They have little burn marks in the castings with the shape of the ants. It's really cool. Pompeii style lolex framie wrote:Those sculptures are fantastic.
They are however bloody hard on the ants
Tig welding tips, questions, equipment, applications, instructions, techniques, tig welding machines, troubleshooting tig welding process
Instagram: @nathanppiatt
Owner/welder at Homegrown Metal Fab
Lincoln Weld-Pak 125 HD
Lincoln AC/DC 225/125
Lincoln Port-a-torch
30" 40 ton homegrown press brake
Northern Industrial1HP 3/4" chuck, 16 speed drill press
Owner/welder at Homegrown Metal Fab
Lincoln Weld-Pak 125 HD
Lincoln AC/DC 225/125
Lincoln Port-a-torch
30" 40 ton homegrown press brake
Northern Industrial1HP 3/4" chuck, 16 speed drill press
- Otto Nobedder
-
Weldmonger
-
Posts:
-
Joined:Thu Jan 06, 2011 11:40 pm
-
Location:Near New Orleans
No, actually the weldment was a tee-joint (a hoop of rolled angle to stiffen the circumference, fillet welded each side), and the helium was flowing under the leg of the tee. I isolated by drilling through the weld and die-grinding to the vessel inner surface to interrupt the flow. I had about 6" of weld to replace after the repair, and a dozen holes to weld up.ex framie wrote:...So in the case you mentioned above did that mean you had 5ft of weld to replace?
Steve S
- Otto Nobedder
-
Weldmonger
-
Posts:
-
Joined:Thu Jan 06, 2011 11:40 pm
-
Location:Near New Orleans
I love the anthill castings! I think that idea would work well here, where fire ants will dig in clay, making a very solid casting medium. Flushing out the casting from the hard clay may be a challenge, though.
Steve S
Steve S
They put about 40 hours into big ones. They mount em on exotic wood bases and fancy paing. They had one that was smaller than the one I worked on go for over a grand.Otto Nobedder wrote:I love the anthill castings! I think that idea would work well here, where fire ants will dig in clay, making a very solid casting medium. Flushing out the casting from the hard clay may be a challenge, though.
Steve S
Instagram: @nathanppiatt
Owner/welder at Homegrown Metal Fab
Lincoln Weld-Pak 125 HD
Lincoln AC/DC 225/125
Lincoln Port-a-torch
30" 40 ton homegrown press brake
Northern Industrial1HP 3/4" chuck, 16 speed drill press
Owner/welder at Homegrown Metal Fab
Lincoln Weld-Pak 125 HD
Lincoln AC/DC 225/125
Lincoln Port-a-torch
30" 40 ton homegrown press brake
Northern Industrial1HP 3/4" chuck, 16 speed drill press
You'll have a very unpleasant experience if you pour liquid metal in moisty clay.Otto Nobedder wrote:I love the anthill castings! I think that idea would work well here, where fire ants will dig in clay, making a very solid casting medium. Flushing out the casting from the hard clay may be a challenge, though.
Steve S
Pictures from my scrap collection:
http://forum.weldingtipsandtricks.com/v ... f=9&t=5677
http://forum.weldingtipsandtricks.com/v ... f=9&t=5677
- subwayrocket
-
Ace
-
Posts:
-
Joined:Thu Aug 13, 2015 11:38 pm
-
Location:Scranton/WilkesBarre, Pennsylvania
At the end of practicing, I decided to do some soda cans again . Getting a little better each time . They seem to be really good for foot pedal and puddle control practice .
-------------------------------------------------------------------
-------------------------------------------------------------------
Other side, I got a small burn thru but was able to wash in some filler with pedal pumping.
-------------------------------------------------------------------
- 1PopCan.jpg (44.71 KiB) Viewed 2044 times
Other side, I got a small burn thru but was able to wash in some filler with pedal pumping.
