Page 1 of 1
blowing out when welding tube
Posted: Sat Dec 06, 2014 8:08 pm
by jcw
I know it's been covered before, but I was wondering if you could just stop short of welding completely around a tube joint to prevent the puddle from being blown out. Instead of drilling a brand new hole somewhere else.
My project is frame bracing for an old 70's motorcycle. 7/8" and 1" 0.065" tube. Most welded up fine, but the shorter corner braces with the least amount of length seem to not want to close up. It's getting pretty ugly. LOL.
Re: blowing out when welding tube
Posted: Sat Dec 06, 2014 8:19 pm
by zank
This doesn't help you now, but on future projects drill vent holes into the tube that is being covered by your coped tube.
To address your question, I would prefer to drill a small vent hole in a less stressed area and close up the weld.
Re: blowing out when welding tube
Posted: Sat Dec 06, 2014 9:21 pm
by Superiorwelding
Besides drilling a vent hole as zank suggested I usually stop short and let the tube cool down. Usually but not always you can light up, dip and stop and the hole will fill. I did some alum the other day using this process and it worked very well.
-Jonathan
Re: blowing out when welding tube
Posted: Sat Dec 06, 2014 10:38 pm
by jcw
zank wrote:This doesn't help you now, but on future projects drill vent holes into the tube that is being covered by your coped tube.
To address your question, I would prefer to drill a small vent hole in a less stressed area and close up the weld.
drill the hole right in the center of the covered part? That's cool! why didn't I think of that.
superiorwelding wrote:Besides drilling a vent hole as zank suggested I usually stop short and let the tube cool down. Usually but not always you can light up, dip and stop and the hole will fill. I did some alum the other day using this process and it worked very well.
-Jonathan
I tried that and it worked on the longer tubes, but the short corner braces blew out even with a second or two. Maybe it's the wall thickness?
Here's some pics. Not pretty. I don't pretend that they are. Or, that I'm an accomplished welder. Maybe someday...
It looks like a zit that popped.
it's funny how all that practice you did on the bench goes out the window and you revert back to your old habits when you weld "for real." I felt I needed to make sure I made a good weld, and all that dime stacking went out the window.
here's the monstrosity (didn't pick up the table before this pic). I tried doing a lot of short segments and moved around the frame as much as I could to minimize heat distortion of the frame without a formal jig.
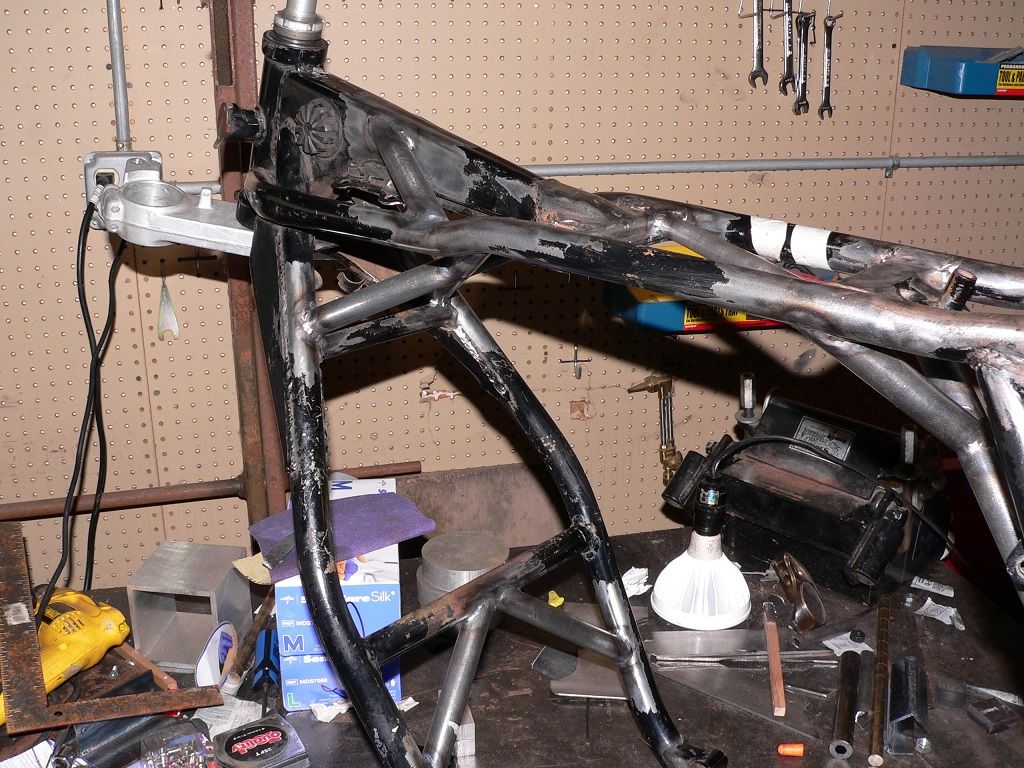
Why swab tube ID clean before welding?
Posted: Sun Dec 07, 2014 2:21 am
by dave powelson
X2 on comments to let tube cool down some before closing the joint.
