Tig welding tips, questions, equipment, applications, instructions, techniques, tig welding machines, troubleshooting tig welding process
Reading on other posts suggests going hotter than the 1A/.001 rule; let it shine quickly and then outrun the heat. But I just can't seem to get the initial puddle right. Should I be hotter or colder to get it started?
First off have you tried to tig on steel, and if so does it give a clean, shiny puddle using the 1A/1-thou rule? If not, you may have a shielding gas issue.
If yes, then you need to use more amperage. Lo' and behold. 16ga.
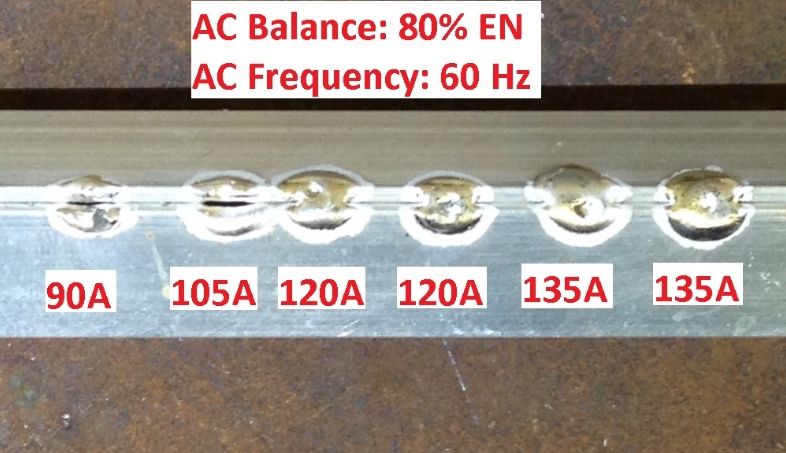
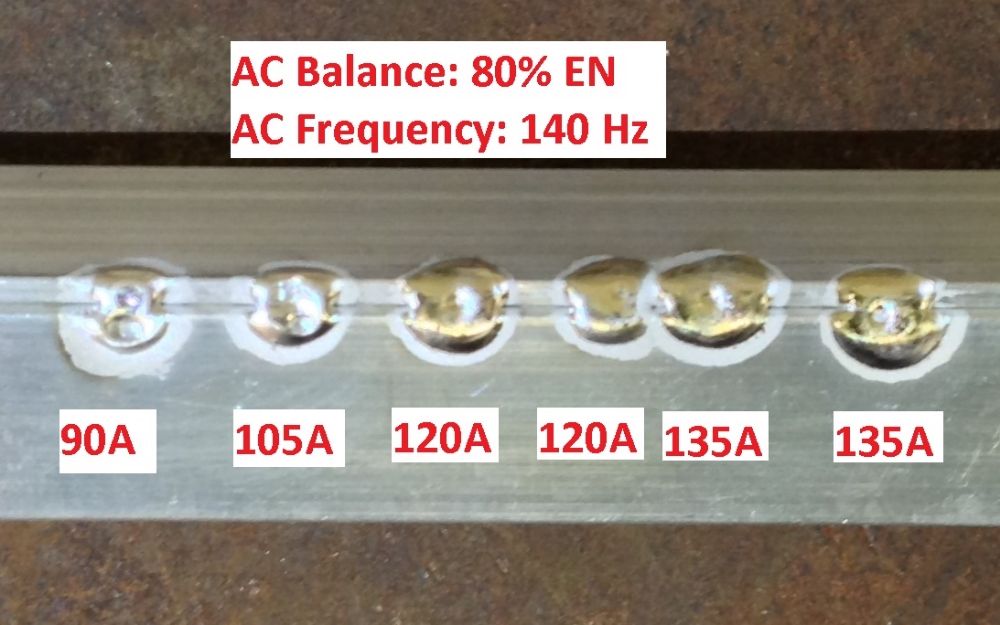
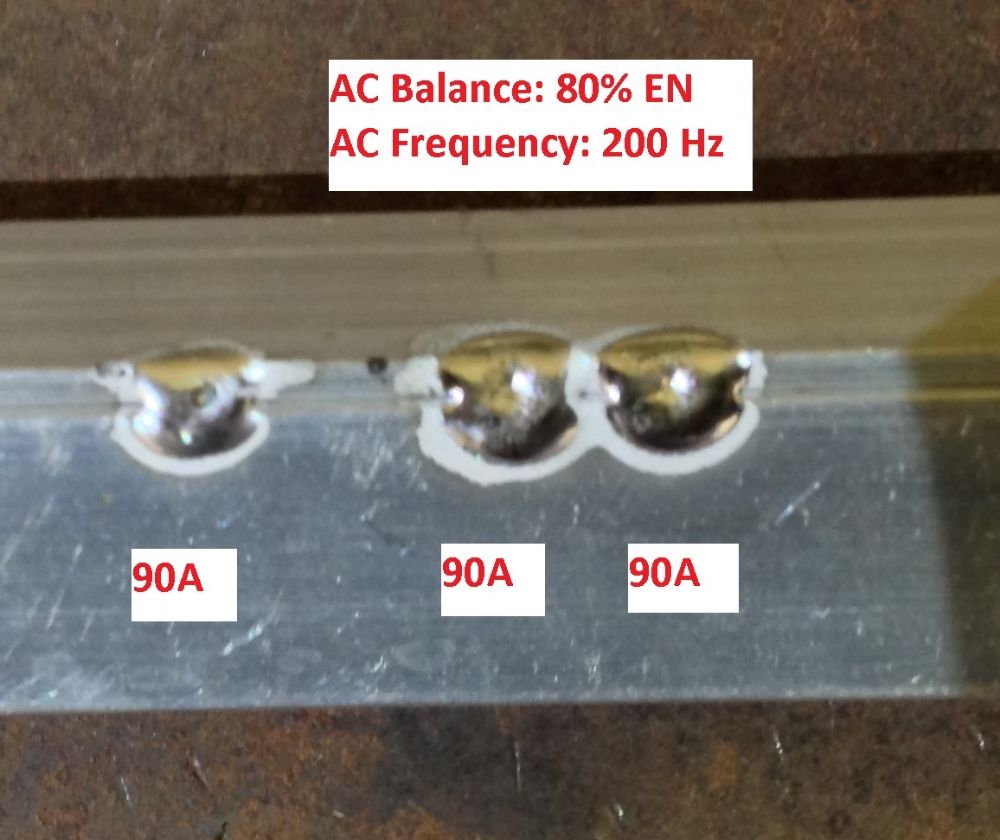