- 2PopCan.jpg (39.4 KiB) Viewed 2044 times
Had to make some ports so I can add some sample valves to 8 vessels. 316L, back purged
- Attachments
-
- IMG_20151016_225538170_HDR.jpg (49.84 KiB) Viewed 1965 times
-
- IMG_20151016_225546549_HDR.jpg (74.64 KiB) Viewed 1965 times
I weld stainless, stainless and more stainless...Food Industry, sanitary process piping, vessels, whatever is needed, I like to make stuff.
ASME IX, AWS 17.1, D1.1
Instagram #RNHFAB
ASME IX, AWS 17.1, D1.1
Instagram #RNHFAB
- subwayrocket
-
Ace
-
Posts:
-
Joined:Thu Aug 13, 2015 11:38 pm
-
Location:Scranton/WilkesBarre, Pennsylvania
subwayrocket wrote:Nice welds. that thing looks like it could get your name on a list though ...haha
Lol...same thing a co-workers said when he popped in and saw me welding them.
I weld stainless, stainless and more stainless...Food Industry, sanitary process piping, vessels, whatever is needed, I like to make stuff.
ASME IX, AWS 17.1, D1.1
Instagram #RNHFAB
ASME IX, AWS 17.1, D1.1
Instagram #RNHFAB
- subwayrocket
-
Ace
-
Posts:
-
Joined:Thu Aug 13, 2015 11:38 pm
-
Location:Scranton/WilkesBarre, Pennsylvania
Usually after I practice, I like to "break" some junk then try to weld it back together. I pulled a few of these brake and clutch levers off a motorcycle down the scrapyard. These things like to snap when you have a good offroad crash ...
Anyway I snapped this one in the vise , cleaned it up with a die grinder, put a small bevel and lightly shaved the surface where the bead would fan out . Finally , I gave it the ole torture test . It started bending down the opposite end so I flipped it to try and snap it at the weld. Here's a vid . I believe this is heat treated cast aluminum .
https://youtu.be/YwK-t6qNRJM
Anyway I snapped this one in the vise , cleaned it up with a die grinder, put a small bevel and lightly shaved the surface where the bead would fan out . Finally , I gave it the ole torture test . It started bending down the opposite end so I flipped it to try and snap it at the weld. Here's a vid . I believe this is heat treated cast aluminum .
https://youtu.be/YwK-t6qNRJM
Cool vid. That new break was probably the end of the HAZ. I'm curious if someone knows what could be done to a small part like this to keep that from happening. I may have some small parts repairs coming up that will be stressed and I'm not sure if a preheat and cool down process will help.
I have more questions than answers
Josh
Josh
- subwayrocket
-
Ace
-
Posts:
-
Joined:Thu Aug 13, 2015 11:38 pm
-
Location:Scranton/WilkesBarre, Pennsylvania
Thanks much Poland. I'm just a guy in my garage havin fun...not a professional like you guys. When I broke the part, it had very fine grain structure in the break. I suspect it was heat treated after casting. My weld nullified that ...haha
I think you'd have to re-establish fine grain structure throughout the whole part) i.e. heat and hold it at like 950 for an hour then very quick quench ...then heat it again to like 375 for and hold there a few hours followed by an ambient air cool down .
I notice on the toughest cast alum scrap parts I've welded (Honda auto parts), they have a very file grain structure...looks like 120 or 220 grit in the break when you work hard to bust it up ...and the cast that busts up easier has larger grain structure...a Cast Alum transmission housing I practiced on recently , the grains looked like 60 or 80 grit . I sledge hammered that part after welding it(video here somewhere)...the last of several breaks was about 1/2" away from the weld ...right at the end of the HAZ . Just like this lever Interesting stuff ...but no one's life is hanging off anything I weld. Brake/clutch/shift levers often break in a race/crash ...it's nice to be able to fix them ...I don't see the little extra ductility as a prob . I sure would like to be able to heat treat though ....Someone did say "you start to accumulate things" when you get into TIG.....so true
I think you'd have to re-establish fine grain structure throughout the whole part) i.e. heat and hold it at like 950 for an hour then very quick quench ...then heat it again to like 375 for and hold there a few hours followed by an ambient air cool down .
