4130 Weld Problems
Posted: Tue Mar 26, 2013 12:56 pm
I have had an issue suddenly pop up as I finish up the main certified cage portion of my chassis (drag racing SFI 25.2). This is all 4130 tubing, varying from 1" x 0.058" to 1.625" x 0.083" (and the problem joints are mostly where those two are joined together). I haven't knowingly changed anything with how I prep my tubes, but suddenly I am running into intermittent splattering weld puddles, like I either have no shielding gas or have contamination at the weld puddle (seems more like contamination splatter). It seems to be intermittent, but usually at the start of a particular weld. If the weld starts clean then it usually stays clean the whole way. If it starts splattering, I can usually stop welding, clean up that spot with a wire brush, re-start the weld at a different point and weld right over that area without any more splatter. Sometimes the splattering is very brief and I can just "weld through" and get a clean bead, while other times I tried that it just got worse and blew through the tube.
When the splattering starts, it seems to be instantly as I start the arc, even though the arc is starting more on the "parent" tube at the junction (i.e., not directly on the cut tube end until I get the puddle started).
As far as metal prep, I normally use a hole saw notcher with wax cutting lubricant, then clean all the wax and other stuff off with carb cleaner and a rag. Then I use a grinder to "blunt" the sharp edges of the notch, then a sanding disc to clean the outside of the tubes at the joint (cleaning all mill scale off, down to "raw" metal), and also do the same to the inside of