
Tig welding tips, questions, equipment, applications, instructions, techniques, tig welding machines, troubleshooting tig welding process
- entity-unknown
-
Ace
-
Posts:
-
Joined:Mon Jul 18, 2016 2:07 pm
-
Location:Mesa, AZ
Rick_H, your work is always inspiring and something to aspire for 

Lincoln Electric AC225
Everlast PowerPro Multi-Process TIG/Stick/Plasma 256Si
Everlast W300 WaterCooler
Optrel e684x1
22+ Year Security Engineer developing cool shit and stoppin hackers
Everlast PowerPro Multi-Process TIG/Stick/Plasma 256Si
Everlast W300 WaterCooler
Optrel e684x1
22+ Year Security Engineer developing cool shit and stoppin hackers

Here's a stupid little one. Just a .25 shaft with a 4142 drive gizmo on the end. No filler, fusion, 30 amps. Shaft is hard high carbon. I used to braze these. Last about a year. We'll see how this fairs. I'll temper at 500 to keep the end tough. It's a Flintstonish drive coupler from a detachable hopper.
Sorry for wasting your time. I'll try to get something cool someday.
Sorry for wasting your time. I'll try to get something cool someday.
- Attachments
-
- 1471302975242-844531791.jpg (40.42 KiB) Viewed 1881 times
Stone knives and bearskins.....and a NEW EVERLAST 164SI !!!
That's my newly shared work welder.
At home I got a Power Tig 185 DV. Nice, but no plasma cutting... Nice tight arc after a second.
That's my newly shared work welder.
At home I got a Power Tig 185 DV. Nice, but no plasma cutting... Nice tight arc after a second.
No apologies necessary. Everyone's experience is different and therefore everyone has something to bring to the table that we can learn from. Even these little "gizmos" are of interest and a point of discussion.
I certainly would be interested to know how it fares. I personally think the weld, without filler, will be weak and break sooner than later. Keep us posted!
I certainly would be interested to know how it fares. I personally think the weld, without filler, will be weak and break sooner than later. Keep us posted!
Flat out like a lizard drinkin'
Thanks! I had a piece of 309 in my hand but didn't use it after I saw the puddle. I'll tell you one thing. This was easier than brazing. I tried a similar piece first at 40 amps and melted it to a ball. I'm getting used to it.
Stone knives and bearskins.....and a NEW EVERLAST 164SI !!!
That's my newly shared work welder.
At home I got a Power Tig 185 DV. Nice, but no plasma cutting... Nice tight arc after a second.
That's my newly shared work welder.
At home I got a Power Tig 185 DV. Nice, but no plasma cutting... Nice tight arc after a second.
- maker of things
-
Guide
-
Posts:
-
Joined:Tue Jul 19, 2016 6:52 am
To me it's cool when you have the ability to make the thing you need instead of buying it.nelson wrote: I'll try to get something cool someday.
I welded some tabs on a piece of sheet metal to make a shroud for a window mount a/c unit. How's that for boring?