I notice on the toughest cast alum scrap parts I've welded (Honda auto parts), they have a very file grain structure...looks like 120 or 220 grit in the break when you work hard to bust it up ...and the cast that busts up easier has larger grain structure...a Cast Alum transmission housing I practiced on recently , the grains looked like 60 or 80 grit . I sledge hammered that part after welding it(video here somewhere)...the last of several breaks was about 1/2" away from the weld ...right at the end of the HAZ . Just like this lever Interesting stuff ...but no one's life is hanging off anything I weld. Brake/clutch/shift levers often break in a race/crash ...it's nice to be able to fix them ...I don't see the little extra ductility as a prob . I sure would like to be able to heat treat though ....Someone did say "you start to accumulate things" when you get into TIG.....so true
Yes. Accumulation. I think it's a registered welder disease. I've been pondering the small gas fire forges for black smiths and horse shoe ers. Think I may have to add a modulating gas valve but I might be able to get double duty out of it.
I have more questions than answers
Josh
Josh
ex framie
- ex framie
-
Ace
-
Posts:
-
Joined:Sun Aug 09, 2015 1:09 am
-
Location:Brisbane QLD Land of oz
Subway,
I would be happy to use that repaired lever, fit for purpose etc.
Josh,
To remove the haz would require the part to be normalised and then heat treated again.
Google aluminium heat treatment, I think its doable at home.
I would be happy to use that repaired lever, fit for purpose etc.
Josh,
To remove the haz would require the part to be normalised and then heat treated again.
Google aluminium heat treatment, I think its doable at home.
Pete
God gave man 2 heads and only enough blood to run 1 at a time. Who said God didn't have a sense of humour.....
God gave man 2 heads and only enough blood to run 1 at a time. Who said God didn't have a sense of humour.....
- subwayrocket
-
Ace
-
Posts:
-
Joined:Thu Aug 13, 2015 11:38 pm
-
Location:Scranton/WilkesBarre, Pennsylvania
Would this be what I described above ? I think I saw a video somewhere that used only one step ...that may have been 7005 though . Thanksex framie wrote: To remove the haz would require the part to be normalised and then heat treated again.
Google aluminium heat treatment, I think its doable at home.
- MosquitoMoto
-
Weldmonger
-
Posts:
-
Joined:Sat Aug 01, 2015 8:38 am
-
Location:The Land Down Under
Wow Sub, sometimes I think we really are following the same path (except you're further down the path!)
I went out to my bench last night and broke an old KTM lever. Now for the welding.
If I can nail this it might be handy as long as I can make the repair invisible. There seems to be some demand lately for shorty levers that look otherwise standard. But of course creating a brake lever that won't become a 'break' lever is a big responsibility. Not something to be taken lightly.
Kym
I went out to my bench last night and broke an old KTM lever. Now for the welding.
If I can nail this it might be handy as long as I can make the repair invisible. There seems to be some demand lately for shorty levers that look otherwise standard. But of course creating a brake lever that won't become a 'break' lever is a big responsibility. Not something to be taken lightly.
Kym
- subwayrocket
-
Ace
-
Posts:
-
Joined:Thu Aug 13, 2015 11:38 pm
-
Location:Scranton/WilkesBarre, Pennsylvania
Haha yeah ...I put a bevel in it thinking i'd get better penetration ...but this small part heats up quick anyway.MosquitoMoto wrote:Wow Sub, sometimes I think we really are following the same path ...........
If I can nail this it might be handy as long as I can make the repair invisible. There seems to be some demand lately for shorty levers that look otherwise standard.
Kym
At least with the bevel you know you're welded thru it pretty good, should you decide to grind off some of it later .
The hardest part of it was getting the 2 halves lined up and pushed together to tack them up.
I'd suggest using a 1/4" carbide burr to make the bevel, and also to lightly skim the area that the bead will fan out into.
I've noticed skimming with a die grinder has made cast Alum welds go better. Good luck twin brother !
