR SHIELD GAS FLOWS, CURRENT SETTINGS AND CUP SELECTION", for various electrode diameters and other parameters, halfway down on this page:
http://www.ckworldwide.com/tech-3.pdf
For example, the miller TIG calc recommends a 1/8" tungsten electrode diameter with 225-300 amps, and a 1/2" (= #8) cup with 13cfh argon gas flow for a butt welded 1/4" steel joint.
The CK chart recommends using a #7,#8, or #10 cup, with between 10-18cfh std collet body or 8-12cfh gas lens body, when welding ferrous materials with a 1/8" tungsten.
While references like these charts&calculators give a "ballpark" starting point, it is a good idea before attempting to weld any critical or important joints, to test the paramters (and experiemnt if necessary) on a test coupon of similar metal type and thickness, and weld joint type until the desired results are achieved.
Re: tig cup welding cup size
Posted: Thu Jan 06, 2011 7:10 pm
by WILD BILL
How do you know if you have proper gas coverage or not?
Re: tig cup welding cup size
Posted: Thu Jan 06, 2011 7:55 pm
by sschefer
WILD BILL wrote:How do you know if you have proper gas coverage or not?
There's a couple of really good indicators. With too little gas flow, you'll spit tungstens and your welds will be sooty. With too much gas flow your weld puddle will freeze prematurely and be frosty.
As a side note, sometimes we try to compensate for a bad torch angle with more gas flow. Sometimes it works but the sure indicator that your torch angle is wrong is a sooty comet streak at the end of the weld.
Re: tig cup welding cup size
Posted: Sun Jan 09, 2011 5:35 pm
by jakeru
Here is one suggestion made by Jody towards the bottom of this titanium welding page:
http://www.weldingtipsandtricks.com/wel ... anium.html
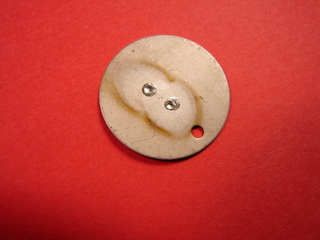
"[A titanium disc like the one shown here] is an excellent way to make sure your shielding gas coming out of the cup is good no matter what kind of metal you are welding. You just puddle a small area for a few seconds and then terminate the arc and hold the torch still. If you get any discoloration other than slight straw, you may not have good enough argon shielding to weld titanium or anything else. I recommend carrying one of these titanium weld test coins on your key chain."
But what I usually do, at least when welding aluminum, is be on the lookout for any "crud" floating in the middle of the puddle (which with perfect shielding and AC balance setting, would otherwise appear completely shiny and mirror-like). If the aluminum oxidation gets really bad, it can completely cover the puddle with a "skin" which will prevent good welds.
You can also be on the lookout for the "rainbow" discoloration patterns when welding steels that have relatively little oxides on their surfaces before being welded (such as clean cold rolled steel, or stainless steel.) They will form the rainbow oxidation film colors just like titanium does (perhaps not as readily as titanium does.)