the cut tube ends using a sanding cartridge roll on a die grinder. Finally I go over the whole thing again with carb cleaner and a clean rag. I have been using this same process for this whole chassis without any issues until the end of the main cage, where I am finishing up some prior welds and adding several little 1" diameter cage gussets.
Trying to solve this issue I tried switching to cutting oil on the notcher, tried a different brand of carb cleaner, and tried acetone-based nail polish remover. I also tried using a wire wheel instead of the sanding disc, and fresh tungstens that were sharpened with a new grinding wheel. I also tried swapping Argon bottles. To confuse matters I had a split in my torch gas hose, but I have that taped up and holding for now (and a new one on the way). When I had the split it made things obviously worse, but back now to the intermittent problems. I am using a CK Gas Saver gas lens, and have tried flow rates from 12 to 25 CFM.
Here is a photo of one of the welds that had minor splattering, where I was able to clean it up and move to a different start spot then weld right over the initial "splatter spot" with no issues:
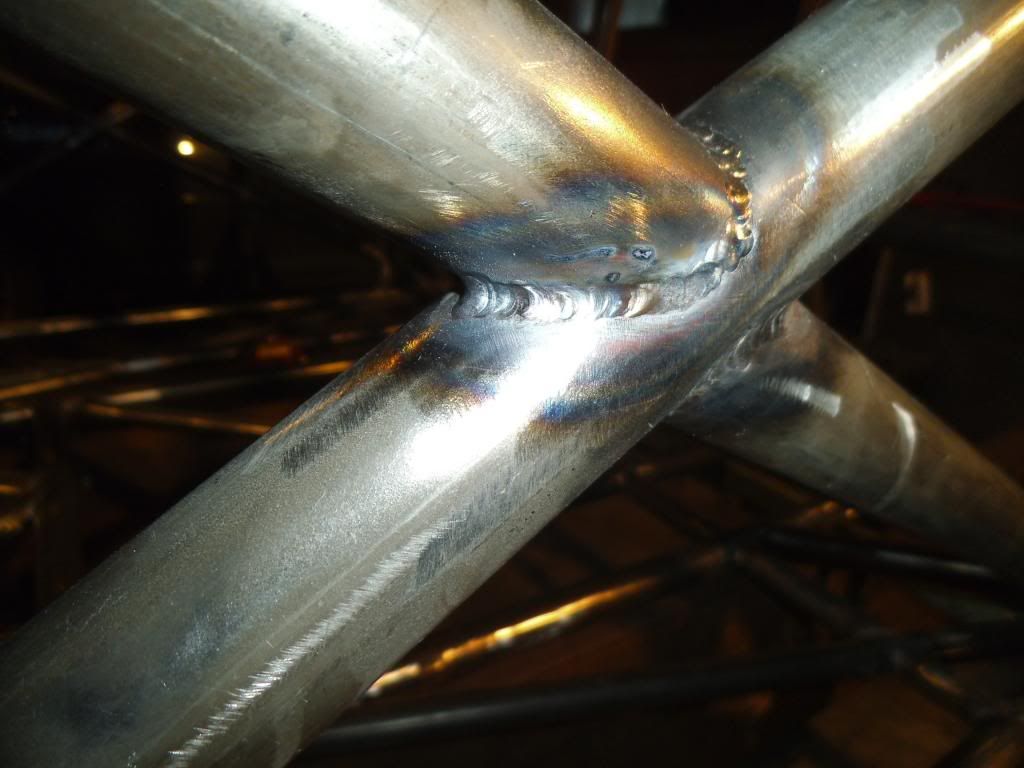
Here are a couple of photos of a section where I tried moving to new start spots, but the splatter seemed to happen at each spot, but cleaned up after a little more welding, but left a noticeable brown-rust colored residue around the weld:
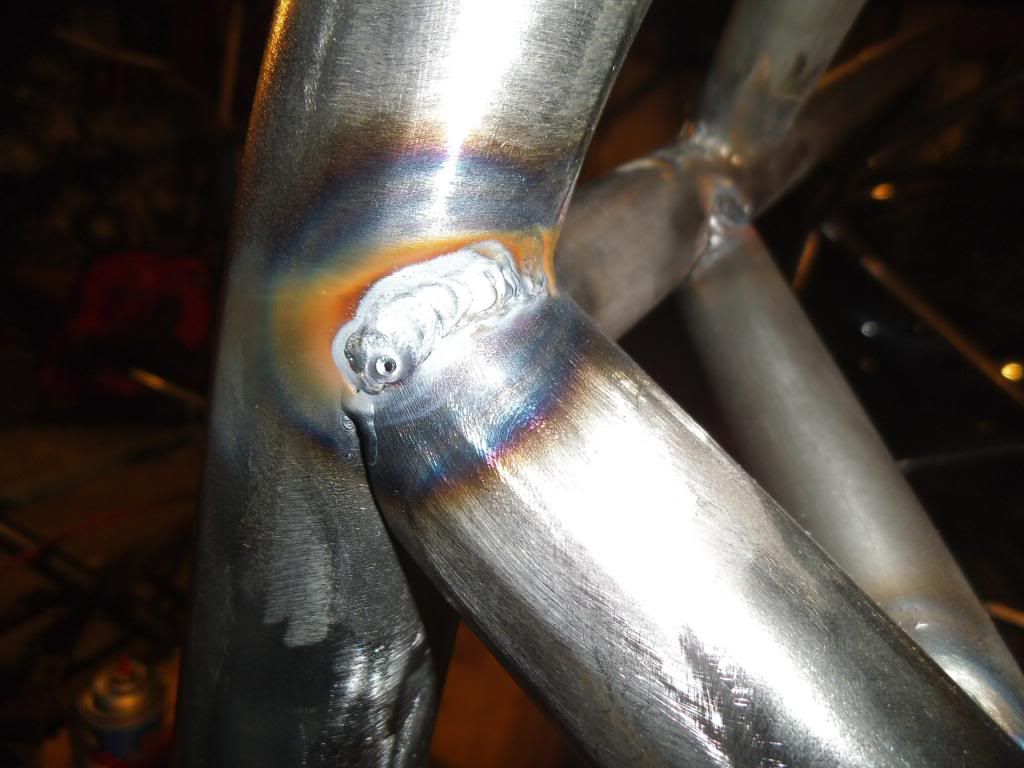
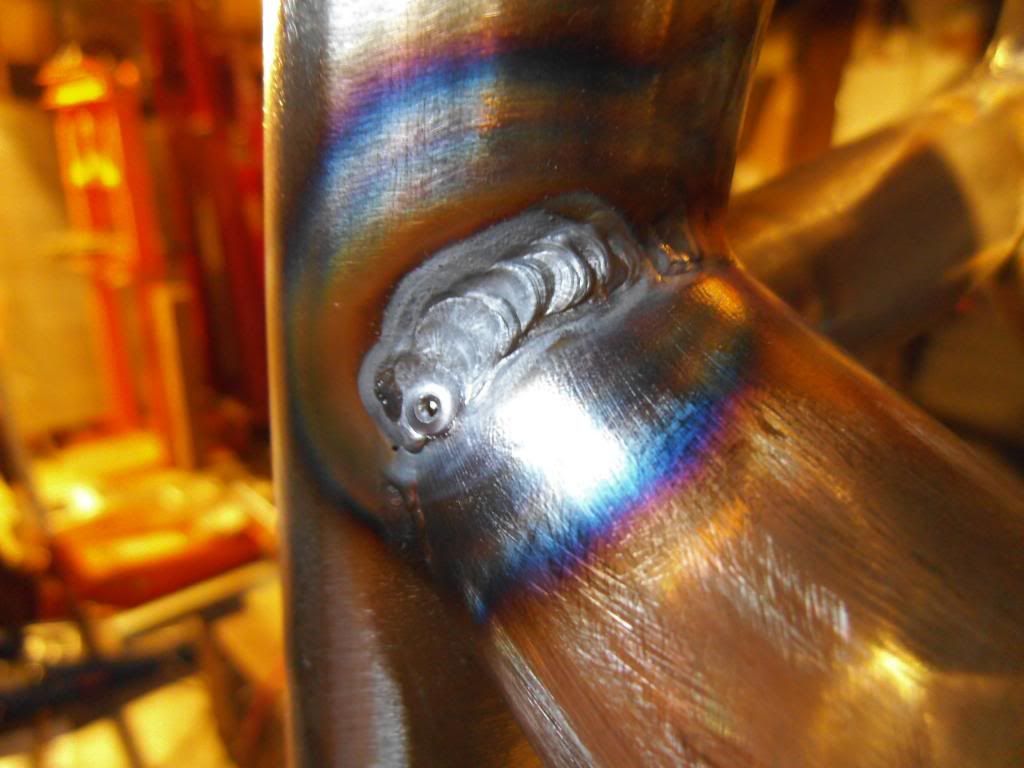
Any suggestions of what else to try? I started to think that it was the new 1" tubing, but it also happened on the continuation of an older joint that seemed to be fine when I welded the first portion a few weeks ago.