- MosquitoMoto
-
Weldmonger
-
Posts:
-
Joined:Sat Aug 01, 2015 8:38 am
-
Location:The Land Down Under
I repaired a rear brake pedal a few weeks ago and the hardest part by far was set up and tacking. Built up lots of heat very quickly.
Someone on this forum suggested that the part may have annealed and softened at the HAZ but I had no problem with that situation on a rear brake pedal. It means it would possibly bend rather than break on contact with the track, and also, I nev use the rear brake when I'm racing anyhow.
But the front brake lever...I definitely use that! And when you're trying to out brake a fellow racer and carrying 180 into the hairpin at the end of the straight, the last thing you need is for your front brake lever to bend or break. So I'll be carrying out some very thorough testing when I'm finished with my lever weld.
Kym
Someone on this forum suggested that the part may have annealed and softened at the HAZ but I had no problem with that situation on a rear brake pedal. It means it would possibly bend rather than break on contact with the track, and also, I nev use the rear brake when I'm racing anyhow.
But the front brake lever...I definitely use that! And when you're trying to out brake a fellow racer and carrying 180 into the hairpin at the end of the straight, the last thing you need is for your front brake lever to bend or break. So I'll be carrying out some very thorough testing when I'm finished with my lever weld.
Kym
- subwayrocket
-
Ace
-
Posts:
-
Joined:Thu Aug 13, 2015 11:38 pm
-
Location:Scranton/WilkesBarre, Pennsylvania
It builds heat quick but you just do quick full pedal bursts ...maybe make like 2-3 beads and stop...wire brush a little .MosquitoMoto wrote:I repaired a rear brake pedal a few weeks ago.
Built up lots of heat very quickly.
Someone on this forum suggested that the part may have annealed and softened at the HAZ
Kym
It definitely gets a little softer a half inch either side of the weld . Funny how we're always doing the same projects, each on the other side of the globe !
- subwayrocket
-
Ace
-
Posts:
-
Joined:Thu Aug 13, 2015 11:38 pm
-
Location:Scranton/WilkesBarre, Pennsylvania
never thought of doing that . Alot of this cast stuff is either odd shape , or something i'd be afraid to start peening on .motox wrote:you can try peening the haz areas and work harden them.
craig
I'm thinking with these alum cast parts, heat treating would be the way to go . Open to suggestions though , from anyone that does a lot of this. With these cast alum parts, i'm thinking about what kind of service will this part be put back into...is it gona be but under high loads , cycles , impacts, what is the consequence if it fails . Someone recently asked me to weld some motocross handlebars ...They will see extreme loads, countless impacts and cycles ...and the consequence of it failing are possibly someones life . If a foot shifter or hand lever bends, it's no biggie ... guess i'm getting off topic here ...no clue where im going with this ...haha
kiwi2wheels
- kiwi2wheels
-
Ace
-
Posts:
-
Joined:Sun Feb 17, 2013 10:27 am
Shorten the lever at the ball.MosquitoMoto wrote:Wow Sub, sometimes I think we really are following the same path (except you're further down the path!)
I went out to my bench last night and broke an old KTM lever. Now for the welding.
If I can nail this it might be handy as long as I can make the repair invisible. There seems to be some demand lately for shorty levers that look otherwise standard. But of course creating a brake lever that won't become a 'break' lever is a big responsibility. Not something to be taken lightly.
Kym
Did some aluminum in the morning and steel in the afternoon today. I always have to reprogram myself when going from one material to the other. The first few beads on the steel were a trip.