- IMG_20160813_111935464_HDR.jpg (92.52 KiB) Viewed 1831 times
-Jon
I learned how to weld at night, but not last night. (despite how my weld looks)
Lincoln Viking 3350 K3034-2&3
Dynasty 210DX w/cps and coolmate3
Lincoln Power Mig 180c
hermit.shed on instagram
I learned how to weld at night, but not last night. (despite how my weld looks)
Lincoln Viking 3350 K3034-2&3
Dynasty 210DX w/cps and coolmate3
Lincoln Power Mig 180c
hermit.shed on instagram
- MosquitoMoto
-
Weldmonger
-
Posts:
-
Joined:Sat Aug 01, 2015 8:38 am
-
Location:The Land Down Under
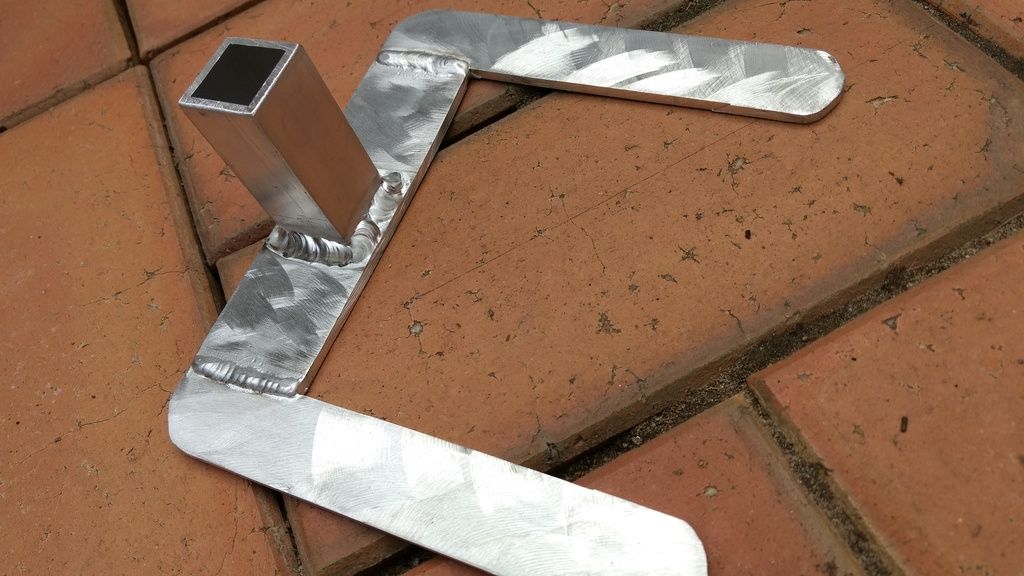
I have an entry in the What I Welded Today 'Boring' category that I feel might rival Maker's previous post.
I do a lot of voice work, often on the run using a portable microphone. I recently added a 'popper stopper' wind sock to help stop explosive 'P' and 'T' sounds getting through and peaking the mic.
Needed a stand for it. Built this from scrap 3mm aluminium. It was old, oil-soaked aluminium that had been left outside, and yes, it misbehaved badly. Got it done in the end though just cleaning and cleaning again. Not pretty, but it works.
Kym
fredygump
- fredygump
-
Active Member
-
Posts:
-
Joined:Thu Feb 12, 2015 8:01 pm
-
Location:Rochester, MN
Working on a conveyor the last several days. I'm still an apprentice, but I guess I'm moving up? Three months ago I was working on the laser, fetching material and putting shop stickers on parts.
- Attachments
-
- IMG_20160816_113402.jpg (100.98 KiB) Viewed 1730 times
- MosquitoMoto
-
Weldmonger
-
Posts:
-
Joined:Sat Aug 01, 2015 8:38 am
-
Location:The Land Down Under
It was getting late and I didn't want to fill out all the paperwork to weld in an explosion proof environment not counting dragging all my safety gear. So I measured it all up and fabbed it all up in my small office/satellite shop in the a/c (damn it's been hot).
Fun times as you can see..lol
Fun times as you can see..lol
- Attachments
-
- IMG_20160816_232325495.jpg (30.84 KiB) Viewed 1707 times
-
- IMG_20160816_232313552.jpg (44.84 KiB) Viewed 1707 times
-
- IMG_20160816_233741481.jpg (77.23 KiB) Viewed 1707 times
-
- IMG_20160816_232244761.jpg (83.69 KiB) Viewed 1707 times
I weld stainless, stainless and more stainless...Food Industry, sanitary process piping, vessels, whatever is needed, I like to make stuff.
ASME IX, AWS 17.1, D1.1
Instagram #RNHFAB
ASME IX, AWS 17.1, D1.1
Instagram #RNHFAB
ex framie
- ex framie
-
Ace
-
Posts:
-
Joined:Sun Aug 09, 2015 1:09 am
-
Location:Brisbane QLD Land of oz
You need a longer and higher shop
Nice work as always.
Did you get it out after you built it?

Nice work as always.
Did you get it out after you built it?
Pete
God gave man 2 heads and only enough blood to run 1 at a time. Who said God didn't have a sense of humour.....
God gave man 2 heads and only enough blood to run 1 at a time. Who said God didn't have a sense of humour.....
- maker of things
-
Guide
-
Posts:
-
Joined:Tue Jul 19, 2016 6:52 am
Now when I read your posts you sound like Troy McClure in my head.MosquitoMoto wrote: I do a lot of voice work
- troy mcclure.JPG (32.9 KiB) Viewed 2001 times
Last edited by maker of things on Wed Aug 17, 2016 7:48 am, edited 1 time in total.