Additionally, if the tube ID isn't wet and dry swabbed clean, then blown out
before any welding--that adds to the out gassing pressure and puddle blow-outs and porosity and crappy appearance and
that fiddingly around making things squeaky clean is only done by pros so they can justify higher charges.
On a tangent--that's probably been touched on in this forum-prior, concerning 'chrome-moly' tube frame
repair welding, you might some post weld normalizing (gentle torch heat to 7-900 F, slow cool) to mitigate HAZ stress fracturing. I do that automatically on aircraft c/m tube frame repairs, working under an IA's approval.
Re: blowing out when welding tube
Posted: Sun Dec 07, 2014 11:34 am
by jwright650
So to fix the blow out in the first pic...are you drilling back through that spot and then filling it back in with the Tig once everything has cooled off to see if the outgassing quits giving you trouble closing the hole?
Re: blowing out when welding tube
Posted: Sun Dec 07, 2014 1:29 pm
by dave powelson
jwright650 wrote:So to fix the blow out in the first pic...are you drilling back through that spot and then filling it back in with the Tig once everything has cooled off to see if the outgassing quits giving you trouble closing the hole?
Grind, bur all that porosity out and feather. Simply drilling isn't going to remove that stuff. Trying to wash over it is futile.
Drilling vents is done before welding. Drilling a vent after the screwup, maybe. If one's really watching the puddle (hint) and the heat (hint) they can quickly see if outgassing, contamination is messin' with the puddle and stop.
Getting blowouts is not normal in tube construction. Blowouts indicate lack of internal cleaning, with heated air outgassing
a secondary cause. That's 'Why?' some guys are anal about
swabbing tube ID's clean before welding. Any, tiny bit of oil inside a tube, will quickly run right to the puddle from inches away, especially if the joint is lower than the oil spot. Running a sanding cartridge roll up inside the tube ends to make things bright and shiny, after wet and dry swabbing to remove mill oxidation doesn't hurt either.
Re: blowing out when welding tube
Posted: Sun Dec 07, 2014 2:00 pm
by jwright650
dave powelson wrote:jwright650 wrote:So to fix the blow out in the first pic...are you drilling back through that spot and then filling it back in with the Tig once everything has cooled off to see if the outgassing quits giving you trouble closing the hole?
Grind, bur all that porosity out and feather. Simply drilling isn't going to remove that stuff. Trying to wash over it is futile.
Drilling vents is done before welding.
I was thinking that the porosity was generally concentrated to the place it bubbled out and showed itself and could be drilled out with a bit larger than the porosity cluster and would give you nothing but clean material to weld back up.
I've welded over porosity before...LOL, I know what happens(nothing good).

Re: blowing out when welding tube
Posted: Sun Dec 07, 2014 2:18 pm
by jcw
appreciate of the input.
the frame is mild steel. I've read pre heating the chrome-moly tube over a certain thickness is important, too.
All the tubing braces were both sanded and wiped down with toluene inside and out. The frame that I was welding to could not be prepped on the inside. Outside was prepped the same way.
I'll grind out that pimple as best I can and give it another go.
I've read that tube joint strength is related to length of the overall weld. So, is it not acceptable to leave a 1/2 centimeter gap? I know zank said he wouldn't. Is that gap going to be a stress riser or a point of fatigue? Or is the weld strength just a little bit less if I fail to close the weld. (stupid question, but some of those narrow angle joints are nearly impossible to get to).
Re: blowing out when welding tube
Posted: Sun Dec 07, 2014 3:41 pm
by dave powelson
jcw wrote:appreciate of the input.
the frame is mild steel.
I've read pre heating the chrome-moly tube over a certain thickness is important, too.
***preheat on much thicker sections, not on tube assemblies
All the tubing braces were both sanded and wiped down with toluene inside and out. The frame that I was welding to could not be prepped on the inside. Outside was prepped the same way.
I'll grind out that pimple as best I can and give it another go.
I've read that tube joint strength is related to length of the overall weld.
So, is it not acceptable to leave a 1/2 centimeter gap? I know zank said he wouldn't.
*****1/2 cm rounds off to .200 inch, that's a huge gap. If there really was gapping that large, then weld porosity simply from having the large puddle back side exposed to air can be expected, in an enclosed tube joint. The tighter the tube joints, the stronger the assembly is and more resistant to fatigue.
Is that gap going to be a stress riser or a point of fatigue? Or is the weld strength just a little bit less if I fail to close the weld. (stupid question, but some of those narrow angle joints are nearly impossible to get to)
*****the 'normal' failure mode is at the HAZ area, just past the weld fillet toe. .
The normalizing I previously mentioned (which has been summarily ignored or blown-off...and is understandable) helps to allow stress to be distributed over a much larger area of the tube, rather than concentrated at this higher to lower strength transition of the HAZ (which is characteristic of thin walled, cm tubing--the weld heat has hardened this area, because it's cm.) Looking at crashed cm structures is great education.
"some of those narrow angle joints are nearly impossible to get to"........gas lens (allowing more tungsten stickout), flex loc torch with button cap gets in there.