14ga is thicker than 16ga obviously, so the answer should be obvious.
If yes, then you need to use more amperage. Lo' and behold. 16ga.
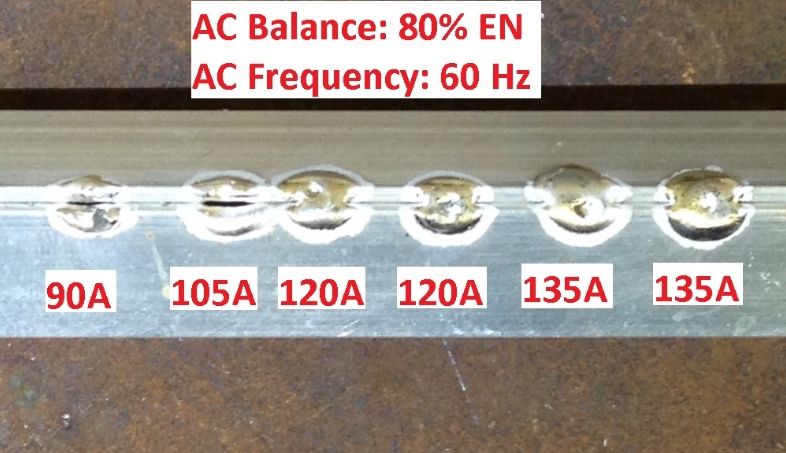
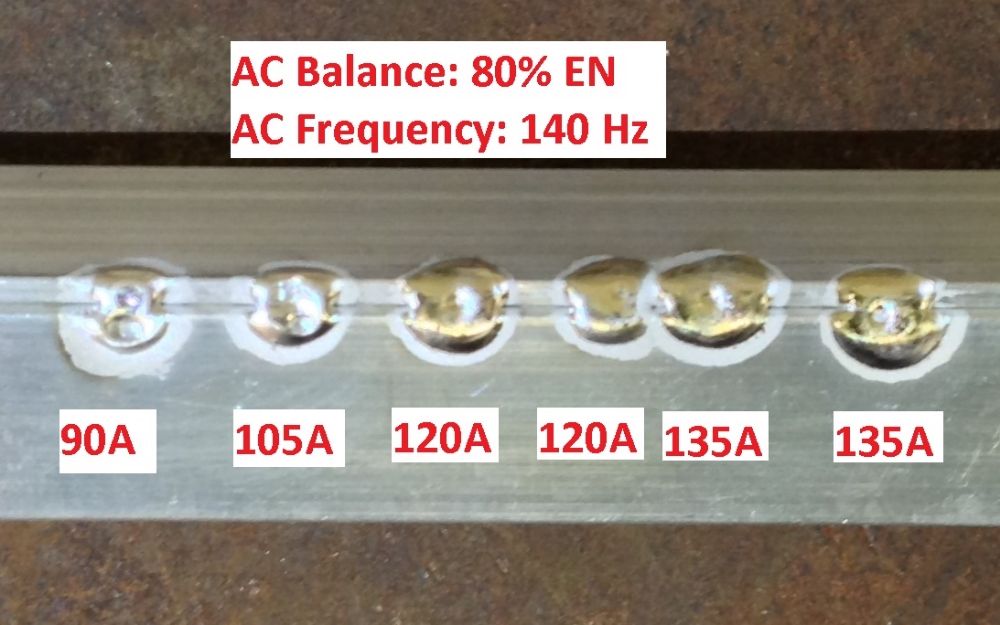
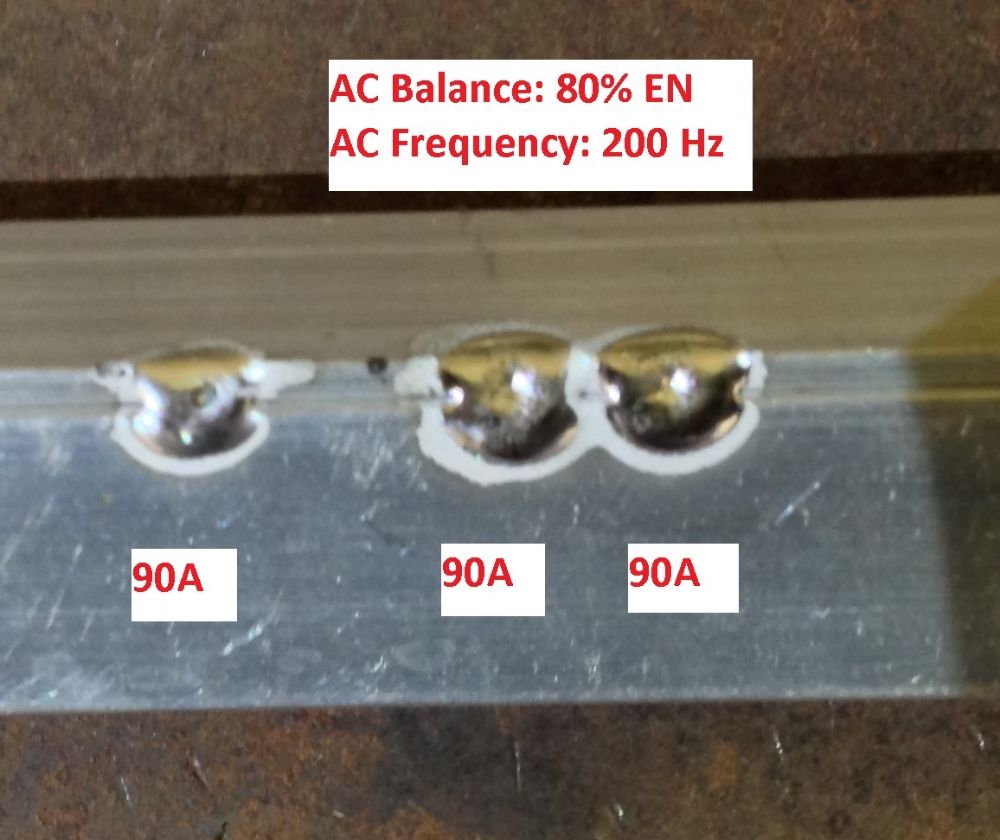
14ga is thicker than 16ga obviously, so the answer should be obvious.