-Jon
I learned how to weld at night, but not last night. (despite how my weld looks)
Lincoln Viking 3350 K3034-2&3
Dynasty 210DX w/cps and coolmate3
Lincoln Power Mig 180c
hermit.shed on instagram
I learned how to weld at night, but not last night. (despite how my weld looks)
Lincoln Viking 3350 K3034-2&3
Dynasty 210DX w/cps and coolmate3
Lincoln Power Mig 180c
hermit.shed on instagram
Yeah it made it out..lol Ceiling in that room is 18', and it has a/c....lol Main shop was hot as hell..heheex framie wrote:You need a longer and higher shop![]()
Nice work as always.
Did you get it out after you built it?
I weld stainless, stainless and more stainless...Food Industry, sanitary process piping, vessels, whatever is needed, I like to make stuff.
ASME IX, AWS 17.1, D1.1
Instagram #RNHFAB
ASME IX, AWS 17.1, D1.1
Instagram #RNHFAB
exnailpounder
- exnailpounder
-
Weldmonger
-
Posts:
-
Joined:Thu Dec 25, 2014 9:25 am
-
Location:near Chicago
Hey Rick, question...I know you don't use filler when you do sanitary welds but I notice that from not using filler, the weld is a bit sunken in. Do you grind and polish that out? I remember a post you made awhile back about a belt sanding attachment for a grinder that helps you polish your welds.Whats the actual procedure? Also, did you ever get any of that flux cored SS rod that Coldman showed us?Rick_H wrote:Yeah it made it out..lol Ceiling in that room is 18', and it has a/c....lol Main shop was hot as hell..heheex framie wrote:You need a longer and higher shop![]()
Nice work as always.
Did you get it out after you built it?
Ifyoucantellmewhatthissaysiwillbuyyouabeer.
- maker of things
-
Guide
-
Posts:
-
Joined:Tue Jul 19, 2016 6:52 am
Mine is down right hideous but it is cutting the grass. Fixed MTD mower pot metal rear axle for a co-worker. Oil and dirt saturated, couldn't clean half of the areas to be welded. 4043 filler with 5% pure tungsten added (by me).MosquitoMoto wrote: Not pretty, but it works.
- IMG_20160610_125723486.jpg (38.72 KiB) Viewed 1976 times
- IMG_20160610_125744946.jpg (80.31 KiB) Viewed 1976 times
Last edited by maker of things on Wed Aug 17, 2016 1:15 pm, edited 1 time in total.
-Jon
I learned how to weld at night, but not last night. (despite how my weld looks)
Lincoln Viking 3350 K3034-2&3
Dynasty 210DX w/cps and coolmate3
Lincoln Power Mig 180c
hermit.shed on instagram
I learned how to weld at night, but not last night. (despite how my weld looks)
Lincoln Viking 3350 K3034-2&3
Dynasty 210DX w/cps and coolmate3
Lincoln Power Mig 180c
hermit.shed on instagram
The welds are basically flat, I use a belt attachment on my Metabo burnishing machine with a scotch brute belt....polishes out nice and pursue.exnailpounder wrote:Hey Rick, question...I know you don't use filler when you do sanitary welds but I notice that from not using filler, the weld is a bit sunken in. Do you grind and polish that out? I remember a post you made awhile back about a belt sanding attachment for a grinder that helps you polish your welds.Whats the actual procedure? Also, did you ever get any of that flux cored SS rod that Coldman showed us?Rick_H wrote:Yeah it made it out..lol Ceiling in that room is 18', and it has a/c....lol Main shop was hot as hell..heheex framie wrote:You need a longer and higher shop![]()
Nice work as always.
Did you get it out after you built it?
Never did get a reaponse
Last edited by Rick_H on Wed Aug 17, 2016 10:15 pm, edited 1 time in total.
I weld stainless, stainless and more stainless...Food Industry, sanitary process piping, vessels, whatever is needed, I like to make stuff.
ASME IX, AWS 17.1, D1.1
Instagram #RNHFAB
ASME IX, AWS 17.1, D1.1
Instagram #RNHFAB
Hey Rick,
While we are on the topic, how many amps are you running on the pipe, and what is your gas flow on the purge?
