Strong backing
Posted: Fri Mar 15, 2013 10:23 pm
your work. Do any of you aluminum fab'rs do this? Aluminum moves a lot. Many of us don't get to use much in the way of jigs or fixtures, especially once projects start going towards 3D. I used to notice a lot of other fabrications with that bamboo effect between joints etc and it used to irk me. Then when you're done, tweaking something that is all caged in a 1/4 or 1/2 inch requires some substantial leverage. This is what I do. It helps keep things straight and factory looking. Many people who don't weld aluminum a lot tend to treat it like steel, meaning, they will assemble and tack all of the parts together and then weld it out all at once. For those who don't know, this little trick can save you a lot of work and make your stuff just look neater overall.
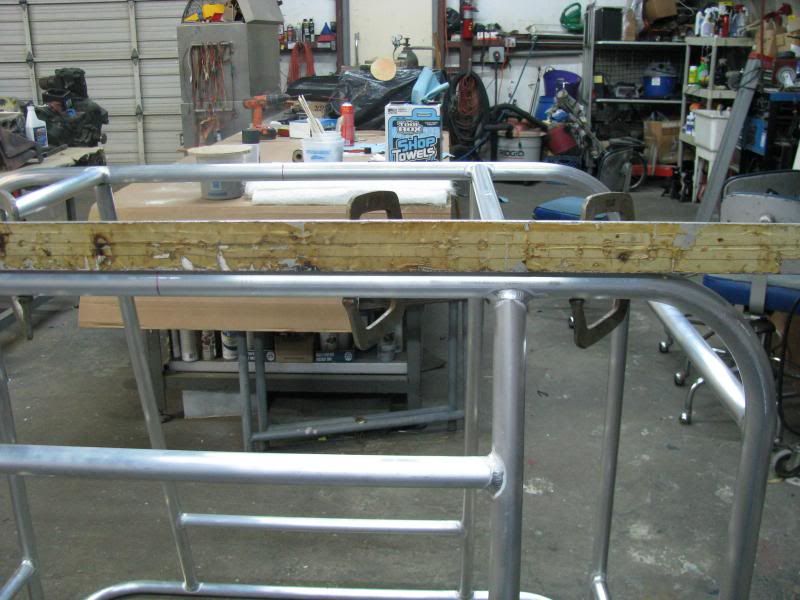
R6 and R11 framing clamps have to be one of the best inventions of modern times. I save all my oddball drops of angle and such for things like this. The above picture is a piece of 2" x 2" x 1/4" aluminum angle. You can tell by the masking tape (for use with anodized) on it's showing face that it has been used a lot. On heavier material, I will double these up and even employ shims to add pre-stress to help combat warpage. At most a good bump with a rubber mallet will fine tune any remaining distortion between welds.
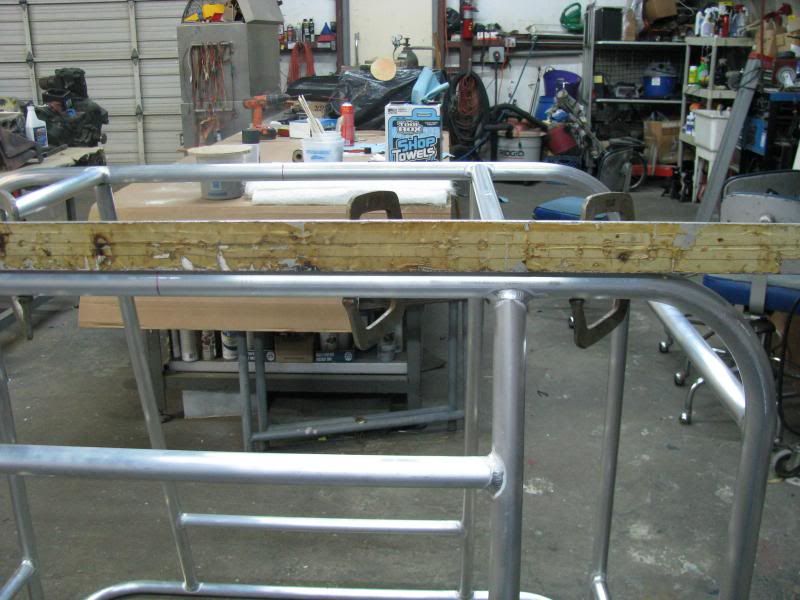
R6 and R11 framing clamps have to be one of the best inventions of modern times. I save all my oddball drops of angle and such for things like this. The above picture is a piece of 2" x 2" x 1/4" aluminum angle. You can tell by the masking tape (for use with anodized) on it's showing face that it has been used a lot. On heavier material, I will double these up and even employ shims to add pre-stress to help combat warpage. At most a good bump with a rubber mallet will fine tune any remaining distortion between welds.