I don't think I would have a chance on the .005 blades. I was having a tough time with .035 on the utility knife blades. I think my pulse will go that low. I believe I can go as low as 3 amps with .040 tungsten. I was thinking along the lines of setting the max to 20-25 amps then 1pps with 20% peak 50% background current and add filler at the peak. at least to use the .035 wire.
I had a spool of .025 at one point and I'm still trying to find that, or I'll have to find some "not made to be filler" material that is thinner.
Tig welding tips, questions, equipment, applications, instructions, techniques, tig welding machines, troubleshooting tig welding process
- maker of things
-
Guide
-
Posts:
-
Joined:Tue Jul 19, 2016 6:52 am
-Jon
I learned how to weld at night, but not last night. (despite how my weld looks)
Lincoln Viking 3350 K3034-2&3
Dynasty 210DX w/cps and coolmate3
Lincoln Power Mig 180c
hermit.shed on instagram
I learned how to weld at night, but not last night. (despite how my weld looks)
Lincoln Viking 3350 K3034-2&3
Dynasty 210DX w/cps and coolmate3
Lincoln Power Mig 180c
hermit.shed on instagram
dirtmidget33
- dirtmidget33
-
Heavy Hitter
-
Posts:
-
Joined:Tue May 13, 2014 5:22 pm
Had some .40 tungsten in torch this morning it wasn't in greatest shape, thought what hell since I posted on this thread couple of days ago. Threw some used blades on bench and put them together been a long time since I tried this. Machine goes to 5 amps but won't puddle at that turned it up to 10 was a little much, but feathered down. So was prolly welded at 7 to 9, Filler was safety wire. Stuck the tungsten where it's discolored and yanked torch loose which made color even worse losing gas coverage. Might try another one later, I know I can get better results.
- 0824161039a.jpg (21.75 KiB) Viewed 1205 times
why use standard nozzles after gas lens where invented. Kinda of like starting fires by rubbing sticks together.
exnailpounder
- exnailpounder
-
Weldmonger
-
Posts:
-
Joined:Thu Dec 25, 2014 9:25 am
-
Location:near Chicago
Thats awesome. My machine will only go down to 10 amps with a 3/32" tungsten so I had to move out...no time for filler...Great work! I'm impressed! I think this game just took on a new life 

Ifyoucantellmewhatthissaysiwillbuyyouabeer.
- maker of things
-
Guide
-
Posts:
-
Joined:Tue Jul 19, 2016 6:52 am
What is the dia and matl of the safety wire?
-Jon
I learned how to weld at night, but not last night. (despite how my weld looks)
Lincoln Viking 3350 K3034-2&3
Dynasty 210DX w/cps and coolmate3
Lincoln Power Mig 180c
hermit.shed on instagram
I learned how to weld at night, but not last night. (despite how my weld looks)
Lincoln Viking 3350 K3034-2&3
Dynasty 210DX w/cps and coolmate3
Lincoln Power Mig 180c
hermit.shed on instagram
dirtmidget33
- dirtmidget33
-
Heavy Hitter
-
Posts:
-
Joined:Tue May 13, 2014 5:22 pm
The safety wire was .032 stainless listed as 302/304. I normally have .020 also but did not order after I ran out last time. The .020 I had was iconel need to get more.
why use standard nozzles after gas lens where invented. Kinda of like starting fires by rubbing sticks together.
exnailpounder
- exnailpounder
-
Weldmonger
-
Posts:
-
Joined:Thu Dec 25, 2014 9:25 am
-
Location:near Chicago
My machine will only go to 5 amps with a .040 tungsten...which I don't have so you own this thread....for nowdirtmidget33 wrote:The safety wire was .032 stainless listed as 302/304. I normally have .020 also but did not order after I ran out last time. The .020 I had was iconel need to get more.


