Tips for 2mm thick intercooler pipe and Turbo Elbows?
Posted: Thu Oct 13, 2011 8:24 am
Hi everyone,
I'm a big fan of Jody's work and the community here. Learning how to make a consistent "stack of dimes" bead on 2mm thick intercooler piping has been challenging. Here is my best so far:
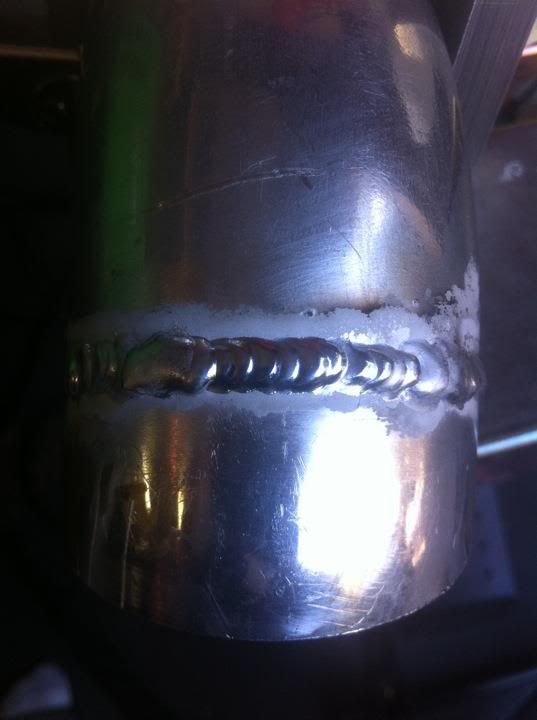
Machine: PowerTig 225LX
Amperage: 90 amps with pedal (no pulse, ~ 1'o'clock frequency, ~ 37% Balance)
Torch: air cooled hand-held with switch, control in 4T position
Gas: 100% pure argon
cup: everlast #7 cup
Flow: 7L / min
Tungsten: 3/32 2% lanthanated (sharpened to point)
Filler Rod: 3/32 4043
PreFlow: ~1-2s
PostFlow: ~8 seconds
Pulse: Off
Are there any tips or tricks you experienced tig welders can recommend to help me achieve a more consistent stack of dimes look (on pipe) like below? Also, since I have to weld on an aluminum 2.5 inch (diameter) elbow to my turbo like the picture, what settings do you guys recommend?:
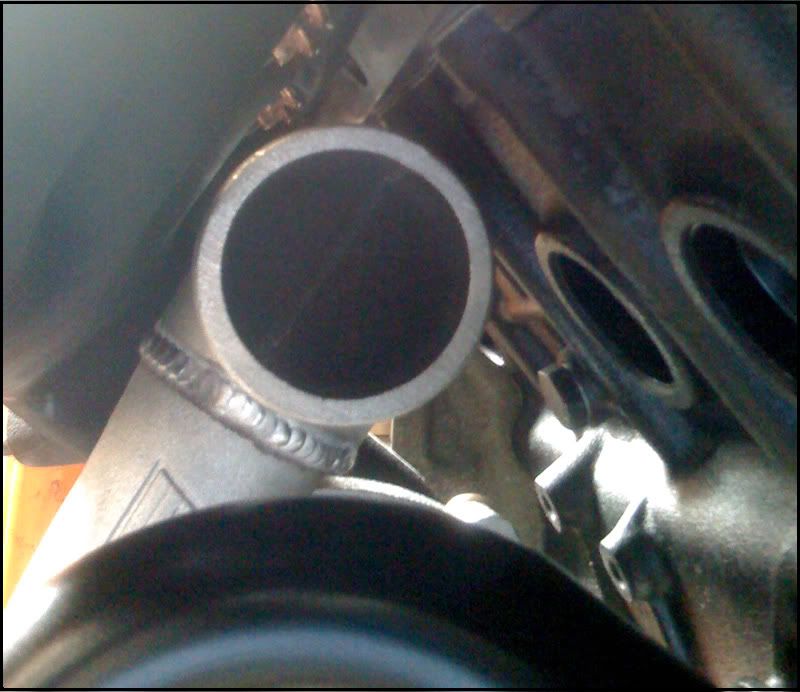