When the splattering starts, it seems to be instantly as I start the arc, even though the arc is starting more on the "parent" tube at the junction (i.e., not directly on the cut tube end until I get the puddle started).
As far as metal prep, I normally use a hole saw notcher with wax cutting lubricant, then clean all the wax and other stuff off with carb cleaner and a rag. Then I use a grinder to "blunt" the sharp edges of the notch, then a sanding disc to clean the outside of the tubes at the joint (cleaning all mill scale off, down to "raw" metal), and also do the same to the inside of the cut tube ends using a sanding cartridge roll on a die grinder. Finally I go over the whole thing again with carb cleaner and a clean rag. I have been using this same process for this whole chassis without any issues until the end of the main cage, where I am finishing up some prior welds and adding several little 1" diameter cage gussets.
Trying to solve this issue I tried switching to cutting oil on the notcher, tried a different brand of carb cleaner, and tried acetone-based nail polish remover. I also tried using a wire wheel instead of the sanding disc, and fresh tungstens that were sharpened with a new grinding wheel. I also tried swapping Argon bottles. To confuse matters I had a split in my torch gas hose, but I have that taped up and holding for now (and a new one on the way). When I had the split it made things obviously worse, but back now to the intermittent problems. I am using a CK Gas Saver gas lens, and have tried flow rates from 12 to 25 CFM.