Ifyoucantellmewhatthissaysiwillbuyyouabeer.
dirtmidget33
- dirtmidget33
-
Heavy Hitter
-
Posts:
-
Joined:Tue May 13, 2014 5:22 pm
Sure I could get lot better results with .020 or smaller filler, cheater lens, and a tungsten that's not crapped up. Need a cheater for project I'm working on anyway. Its a lightwieght prototype part, otherwise I would post pics of that also. This is what tungsten looked like a little worse now then when I started since I dipped it earlier then again on the blade. One of my other sharpened .040 thrown in to show grind I use on them most of time. I don't have any .020 tungsten or accessories for it, as small as .040 is not sure I could even see using .020 tungstenexnailpounder wrote: My machine will only go to 5 amps with a .040 tungsten...which I don't have so you own this thread....for now![]()
- 0824161326.jpg (25.12 KiB) Viewed 1166 times
What machine where you using?
I guess the Miller Sycrowave 210 seen that in your signature.
why use standard nozzles after gas lens where invented. Kinda of like starting fires by rubbing sticks together.
dirtmidget33
- dirtmidget33
-
Heavy Hitter
-
Posts:
-
Joined:Tue May 13, 2014 5:22 pm
Gave it another shot before calling it a day. Tried 2 two sets One set was a total waste tried something different, this was other one. These blades real brittle in HAZ
Not results that I'm happy with.
- 0824161621a.jpg (28.53 KiB) Viewed 1156 times
why use standard nozzles after gas lens where invented. Kinda of like starting fires by rubbing sticks together.
John Chamorro
- John Chamorro
-
Guide
-
Posts:
-
Joined:Thu Mar 19, 2015 9:44 am
-
Location:San Antonio Valley Peoples Republic of Californy
I sort of got it! My first was a disaster. After reading all the tips I did a slight lap with 1/16 tungsten, .032 safety wire at 18 amps. My biggest problem was staying on the joint. I couldn't see it at all. I went back over it staying off to the side a bit. It aint great but for my second shot at it, it ain't too bad. I'll post a pic when I get my pc back from the computer morgue.
I don't know it all but I'm working on it.
- MosquitoMoto
-
Weldmonger
-
Posts:
-
Joined:Sat Aug 01, 2015 8:38 am
-
Location:The Land Down Under
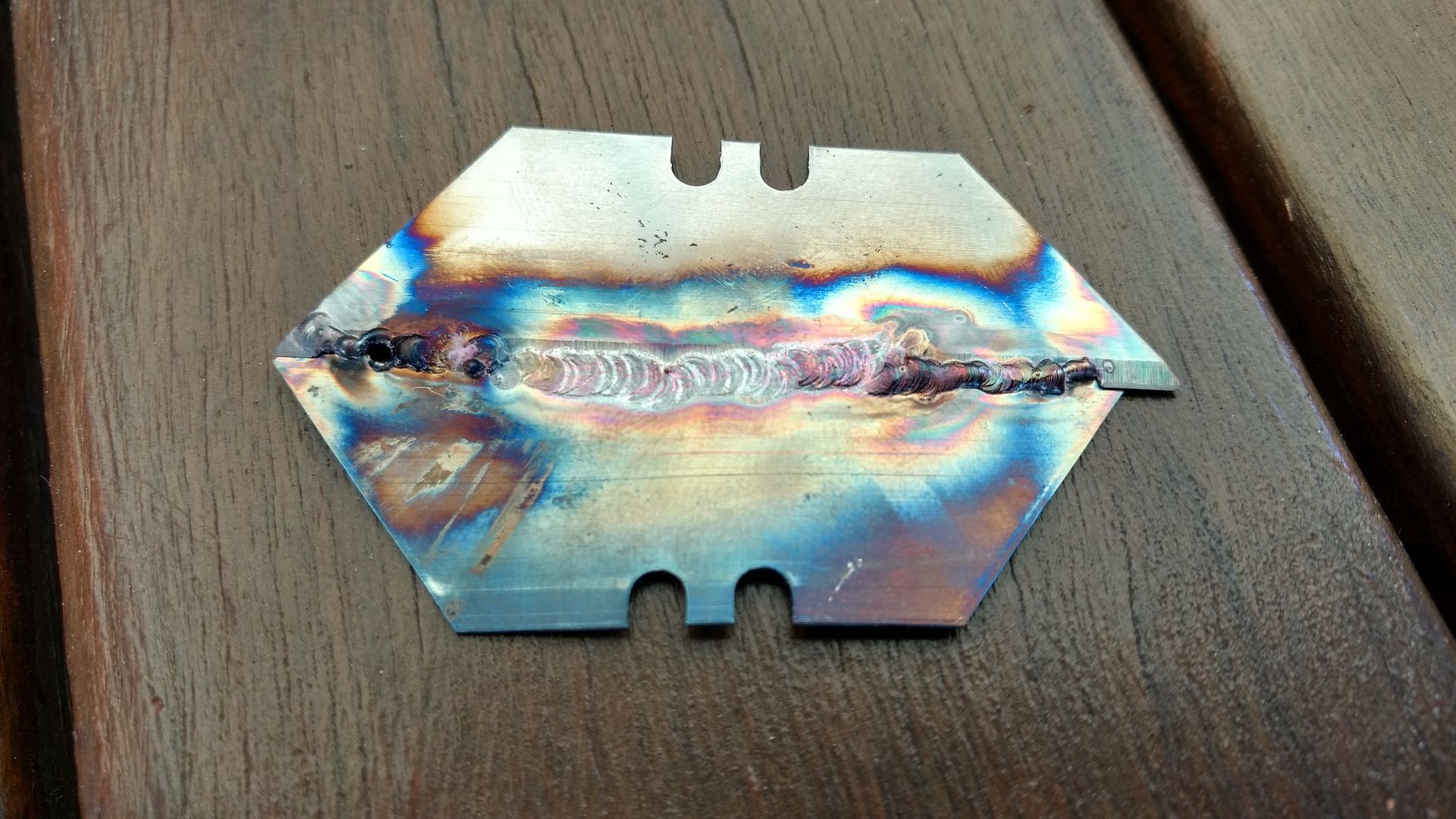
My poor effort.
I did everything wrong at every step. I came over all inspired, then realised that I had only two blades in my shed...and that both were used...and they were different to one another.
Cleaned them up and made a start. Should have spent time clamping but didn't. The disastrous ends are where I touched down and the tungsten stuck, lifting the blades. D'oh!
Used my Metalmaster 215 at 15 amps with pedal. Needle sharp 1.6mm tungsten, 2% Lanthanated. As filler I used .025 Mig wire.
Needless to say I have a pack of fresh, clean cutter blades on their way in the post right now!
Kym
- MosquitoMoto
-
Weldmonger
-
Posts:
-
Joined:Sat Aug 01, 2015 8:38 am
-
Location:The Land Down Under
It's a pretty good cover story!sedanman wrote:My local Home Depot is out of razor blades. That's my story , and I'm sticking to it. Lol

