I've been trying to weld some stainless steel exhaust pipe (ebay brand) with 316L rod, but I think something is wrong with my settings, technique, or torch setup because all my welds look like crap


Prep: Stainless Steel Brush on surfaces w/ acetone + paper towel cleaning.
Tungsten: 2% lanthanated (3/32 size), sharpened to a point
Amps: 40 (also tried pulsed @ 40/20)
Gas: 100% Argon
Torch: Air cooled Everlast
Torch Flow: ~7-8 L/min
Back Purge: ~2.2 L/min through the pipe
Tungsten protruding distance from #7 EverLast cup = 4.32 mm
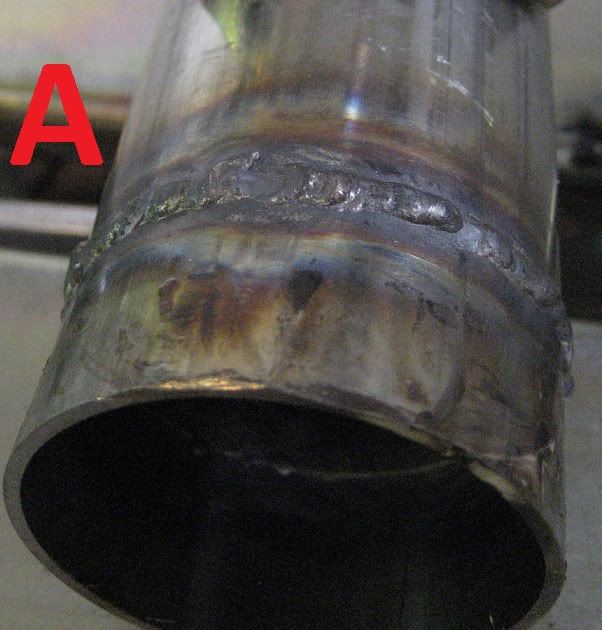
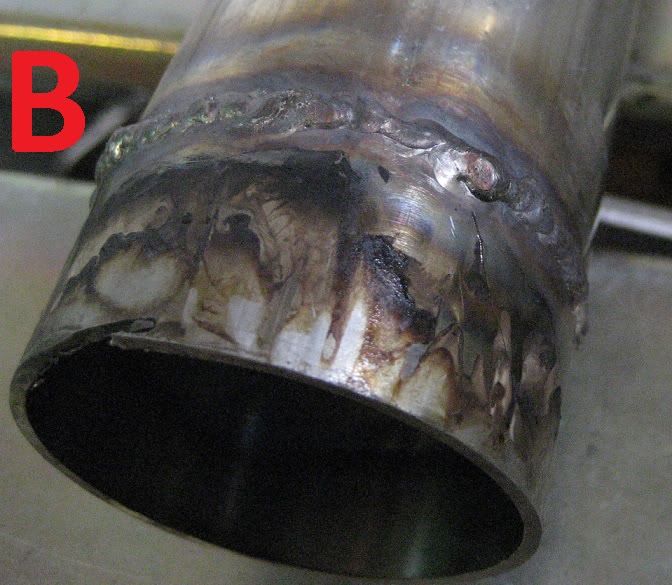
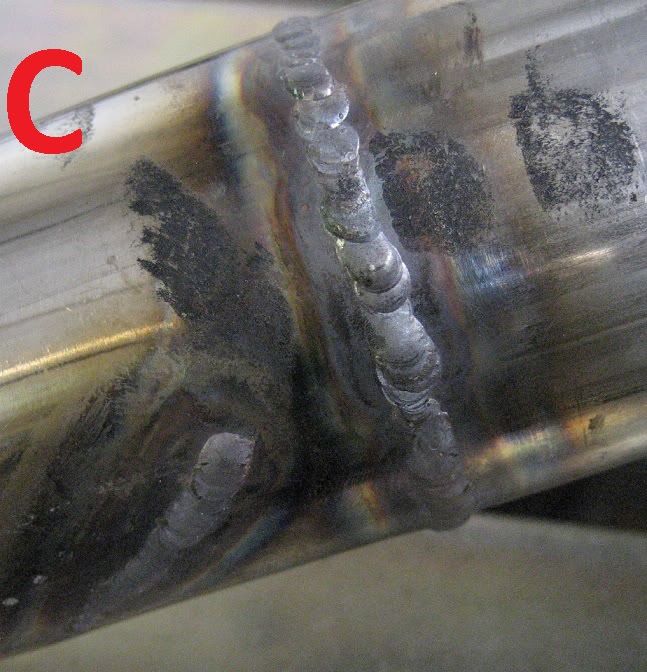
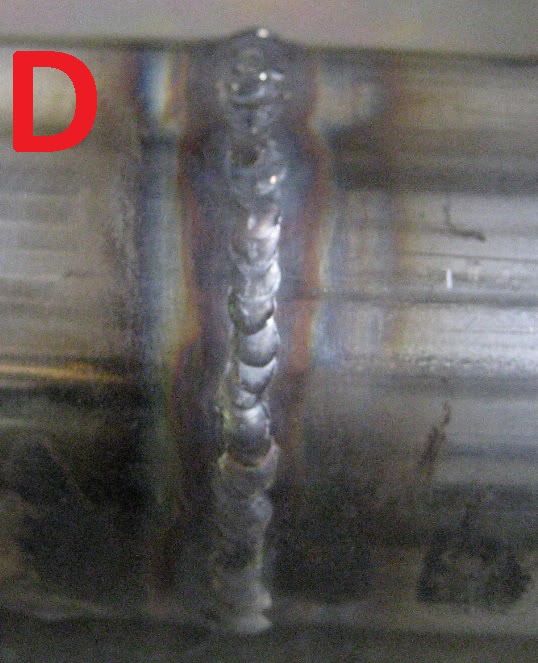
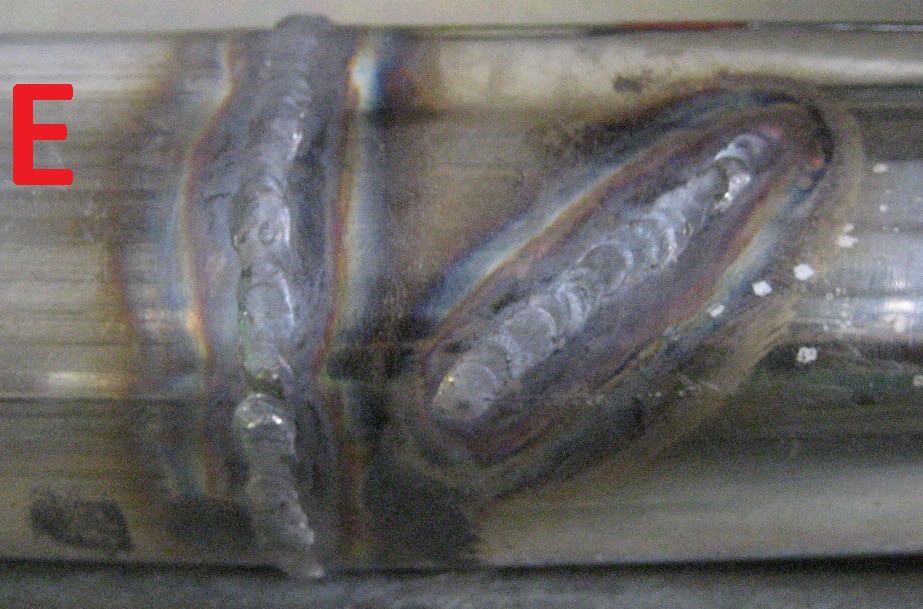
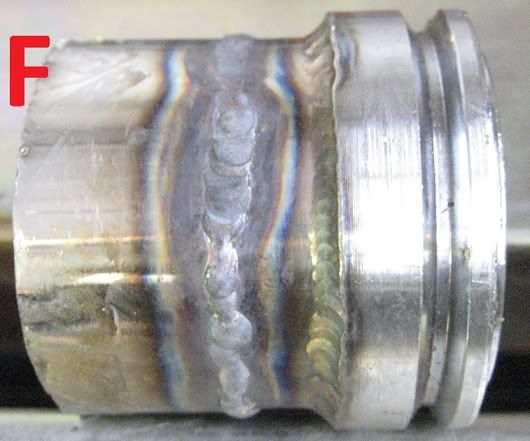
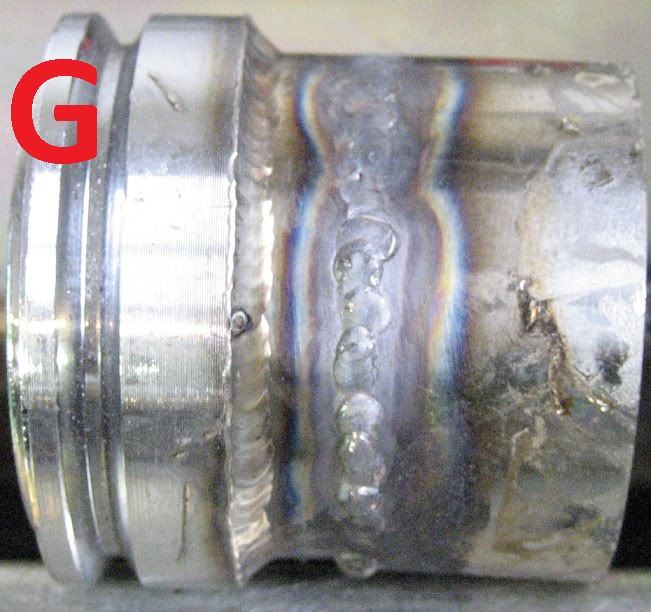
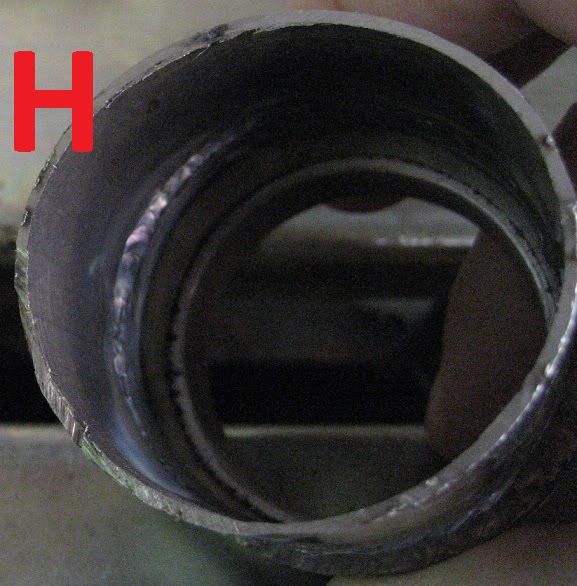