Here is a photo of one of the welds that had minor splattering, where I was able to clean it up and move to a different start spot then weld right over the initial "splatter spot" with no issues:
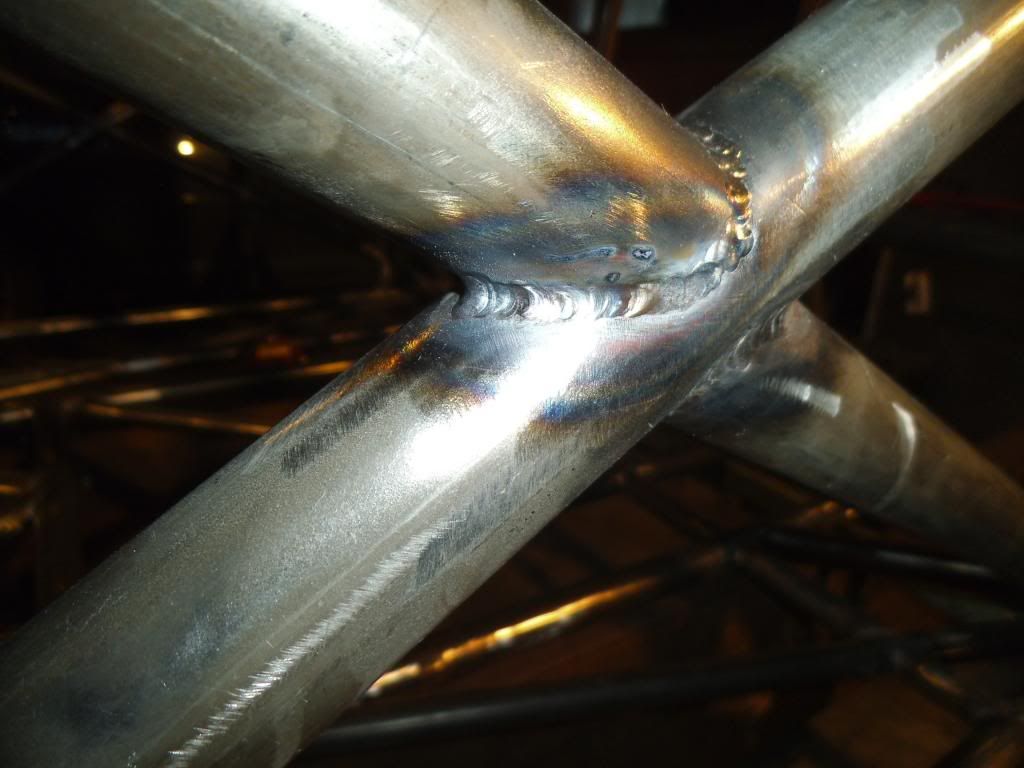
Here are a couple of photos of a section where I tried moving to new start spots, but the splatter seemed to happen at each spot, but cleaned up after