The pic looks like a gas flow problem to me. I know it's obvious but most (all?) of us have forgotten to turn the gas on at some point. Hope this helps.
Cheers.
-Eldon
Cheers.
-Eldon
We are not lawyers nor physicians, but welders do it in all positions!
Miller Dynasty 280DX
Lincoln 210 MP
Miller 625 X-Treme
Hobart Handler 150
Victor Oxygen-acetylene torch
Miller/Lincoln Big 40-SA200 hybrid
Miller Dynasty 280DX
Lincoln 210 MP
Miller 625 X-Treme
Hobart Handler 150
Victor Oxygen-acetylene torch
Miller/Lincoln Big 40-SA200 hybrid
- AKweldshop
-
Weldmonger
-
Posts:
-
Joined:Wed Oct 23, 2013 3:30 pm
-
Location:Palmer AK
Are you sure your on AC?
Just a couple welders and a couple of big hammers and torches.
Men in dirty jeans built this country, while men in clean suits have destroyed it.
Trump/Carson 2016-2024
Men in dirty jeans built this country, while men in clean suits have destroyed it.
Trump/Carson 2016-2024
Well, I just got back to the plate. Still can't get it to do right. I increased the CFH to 20; I had only been using 15 with the gas lens thinking that was enough. Didn't seem to change much. In the pic in the lower "bead", I started at 125A, and could never get the "shiny face" so I just finally tried to outrun the heat across without adding any filler (going from right to left). I then waited only a half minute or so (plate was still hot) and lowered to 90A. This is the horizontal weld across right above the first. Still couldn't get initial weld "shiny", so I started going across and just left the wire in the puddle as I ran across.
Turned it over to DC and used 165A on a piece of 1/8 steel plate and it is the normal feel and weld. I should also say I have welded a couple of small aluminum pieces of trim together (using the pulse function rule of 33) and that came out reasonably nice. I'm just struggling starting on this plate.
Turned it over to DC and used 165A on a piece of 1/8 steel plate and it is the normal feel and weld. I should also say I have welded a couple of small aluminum pieces of trim together (using the pulse function rule of 33) and that came out reasonably nice. I'm just struggling starting on this plate.
- more weld pics.jpg (67.1 KiB) Viewed 2228 times
newschoppafowah
- newschoppafowah
-
Workhorse
-
Posts:
-
Joined:Wed Feb 19, 2014 11:54 pm
I hate to be the simplest things guy, but are you sure exactly what alloy that alum is?
If you're not fighting a breeze outdoors, 15cfh of pure argon should be enough, through a lens.
I'm not trying to be condescending, just throwin' out ideas.
When I first tried to weld alum, I had gotten some weird alloy from a metal supplier who's since (for other numerous and varied reasons) fallen out of favor with me, and it was just weird stuff. I didn't know what I didn't know, so to speak, and struggled for a good long while.
Whatever the deal is, good luck and stay with it. Once you get aluminum, a lot of other things begin to make sense in a cascading sort of way.
If you're not fighting a breeze outdoors, 15cfh of pure argon should be enough, through a lens.
I'm not trying to be condescending, just throwin' out ideas.
When I first tried to weld alum, I had gotten some weird alloy from a metal supplier who's since (for other numerous and varied reasons) fallen out of favor with me, and it was just weird stuff. I didn't know what I didn't know, so to speak, and struggled for a good long while.