Do you use a foot pedal or just a switch?
I started using a foot pedal, and was getting used to it, but had a frame job recently and didn't want to drag the pedal around so went back to torch switch. Seemed to weld better with the switch so thinking I ditch it for SS jobs....I'll throw up some pictures while I'm at it.
While we are on the topic, how many amps are you running on the pipe, and what is your gas flow on the purge?
Do you use a foot pedal or just a switch?
I started using a foot pedal, and was getting used to it, but had a frame job recently and didn't want to drag the pedal around so went back to torch switch. Seemed to weld better with the switch so thinking I ditch it for SS jobs....I'll throw up some pictures while I'm at it.
- IMG_5430.JPG (29.81 KiB) Viewed 1893 times
- IMG_5427.JPG (33.42 KiB) Viewed 1893 times
- IMG_5401.JPG (32.05 KiB) Viewed 1893 times
- MosquitoMoto
-
Weldmonger
-
Posts:
-
Joined:Sat Aug 01, 2015 8:38 am
-
Location:The Land Down Under
Maker -maker of things wrote:Mine is down right hideous but it is cutting the grass. Fixed MTD mower pot metal rear axle for a co-worker. Oil and dirt saturated, couldn't clean half of the areas to be welded. 4043 filler with 5% pure tungsten added (by me).MosquitoMoto wrote: Not pretty, but it works.IMG_20160610_125723486.jpgIMG_20160610_125744946.jpg
In my experience - and often to my surprise - when I fix something for someone, especially when it's done as a favour, they often don't give a damn what it looks like, they're just happy it's fixed.
Haven't tried pot metal yet, heard it can be a nightmare. Well done on the axle.
Kym
Nice stuff! In those pics I'm running 60amps, 2.5pps, 50% on, 50% background (my Master 150sth doesnt allow me to change), back purge on first joints 15cfh, then I'm down to 5cfh by last joint, 25cfh with CK jumbo gas saver, 1/16" tung. When I don't pulse I run 45-50amps. I run a wireless foot pedal and most times I throw it into 2T so it just acts a on and off with a downslope to prevent craters...or I just slowly taper off.nortical wrote:Hey Rick,
While we are on the topic, how many amps are you running on the pipe, and what is your gas flow on the purge?
Do you use a foot pedal or just a switch?
I started using a foot pedal, and was getting used to it, but had a frame job recently and didn't want to drag the pedal around so went back to torch switch. Seemed to weld better with the switch so thinking I ditch it for SS jobs....I'll throw up some pictures while I'm at it.
IMG_5430.JPGIMG_5427.JPGIMG_5401.JPG
Your frame looks good, with round corner tubing I typically put the heat slightly towards the round corner and dab across to grab the other edge, my .100" shown above I ran 85amps, 3/32" tung #8 Superior cup.
I weld stainless, stainless and more stainless...Food Industry, sanitary process piping, vessels, whatever is needed, I like to make stuff.
ASME IX, AWS 17.1, D1.1
Instagram #RNHFAB
ASME IX, AWS 17.1, D1.1
Instagram #RNHFAB
- maker of things
-
Guide
-
Posts:
-
Joined:Tue Jul 19, 2016 6:52 am
Agreed. When given the choice of spending $250 for a used replacement or buying me lunch, unsurprisingly I end up getting lunch.MosquitoMoto wrote: In my experience - and often to my surprise - when I fix something for someone, especially when it's done as a favour, they often don't give a damn what it looks like, they're just happy it's fixed.
And if you never do, be happy. To call the process of fixing something like that "welding" is probably an injustice to the term. If one were to fully disassemble fully clean, fixture and attempt proper welding sure wouldn't be a lunch hour fix.MosquitoMoto wrote:Haven't tried pot metal yet, heard it can be a nightmare.
-Jon
I learned how to weld at night, but not last night. (despite how my weld looks)
Lincoln Viking 3350 K3034-2&3
Dynasty 210DX w/cps and coolmate3
Lincoln Power Mig 180c
hermit.shed on instagram
I learned how to weld at night, but not last night. (despite how my weld looks)
Lincoln Viking 3350 K3034-2&3
Dynasty 210DX w/cps and coolmate3
Lincoln Power Mig 180c
hermit.shed on instagram
New process piping ran from the tank to the existing manifold, sight glass guard fabbed...all ready.