And you can see what happens if you try to weld used blades. (Used blades misbehaving is MY excuse and I'm sticking to it!)
Kym
exnailpounder
- exnailpounder
-
Weldmonger
-
Posts:
-
Joined:Thu Dec 25, 2014 9:25 am
-
Location:near Chicago
Kym....thats not too bad. This isn't easy and all of our welds look like shit. You're way too hard on yourself. Thin metal is a bitch and I think you did well.MosquitoMoto wrote:It's a pretty good cover story!sedanman wrote:My local Home Depot is out of razor blades. That's my story , and I'm sticking to it. Lol![]()
And you can see what happens if you try to weld used blades. (Used blades misbehaving is MY excuse and I'm sticking to it!)
Kym
Ifyoucantellmewhatthissaysiwillbuyyouabeer.
exnailpounder
- exnailpounder
-
Weldmonger
-
Posts:
-
Joined:Thu Dec 25, 2014 9:25 am
-
Location:near Chicago
I noticed they do get really brittle. I f someone ever comes to me and wants me to weld a bunch of razor blades together, I can lie and say it's not a good idea because they get brittle. That or admit I suckdirtmidget33 wrote:Gave it another shot before calling it a day. Tried 2 two sets One set was a total waste tried something different, this was other one. These blades real brittle in HAZ0824161621a.jpgNot results that I'm happy with.