Whatever the deal is, good luck and stay with it. Once you get aluminum, a lot of other things begin to make sense in a cascading sort of way.

Sent from an earthen ditch outside Needles, CA using an awful lot of low voltage single strand wire.
It's a matter of flour and water and then there's the seasonings, which is a matter of salt and so forth and then you h-we interrupt this for the announc
It's a matter of flour and water and then there's the seasonings, which is a matter of salt and so forth and then you h-we interrupt this for the announc
exnailpounder
- exnailpounder
-
Weldmonger
-
Posts:
-
Joined:Thu Dec 25, 2014 9:25 am
-
Location:near Chicago
My 2 cts...It looks like that piece is badly crapped up as well. Can see you tried to clean it but it looks to have deeply ingrained staining. I have a small plate like it that was in a scrap pile and it won't weld for s%$t. Try some brand new shiny stuff.
Ifyoucantellmewhatthissaysiwillbuyyouabeer.
- alum plate.jpg (63.82 KiB) Viewed 2169 times
perhaps try some different high frequency AC settings , may need more cleaning action, make sure you have adequate gas flow, pure Argon
Try 190 amps,speed of torch movent to control puddle or foot pedal if using one
short arc, tip of filler needs to stay in gas shield envelope,torch angle
same old basics
Try 190 amps,speed of torch movent to control puddle or foot pedal if using one
short arc, tip of filler needs to stay in gas shield envelope,torch angle
same old basics
Everlast 250EX
Miller 250 syncrowave
Sharp LMV Vertical Mill
Takisawa TSL-800-D Lathe
Coupla Bandsaws,Grinders,surface grinder,tool/cutter grinder
and more stuff than I deserve(Thanks Significant Other)
Miller 250 syncrowave
Sharp LMV Vertical Mill
Takisawa TSL-800-D Lathe
Coupla Bandsaws,Grinders,surface grinder,tool/cutter grinder
and more stuff than I deserve(Thanks Significant Other)
exnailpounder
- exnailpounder
-
Weldmonger
-
Posts:
-
Joined:Thu Dec 25, 2014 9:25 am
-
Location:near Chicago
If my eyes don't fail me...I don't see any clean zone in that weld bead. That weld is an improvement over the others you tried but that piece of plate is still all crapped up to the point that acetone and a wire brush won't clean it. You can't weld through contamination on aluminum. Maybe try a flap disc to grind past that dirty stuff and get bright clean metal...use a wheel just for aluminum though or it will load and stop cutting and grinder wheels can load up so bad they will shatter.
Ifyoucantellmewhatthissaysiwillbuyyouabeer.
You're still not where you need to be. There is MASSIVE contamination going on, but since we can't see you actually run the bead, we can't be 100% sure where it is coming from. What I think you should do is start from the beginning. Get a nice clean piece of weldable aluminum alloy (junk pile aluminum does not guarantee weldability), and see if you can get just a SINGLE clean puddle. Not even a short bead, one single PUDDLE. It should be clean shiny, with a white etched zone around it, with absolutely NO black impurities. If you cannot attain this then there is no point in even continuing trying to run even the shortest bead because there is an underlying problem that you need to address. Remember that for aluminum you need about 1.5 - 2A per thousandths of material thickness in order to not heat soak the material and cause even further issues.
- Braehill
-
Weldmonger
-
Posts:
-
Joined:Sat Jul 06, 2013 11:16 am
-
Location:Near Pittsburgh,Pennsylvania. Steel Buckle of the Rust Belt
Oscar,
You're saying I would need 560-750 amps to weld 3/8" (1.5-2A per.001)Aluminum? Somebody better tell my old 310 amp Dialarc HF
Len.
You're saying I would need 560-750 amps to weld 3/8" (1.5-2A per.001)Aluminum? Somebody better tell my old 310 amp Dialarc HF
Len.
Now go melt something.
Instagram @lenny_gforce
Len
Instagram @lenny_gforce
Len
- Braehill
-
Weldmonger
-
Posts:
-
Joined:Sat Jul 06, 2013 11:16 am
-
Location:Near Pittsburgh,Pennsylvania. Steel Buckle of the Rust Belt
Craig,
I had to take some temps about 40' up earlier and out of curiosity I shot the handrail with the temp gun and it read minus 6*F, so 750 amps would be on the menu here also.