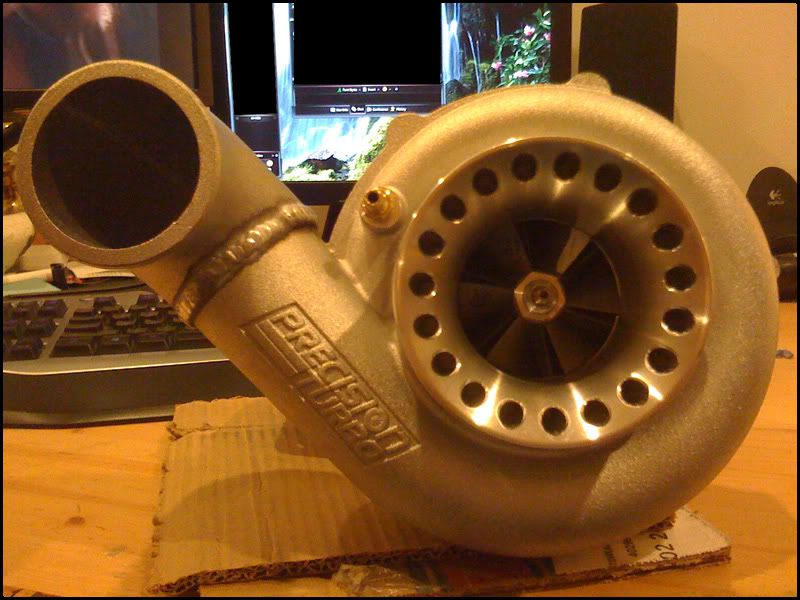
I'm a big fan of Jody's work and the community here. Learning how to make a consistent "stack of dimes" bead on 2mm thick intercooler piping has been challenging. Here is my best so far:
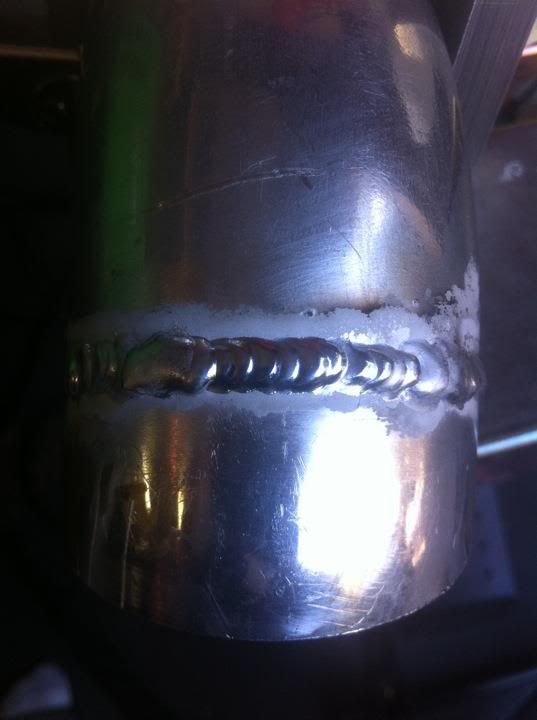
Machine: PowerTig 225LX
Amperage: 90 amps with pedal (no pulse, ~ 1'o'clock frequency, ~ 37% Balance)
Torch: air cooled hand-held with switch, control in 4T position
Gas: 100% pure argon
cup: everlast #7 cup
Flow: 7L / min
Tungsten: 3/32 2% lanthanated (sharpened to point)
Filler Rod: 3/32 4043
PreFlow: ~1-2s
PostFlow: ~8 seconds
Pulse: Off
Are there any tips or tricks you experienced tig welders can recommend to help me achieve a more consistent stack of dimes look (on pipe) like below? Also, since I have to weld on an aluminum 2.5 inch (diameter) elbow to my turbo like the picture, what settings do you guys recommend?:
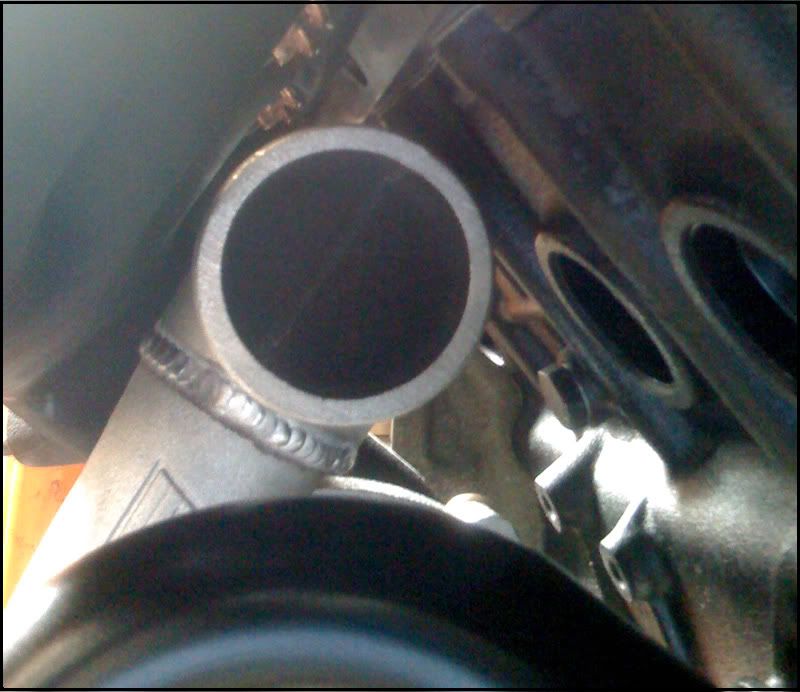
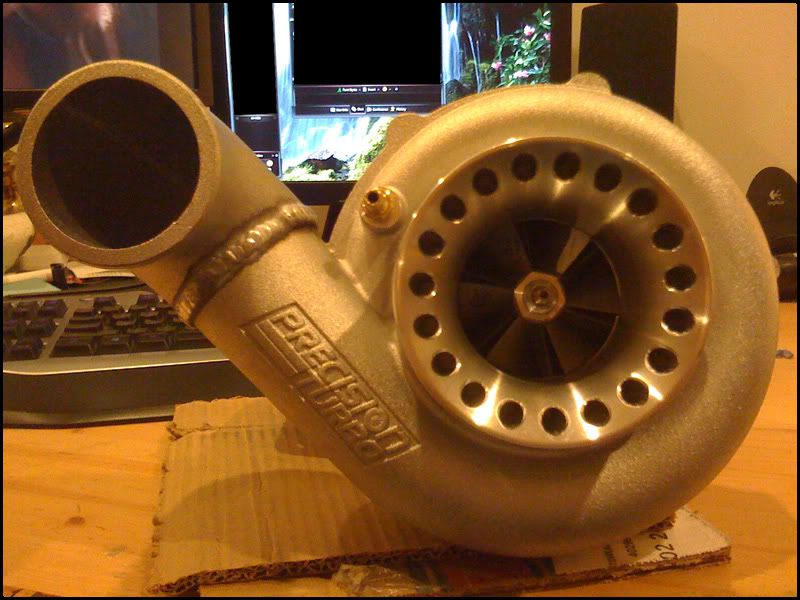