Ifyoucantellmewhatthissaysiwillbuyyouabeer.
exnailpounder
- exnailpounder
-
Weldmonger
-
Posts:
-
Joined:Thu Dec 25, 2014 9:25 am
-
Location:near Chicago
OK God dammit..I am going to betray myself and go to AirGas in the morning and get a .040 electrode and gas lens setup. Thanks everybody for being competitive...now you have unleashed the beast 

Ifyoucantellmewhatthissaysiwillbuyyouabeer.
dirtmidget33
- dirtmidget33
-
Heavy Hitter
-
Posts:
-
Joined:Tue May 13, 2014 5:22 pm
Damn your gonna make me buy a .020 thenexnailpounder wrote:OK God dammit..I am going to betray myself and go to AirGas in the morning and get a .040 electrode and gas lens setup. Thanks everybody for being competitive...now you have unleashed the beast


why use standard nozzles after gas lens where invented. Kinda of like starting fires by rubbing sticks together.
exnailpounder
- exnailpounder
-
Weldmonger
-
Posts:
-
Joined:Thu Dec 25, 2014 9:25 am
-
Location:near Chicago
To hell with you...I"M gonna buy a.020dirtmidget33 wrote:Damn your gonna make me buy a .020 thenexnailpounder wrote:OK God dammit..I am going to betray myself and go to AirGas in the morning and get a .040 electrode and gas lens setup. Thanks everybody for being competitive...now you have unleashed the beastand micro tig filler They do make .005 and .007 think its like 9 or ten inches long. Think it's like 60 or 70 bucks for 25 pieces too


Ifyoucantellmewhatthissaysiwillbuyyouabeer.
dirtmidget33
- dirtmidget33
-
Heavy Hitter
-
Posts:
-
Joined:Tue May 13, 2014 5:22 pm
It's on NOWexnailpounder wrote: To hell with you...I"M gonna buy a.020Im gonna buy a damned microscope too.

Just a reference for anyone thinking about pulse, 5 amp to 8 amp pulse 2 times to 5 times a second hardly can tell it's pulsing it is so slight. Not worth hassle of messing with it and actually made things worse. Did total of three sets today That's the one I didn't get pics of the one with pulse.
why use standard nozzles after gas lens where invented. Kinda of like starting fires by rubbing sticks together.
- MosquitoMoto
-
Weldmonger
-
Posts:
-
Joined:Sat Aug 01, 2015 8:38 am
-
Location:The Land Down Under
Thanks nailer - but I'll keep working on it.exnailpounder wrote:Kym....thats not too bad. This isn't easy and all of our welds look like shit. You're way too hard on yourself. Thin metal is a bitch and I think you did well.MosquitoMoto wrote:It's a pretty good cover story!sedanman wrote:My local Home Depot is out of razor blades. That's my story , and I'm sticking to it. Lol![]()
And you can see what happens if you try to weld used blades. (Used blades misbehaving is MY excuse and I'm sticking to it!)
Kym
I love this competitive stuff. And you know what I'm really happy about? If nothing else I have proved that (as usual) if I play my part, this machine of mine will do anything I need it to do. What an awesome piece of kit.
Those new cutter blades can't come soon enough!
Kym
exnailpounder
- exnailpounder
-
Weldmonger
-
Posts:
-
Joined:Thu Dec 25, 2014 9:25 am
-
Location:near Chicago
motox wrote:I'm looking for 1/4" thick razor blades.
then ill give it a try
craig



Ifyoucantellmewhatthissaysiwillbuyyouabeer.
- entity-unknown
-
Ace
-
Posts:
-
Joined:Mon Jul 18, 2016 2:07 pm
-
Location:Mesa, AZ
Now are you talking about your welder or your motorcycle?MosquitoMoto wrote: I love this competitive stuff. And you know what I'm really happy about? If nothing else I have proved that (as usual) if I play my part, this machine of mine will do anything I need it to do. What an awesome piece of kit.
Kym