Len
I had to take some temps about 40' up earlier and out of curiosity I shot the handrail with the temp gun and it read minus 6*F, so 750 amps would be on the menu here also.
Len
Last edited by Braehill on Sat Feb 21, 2015 9:22 am, edited 1 time in total.
Now go melt something.
Instagram @lenny_gforce
Len
Instagram @lenny_gforce
Len
exnailpounder
- exnailpounder
-
Weldmonger
-
Posts:
-
Joined:Thu Dec 25, 2014 9:25 am
-
Location:near Chicago
Goldhawg...I finally got a chance to play with aluminum with my brand new Syncrowave 210. Sorry for the crappy pix but I use a tablet and its all she will do....1/4" 6061 wiped with acetone and brushed. 175 amps ,75% balance, 3/32" ceriated tungsten, 4043 filler rod, gas lens, #7 cup 20cfh. I set my balance at the Pro set and did other welds at different settings. I think the etching zone is too large at the pro set but I need more time to play. Never used an inverter but it beats my transformer hands down on aluminum. My tungsten was pretty balled by the time I did these beads hence the wide etch.
- Attachments
-
- 20150220_182952-2.jpg (40.15 KiB) Viewed 1408 times
Ifyoucantellmewhatthissaysiwillbuyyouabeer.
- Superiorwelding
-
Weldmonger
-
Posts:
-
Joined:Thu Jan 24, 2013 10:13 pm
-
Location:Eddy, TX
exnailpounder,
Those beads look great. I see consistancy and you can weld in a straight line, better than me at times
Keep plying with it and post up your results.
-Jonathan
Those beads look great. I see consistancy and you can weld in a straight line, better than me at times

-Jonathan
Instagram- @superiorwelding/@learntotig
Twitter- @_JonathanLewis
https://www.learntotig.com
https://www.superiorweldandfab.com
https://www.youtube.com/+SuperiorWeldin ... ATHANLEWIS
Twitter- @_JonathanLewis
https://www.learntotig.com
https://www.superiorweldandfab.com
https://www.youtube.com/+SuperiorWeldin ... ATHANLEWIS
exnailpounder
- exnailpounder
-
Weldmonger
-
Posts:
-
Joined:Thu Dec 25, 2014 9:25 am
-
Location:near Chicago
Hey thanks Jonathan. I have gotten to use my new 210 for a total of about an hour last night and of course I had to try everything. I am stumped as to why the OP is having so much trouble as I find the 210 to be a really good alum welder. I didn't post pics to brag but to show him I have the same machine and gave my settings and hopefully help him out. I worked a long day today so I could play with my new toy all day tommorow. You know that the only difference between men and boys is the price of their toys 

Ifyoucantellmewhatthissaysiwillbuyyouabeer.
- weldin mike 27
-
Weldmonger
-
Posts:
-
Joined:Fri Apr 01, 2011 10:59 pm
-
Location:Australia; Victoria
exnailpounder
- exnailpounder
-
Weldmonger
-
Posts:
-
Joined:Thu Dec 25, 2014 9:25 am
-
Location:near Chicago
I hear ya. I'm 52 going on 12. My wife bought me an a Wicked Lasers Arctic laser that will light matches and burn skin...the first thing I did was take it to the bar and burn holes in the potato chip bags and plastic cups. I can't go back there til May WTFweldin mike 27 wrote:By that last statement, I should be about 12yo

Ifyoucantellmewhatthissaysiwillbuyyouabeer.
- weldin mike 27
-
Weldmonger
-
Posts:
-
Joined:Fri Apr 01, 2011 10:59 pm
-
Location:Australia; Victoria
exnailpounder
- exnailpounder
-
Weldmonger
-
Posts:
-
Joined:Thu Dec 25, 2014 9:25 am
-
Location:near Chicago
Damned if I know Mick..We use lasers in the refineries to point out valves and such to build scaffold to but those are cat toys. It never gets old when my dog goes to her bowl and I give her a little goosw in the dirt hole with that bad boy 

Ifyoucantellmewhatthissaysiwillbuyyouabeer.