Re: blowing out when welding tube
Posted: Sun Dec 07, 2014 4:47 pm
by jcw
I'm sorry I wasn't clear. The gap I meant was not welding completely around the tube.
Re: blowing out when welding tube
Posted: Sun Dec 07, 2014 5:13 pm
by dirtmidget33
dave powelson wrote:
Getting blowouts is not normal in tube construction. Blowouts indicate lack of internal cleaning, with heated air outgassing.
Any time you try to weld on any totally enclosed space you are subject to blowouts. The smaller the space the worst it is. It is the gases (air) expanding when heated. It is totally common to have blowouts when welding tubes if you do not allow somewhere for gases to expand to hence a vent. All race car chassis that are made correctly drill a hole in the middle of a tubing junction so gases can move freely threw the chassis. Quite a few even back purge and again these holes allow a way to distribute gases. Zank has already mentioned this and is totally correct. unfortunately the OP made a mistake and now he knows better for future reference. As for normalizing 4130 I would avoid that at all cost. I was informed a few drag race manufacturers where doing this and had chassis failures. In the circle track world of Sprints, midgets, champ cars(silver crown cars), nascar (now that they or using it), minisprints there is not one chassis builder that I know that does this. You start taking a touch willy nilly to joints you start changing the crystalline structure of the steel. These chassis hold up very well in a lot of violent wrecks and the use of 4130 being TIG welded has been done for years now on these cars and still is done by drilling vents and NOT heating tubes with torch.
Re: blowing out when welding tube
Posted: Mon Dec 08, 2014 10:53 am
by kiwi2wheels
dirtmidget33 wrote:
Any ti..........................As for normalizing 4130 I would avoid that at all cost. I was informed a few drag race manufacturers where doing this and had chassis failures. In the circle track world of Sprints, midgets, champ cars(silver crown cars), nascar (now that they or using it), minisprints there is not one chassis builder that I know that does this. You start taking a touch willy nilly to joints you start changing the crystalline structure of the steel. These chassis hold up very well in a lot of violent wrecks and the use of 4130 being TIG welded has been done for years now on these cars and still is done by drilling vents and NOT heating tubes with torch.
This may start a discussion that could have it's own thread ; anyway, this seems to be a subject of yeas/naes. As you say many chassis builders do not believe in stress relief, and I've seen some books that also advise against it. 4130 was originally designed for gas welding, many of us oldies go with the torch stress relief, as does the FAA , pg 23;
https://www.faa.gov/regulations_policie ... a_Ch05.pdf
Remember, you are taking the shrinkage stress out of the part also, and if is, say an A arm or sub frame, it will comply a lot closer dimensionally to the jig. It's critical that the oxy-acetylene plant holds a neutral flame, many don't these days, it's just seen as a source of heat.
Re drag chassis failures, an interesting read.
http://www.bmeltd.com/Dragster/tubulartales.htm
Re: blowing out when welding tube
Posted: Mon Dec 08, 2014 12:19 pm
by dirtmidget33
I skimmed threw your article will read more accurately later today. In the article you posted it states that they where not using the standard N tubing (normalized tubing) but the heat treated stuff. So according to this article it was choice of tubing both types are available to which once again all open whee chassis builders I know use the 4130 N tubing with ER70-S2 for better elongation . Which I would say, the drag guys choice in tubing is a case of someone looking at specs of tubing seeing one rated as a little higher tensile strength and decided to use that and go a little thinner on wall thickness to save weight. That are depending on rules (wall thickness specs) just thought it might make chassis stronger not taking into account the flex of the chassis and effects on tubing. I have talked to a few Chassis builders just recently and they all use the ER70-S2 even over the Lincoln recommended ER80 because of the elongation and due to dilution of materials. The ER80 makes it a more brittle weld.
Then we have the import of Chinese 4130 which is up for debate over the German and American stuff too.
Re: blowing out when welding tube
Posted: Mon Dec 08, 2014 1:10 pm
by Superiorwelding
I have been in a few heated, and I mean heated, debates on the welding of 4130/4140. I would like to add to this but it would be better to start a new thread as this discussion will get buried and never seen again. Please re-post your links there.
-Jonathan
Re: blowing out when welding tube
Posted: Mon Dec 08, 2014 10:33 pm
by dirtmidget33
Superiorwelding wrote:I have been in a few heated, and I mean heated, debates on the welding of 4130/4140. I would like to add to this but it would be better to start a new thread as this discussion will get buried and never seen again. Please re-post your links there.
-Jonathan
Sounds good to me Jonathan but where do we post links to?? I assume you where gonna start new thread
Re: blowing out when welding tube
Posted: Mon Dec 08, 2014 10:40 pm
by Superiorwelding
dirtmidget33 wrote:Superiorwelding wrote:I have been in a few heated, and I mean heated, debates on the welding of 4130/4140. I would like to add to this but it would be better to start a new thread as this discussion will get buried and never seen again. Please re-post your links there.
-Jonathan
Sounds good to me Jonathan but where do we post links to?? I assume you where gonna start new thread
I will Start one if you would like.....give me a few to dig up some documents.
-Jonathan