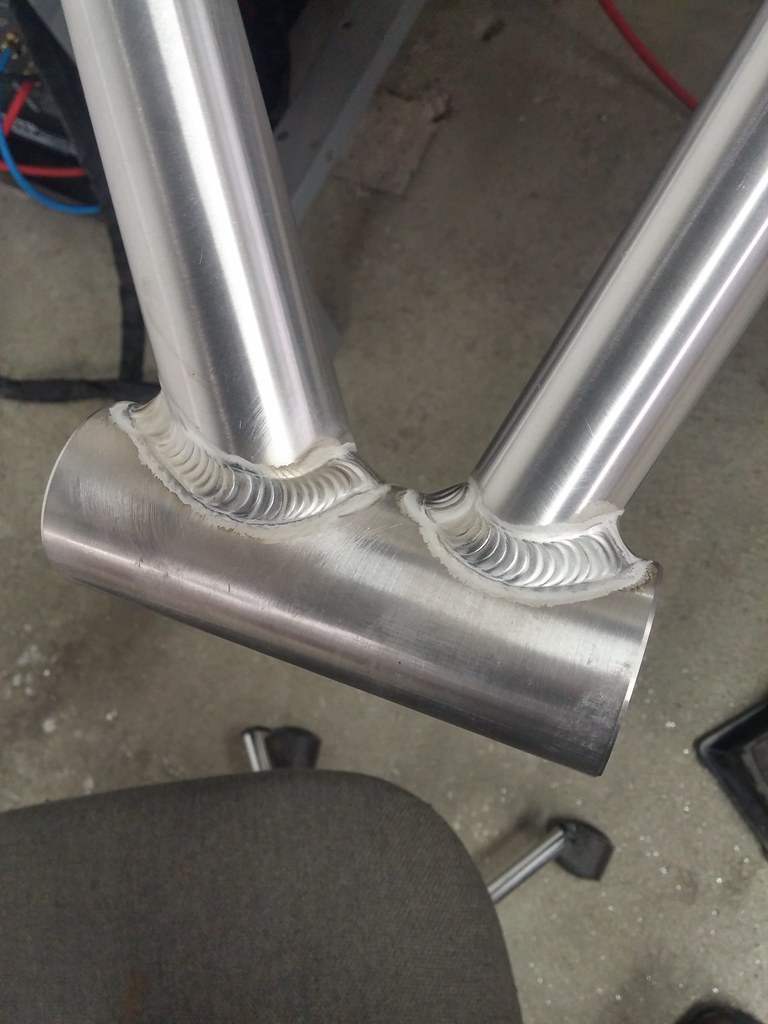
ally by Mike Zanconato, on Flickr
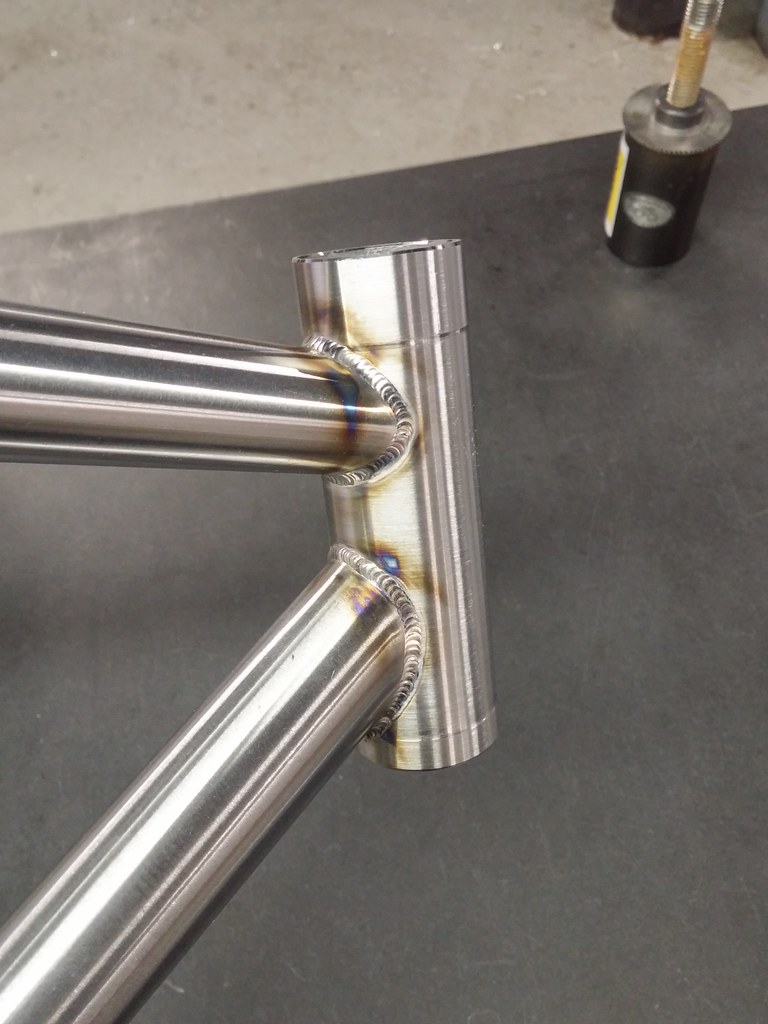
steel by Mike Zanconato, on Flickr

steel by Mike Zanconato, on Flickr

steel by Mike Zanconato, on Flickr
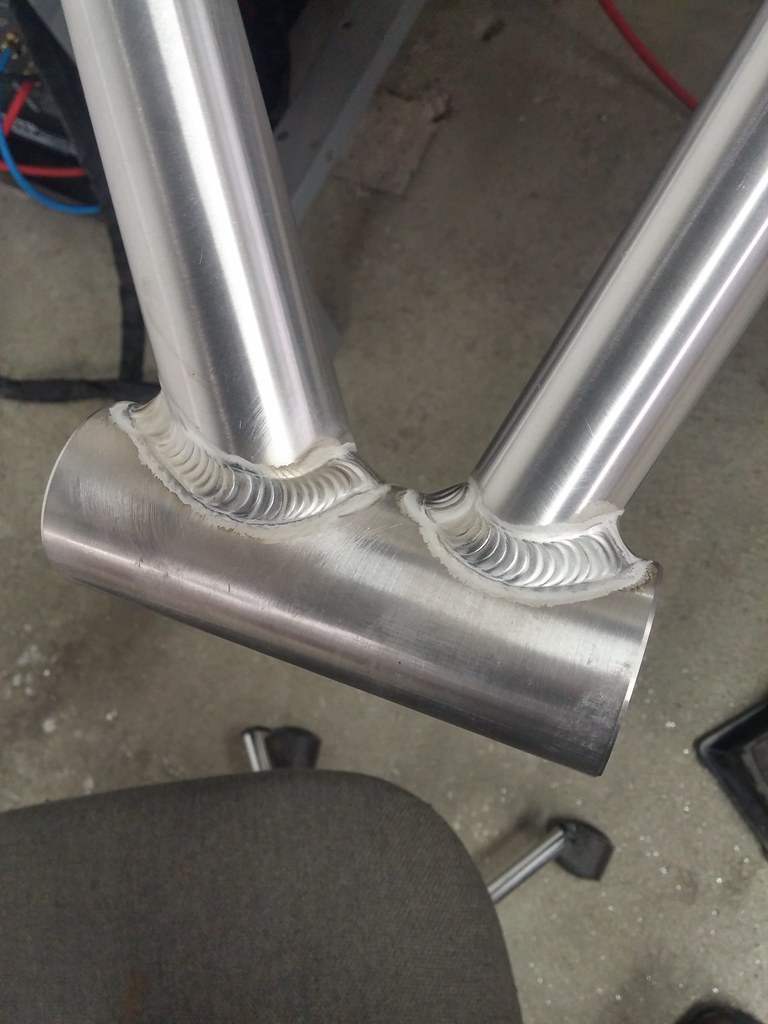
ally by Mike Zanconato, on Flickr
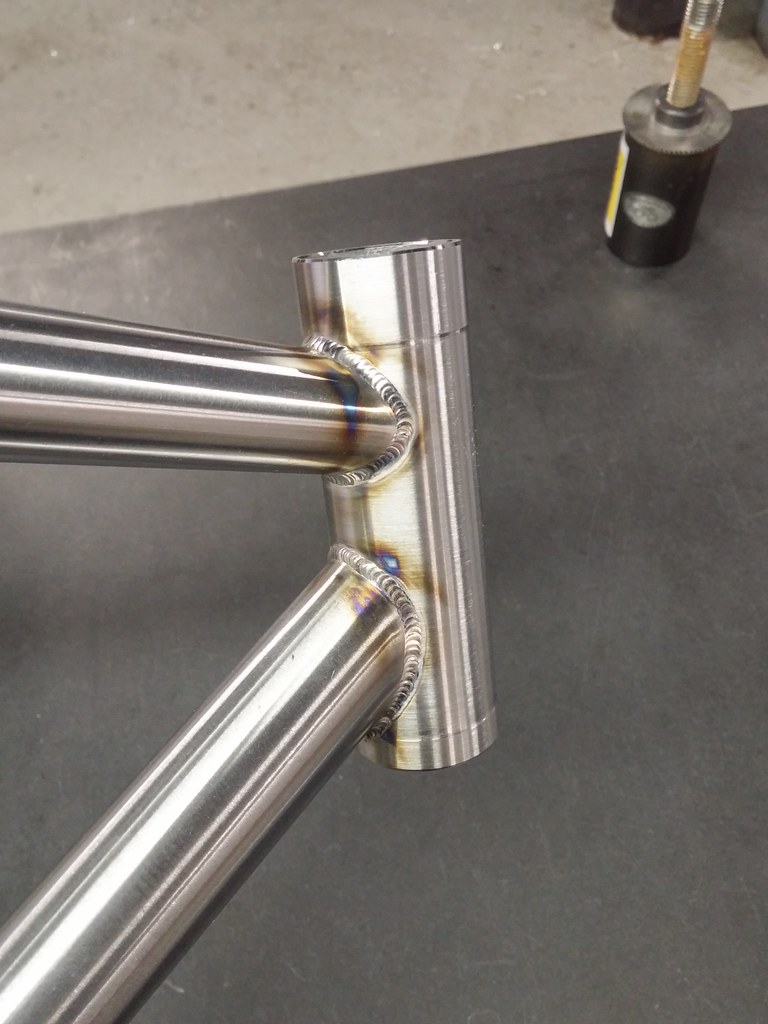
steel by Mike Zanconato, on Flickr

steel by Mike Zanconato, on Flickr

steel by Mike Zanconato, on Flickr
Return to “Tig Welding - Tig Welding Aluminum - Tig Welding Techniques - Aluminum Tig Welding”