a little more welding, but left a noticeable brown-rust colored residue around the weld:
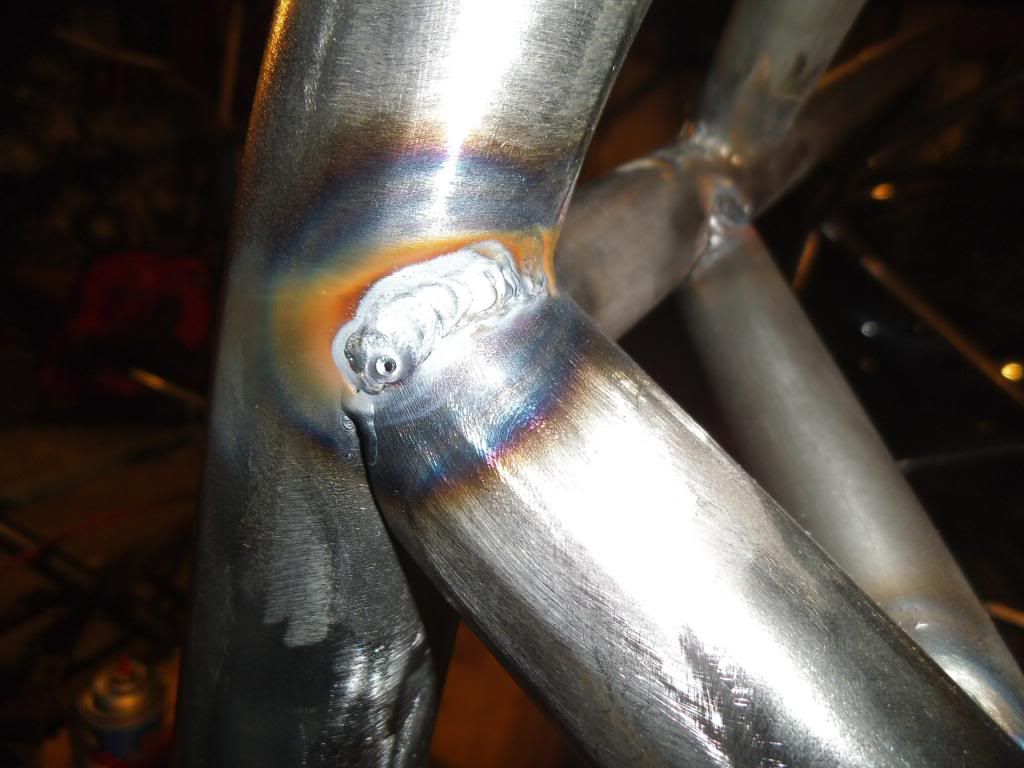
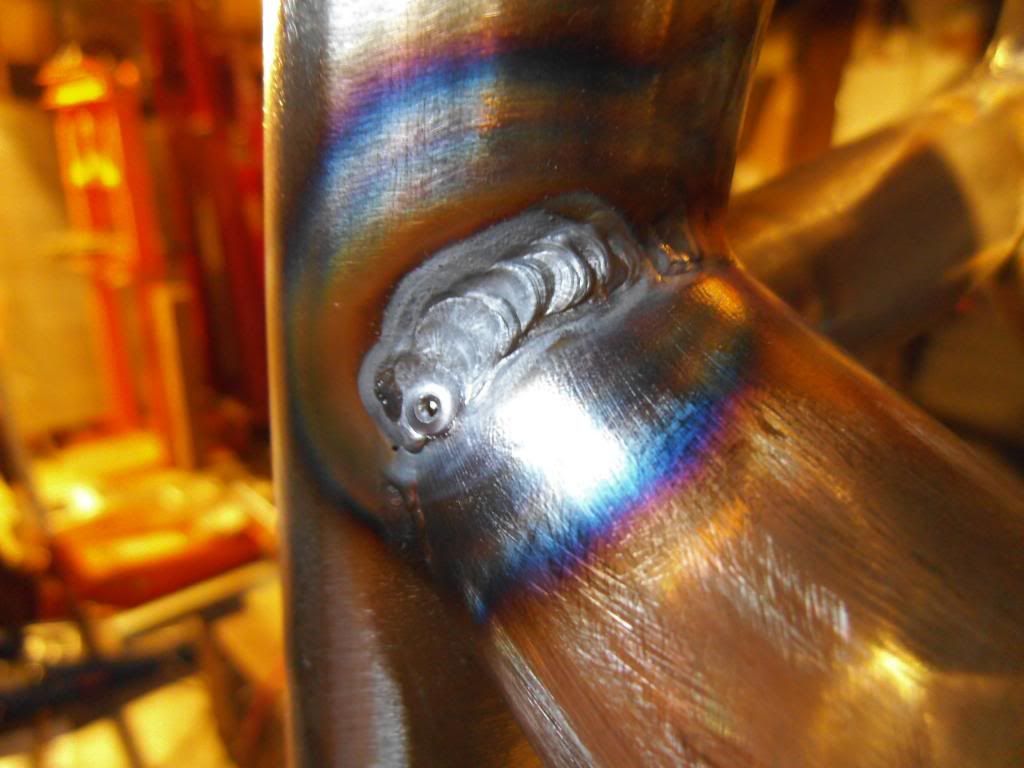
Any suggestions of what else to try? I started to think that it was the new 1" tubing, but it also happened on the continuation of an older joint that seemed to be fine when I welded the first portion a few weeks ago.