I'm lovin this thread! I might have to give this a try once I finish my stand. See what this 256Si (really me) is capable of!
Lincoln Electric AC225
Everlast PowerPro Multi-Process TIG/Stick/Plasma 256Si
Everlast W300 WaterCooler
Optrel e684x1
22+ Year Security Engineer developing cool shit and stoppin hackers
Everlast PowerPro Multi-Process TIG/Stick/Plasma 256Si
Everlast W300 WaterCooler
Optrel e684x1
22+ Year Security Engineer developing cool shit and stoppin hackers

- maker of things
-
Guide
-
Posts:
-
Joined:Tue Jul 19, 2016 6:52 am
I think the fun thing about this challenge is, you really can't use/blame the machine. As long as the amps can go low enough, it's all about the individual holding the torch. I would wager someone that can run razor blades reliably could do so on a Harbor freight tig just as well as a Dynasty, all things being equal (torch tungsten etc).
I might try my #9 fixed gold shade a try to see if that reflects some more light to make the weld puddle more visible.
I might try my #9 fixed gold shade a try to see if that reflects some more light to make the weld puddle more visible.
-Jon
I learned how to weld at night, but not last night. (despite how my weld looks)
Lincoln Viking 3350 K3034-2&3
Dynasty 210DX w/cps and coolmate3
Lincoln Power Mig 180c
hermit.shed on instagram
I learned how to weld at night, but not last night. (despite how my weld looks)
Lincoln Viking 3350 K3034-2&3
Dynasty 210DX w/cps and coolmate3
Lincoln Power Mig 180c
hermit.shed on instagram
exnailpounder
- exnailpounder
-
Weldmonger
-
Posts:
-
Joined:Thu Dec 25, 2014 9:25 am
-
Location:near Chicago
- 20160825_105854.jpg (34.85 KiB) Viewed 1097 times
The secret is...don't light up on the overlapped blade, light up on the blade underneath it and get your puddle and then wash up onto the overlapped blade. This is where you need to dip or you will just burn back the top blade. You need to cool that puddle as soon as your arc touches that overlapped blade or its burns back. I couldn't find anything small enough to use for filler wire SO...I clipped some strands out of a cup brush and tacked them together for filler wire.It was like dipping with a piece of hair



Last edited by exnailpounder on Thu Aug 25, 2016 12:26 pm, edited 2 times in total.
Ifyoucantellmewhatthissaysiwillbuyyouabeer.
Return to “Tig Welding - Tig Welding Aluminum - Tig Welding Techniques - Aluminum Tig Welding”
Jump to
- Introductions & How to Use the Forum
- ↳ Welcome!
- ↳ Member Introductions
- ↳ How to Use the Forum
- ↳ Moderator Applications
- Welding Discussion
- ↳ Metal Cutting
- ↳ Tig Welding - Tig Welding Aluminum - Tig Welding Techniques - Aluminum Tig Welding
- ↳ Mig and Flux Core - gas metal arc welding & flux cored arc welding
- ↳ Stick Welding/Arc Welding - Shielded Metal Arc Welding
- ↳ Welding Forum General Shop Talk
- ↳ Welding Certification - Stick/Arc Welding, Tig Welding, Mig Welding Certification tests - Welding Tests of all kinds
- ↳ Welding Projects - Welding project Ideas - Welding project plans
- ↳ Product Reviews
- ↳ Fuel Gas Heating
- Welding Tips & Tricks
- ↳ Video Discussion
- ↳ Wish List
- Announcements & Feedback
- ↳ Forum News
- ↳ Suggestions, Feedback and Support
- Welding Marketplace
- ↳ Welding Jobs - Industrial Welding Jobs - Pipe Welding Jobs - Tig Welding Jobs
- ↳ Classifieds - Buy, Sell, Trade Used Welding Equipment
- Welding Resources
- ↳ Tradeshows, Seminars and Events
- ↳ The Welding Library
- ↳ Education Opportunities