- Attachments
-
- IMG_20160818_222124680.jpg (87.37 KiB) Viewed 1771 times
-
- IMG_20160818_222145322.jpg (52.41 KiB) Viewed 1771 times
-
- IMG_20160818_222134478.jpg (96.92 KiB) Viewed 1771 times
I weld stainless, stainless and more stainless...Food Industry, sanitary process piping, vessels, whatever is needed, I like to make stuff.
ASME IX, AWS 17.1, D1.1
Instagram #RNHFAB
ASME IX, AWS 17.1, D1.1
Instagram #RNHFAB
Had to chop out this inappropriate and under sized (1") ammonia pump bypass regulator and weld in a proper 1-1/2" regulator. Advised of sizing in advance so I welded some stubs onto flanges to save shutdown time.
When I got to the job I found the 1-1/2" pipe was actually an 1-1/2" x 1-1/4" reducer on both sides that were originally stick welded which meant I had to cut the reducers back to fully remove the stick welds. The reducers were now on the slope which meant alignment clamping became exciting. The left hand weld was frustrated by the proximity of vessels and pipes which tested my skills. Half way through the root I lost gas and crapped the weld. Took my helmet off to find an electrician spectator standing on my hose. After a brief discussion with the bolt neck concerning his family heritage he moved on. Ground out the joint and started again. Right hand joint was uneventful. Yay.
- PV1.jpg (47.61 KiB) Viewed 2010 times
- PV2.jpg (40.98 KiB) Viewed 2010 times
- PV3.jpg (67.16 KiB) Viewed 2010 times
Flat out like a lizard drinkin'
Every weld associated with this accumulator looked like crap. Done by a butcher. Couldn't take the risk of welding on inclusions and porosity. The welding position was hard enough without welding over someone else's crap. Just look at what he did: 1-1'4" pipe, welded on an 1-1/2" reducer, then another reducer to take it down to 1" and then put the wrong valve in. That bloke was a slice short of a sandwich.
Flat out like a lizard drinkin'
Seen some crazy stuff like that before. Random stuff thrown togeather to try to make something work. When in reality it never worked right and now you get to do it over. Set aside all the saftey issues of working with pumped liquid ammonia.
I have more questions than answers
Josh
Josh
exnailpounder
- exnailpounder
-
Weldmonger
-
Posts:
-
Joined:Thu Dec 25, 2014 9:25 am
-
Location:near Chicago
Looks good! I was showing my son how to tig and he moved in to look and stood on the hose. Felt pretty foolish toasting a tungsten with him looking while I'm bragging about how good I am 

Ifyoucantellmewhatthissaysiwillbuyyouabeer.
Return to “Tig Welding - Tig Welding Aluminum - Tig Welding Techniques - Aluminum Tig Welding”
Jump to
- Introductions & How to Use the Forum
- ↳ Welcome!
- ↳ Member Introductions
- ↳ How to Use the Forum
- ↳ Moderator Applications
- Welding Discussion
- ↳ Metal Cutting
- ↳ Tig Welding - Tig Welding Aluminum - Tig Welding Techniques - Aluminum Tig Welding
- ↳ Mig and Flux Core - gas metal arc welding & flux cored arc welding
- ↳ Stick Welding/Arc Welding - Shielded Metal Arc Welding
- ↳ Welding Forum General Shop Talk
- ↳ Welding Certification - Stick/Arc Welding, Tig Welding, Mig Welding Certification tests - Welding Tests of all kinds
- ↳ Welding Projects - Welding project Ideas - Welding project plans
- ↳ Product Reviews
- ↳ Fuel Gas Heating
- Welding Tips & Tricks
- ↳ Video Discussion
- ↳ Wish List
- Announcements & Feedback
- ↳ Forum News
- ↳ Suggestions, Feedback and Support
- Welding Marketplace
- ↳ Welding Jobs - Industrial Welding Jobs - Pipe Welding Jobs - Tig Welding Jobs
- ↳ Classifieds - Buy, Sell, Trade Used Welding Equipment
- Welding Resources
- ↳ Tradeshows, Seminars and Events
- ↳ The Welding Library
- ↳ Education Opportunities