GreinTime
- GreinTime
-
Weldmonger
-
Posts:
-
Joined:Fri Nov 01, 2013 11:20 am
-
Location:Pittsburgh, PA
I just exploded in laughter at work at that image lolexnailpounder wrote:Damned if I know Mick..We use lasers in the refineries to point out valves and such to build scaffold to but those are cat toys. It never gets old when my dog goes to her bowl and I give her a little goosw in the dirt hole with that bad boy
#oneleggedproblems
-=Sam=-
-=Sam=-
exnailpounder
- exnailpounder
-
Weldmonger
-
Posts:
-
Joined:Thu Dec 25, 2014 9:25 am
-
Location:near Chicago
Grein.... Its funny to watch her "tuck it in" when she gets it. It doesn't burn from a distance but it stings a bit. Its even funnier to point it at the deer that come through my yard. They chase the beam and run from it and follow it around...hours of fun. I don't know how I get anything done around here
I wish I knew what Iwant to be when I grow up!

Ifyoucantellmewhatthissaysiwillbuyyouabeer.
This reminds of something that happened 10 years ago.exnailpounder wrote:Damned if I know Mick..We use lasers in the refineries to point out valves and such to build scaffold to but those are cat toys. It never gets old when my dog goes to her bowl and I give her a little goosw in the dirt hole with that bad boy
I get called to this refinery to inspect a repair they made on some line.
The guy responsible to issue the permit is a total wanker and I know him from previous experience. He always tried to pass the responsibility on you by enforcing every PPE he could think of, regardless of whether they were required or even possible to use. I mean the guy wanted to you to wear a safety harness inside a distilling tower which is impossible. So in case there was an accident, he could claim it was your fault for not following directions.
So after I wait for him for more than 1 hour to write the permit and him forcing every conceivable PPE known to man, we go to the unit to show me where the repair is.
He points at a bend 20-25m high where there is absolutely no access (afterwards I learned that the guys that did the repair used a basket with a crane to reach it).
I say I am sorry I can't see where the repair is from here.
He starts describing the area "it is 6m on the right of that 10" plug valve etc"
I go "I am sorry , still can't see it. Come up with me and show me."
He goes " How am I going to get up there?"
Then I go " THEN HOW THE F*CK DO YOU WANT ME TO GET UP THERE? "
Needless to say they called a crane with a lifting basket for me to do the inspection.
Return to “Tig Welding - Tig Welding Aluminum - Tig Welding Techniques - Aluminum Tig Welding”
Jump to
- Introductions & How to Use the Forum
- ↳ Welcome!
- ↳ Member Introductions
- ↳ How to Use the Forum
- ↳ Moderator Applications
- Welding Discussion
- ↳ Metal Cutting
- ↳ Tig Welding - Tig Welding Aluminum - Tig Welding Techniques - Aluminum Tig Welding
- ↳ Mig and Flux Core - gas metal arc welding & flux cored arc welding
- ↳ Stick Welding/Arc Welding - Shielded Metal Arc Welding
- ↳ Welding Forum General Shop Talk
- ↳ Welding Certification - Stick/Arc Welding, Tig Welding, Mig Welding Certification tests - Welding Tests of all kinds
- ↳ Welding Projects - Welding project Ideas - Welding project plans
- ↳ Product Reviews
- ↳ Fuel Gas Heating
- Welding Tips & Tricks
- ↳ Video Discussion
- ↳ Wish List
- Announcements & Feedback
- ↳ Forum News
- ↳ Suggestions, Feedback and Support
- Welding Marketplace
- ↳ Welding Jobs - Industrial Welding Jobs - Pipe Welding Jobs - Tig Welding Jobs
- ↳ Classifieds - Buy, Sell, Trade Used Welding Equipment
- Welding Resources
- ↳ Tradeshows, Seminars and Events
- ↳ The Welding Library
- ↳ Education Opportunities