Jump to
- Introductions & How to Use the Forum
- ↳ Welcome!
- ↳ Member Introductions
- ↳ How to Use the Forum
- ↳ Moderator Applications
- Welding Discussion
- ↳ Metal Cutting
- ↳ Tig Welding - Tig Welding Aluminum - Tig Welding Techniques - Aluminum Tig Welding
- ↳ Mig and Flux Core - gas metal arc welding & flux cored arc welding
- ↳ Stick Welding/Arc Welding - Shielded Metal Arc Welding
- ↳ Welding Forum General Shop Talk
- ↳ Welding Certification - Stick/Arc Welding, Tig Welding, Mig Welding Certification tests - Welding Tests of all kinds
- ↳ Welding Projects - Welding project Ideas - Welding project plans
- ↳ Product Reviews
- ↳ Fuel Gas Heating
- Welding Tips & Tricks
- ↳ Video Discussion
- ↳ Wish List
- Announcements & Feedback
- ↳ Forum News
- ↳ Suggestions, Feedback and Support
- Welding Marketplace
- ↳ Welding Jobs - Industrial Welding Jobs - Pipe Welding Jobs - Tig Welding Jobs
- ↳ Classifieds - Buy, Sell, Trade Used Welding Equipment
- Welding Resources
- ↳ Tradeshows, Seminars and Events
- ↳ The Welding Library
- ↳ Education Opportunities