I am somewhat satisfied with my welds on my aluminum and stainless, I know they arent perfect but they are getting there. What I Hate is my mild steel welds. Ive just never been happy with them. Im enclosing some pics. Staimless, aluminum amd Mild steel. Its the mild steel Id like help with. Beads are matt grey, irregular and dont have that nice stacked dime look. The pic is 1/8", amps are 120, but I have a foot pedal so Im not running it that high (after I get the puddle, I back off) ,gas lense, 3/32" 2* thoriated tungsten, 12 fpm argon, 3/16" ER70S2 rod. mill scale removed
Fire Away
Tig welding tips, questions, equipment, applications, instructions, techniques, tig welding machines, troubleshooting tig welding process
- TRACKRANGER
-
Weldmonger
-
Posts:
-
Joined:Wed Aug 06, 2014 12:48 am
-
Location:Melbourne, Australia
Tom,
That looks too cold to me, as though you've backed off too much.
Try this: Set the machine to 80 Amps, DCEN. Then weld with the pedal fully down.
I would recommend a 3mm gap, tack each end to stop the gap pulling. Run about 10-14 L/min Argon (~ 20-28 cf/h).
Have you got any 3/32" filler rod available instead? That might help also.
Also, you mentioned "12 fpm argon" presumably that is not 12 cubic foot/minute? Can you check that value again?
HTH
Trevor
That looks too cold to me, as though you've backed off too much.
Try this: Set the machine to 80 Amps, DCEN. Then weld with the pedal fully down.
I would recommend a 3mm gap, tack each end to stop the gap pulling. Run about 10-14 L/min Argon (~ 20-28 cf/h).
Have you got any 3/32" filler rod available instead? That might help also.
Also, you mentioned "12 fpm argon" presumably that is not 12 cubic foot/minute? Can you check that value again?
HTH
Trevor
EWM Phonenix 355 Pulse MIG set mainly for Aluminum, CIGWeld 300Amp AC/DC TIG, TRANSMIG S3C 300 Amp MIG, etc, etc
noddybrian
- noddybrian
-
Weldmonger
-
Posts:
-
Joined:Thu Jan 24, 2013 12:13 pm
Welcome to the forum Tom.
If your just getting started with Tig I'd say your welds look great - just more seat time may improve it - but there really is nothing wrong there at all - the obvious difference is that an outside corner & fillet require a fair amount of filler - the steel though is a butt joint with no edge prep or root gap - the arc can only provide so much penetration unless using massive amps so the filler has nowhere to go except as build up - the size rod you have is creating a fast cooling effect on the pool & probably more build up in one pass than you like - so as previously mentioned try a thinner filler rod & use either a root gap or put a bevel on the plates.
If your just getting started with Tig I'd say your welds look great - just more seat time may improve it - but there really is nothing wrong there at all - the obvious difference is that an outside corner & fillet require a fair amount of filler - the steel though is a butt joint with no edge prep or root gap - the arc can only provide so much penetration unless using massive amps so the filler has nowhere to go except as build up - the size rod you have is creating a fast cooling effect on the pool & probably more build up in one pass than you like - so as previously mentioned try a thinner filler rod & use either a root gap or put a bevel on the plates.
butt weld
use 3/32 rod( too much rod chilling puddle too quick)
more amps
torch angle more towards 15*
less cfh argon , 17-20,puddle is chilling too soon, get a deep beveled puddle and then up travel speed,big rod dips not dabs
alum just more seat time
SS too cool for my type of welding
gas flow will affect weld puddle temp
welders need to be their own critique, last person to see the weld,is usally the welder
At my elder age every weld is a new adventure.
use 3/32 rod( too much rod chilling puddle too quick)
more amps
torch angle more towards 15*
less cfh argon , 17-20,puddle is chilling too soon, get a deep beveled puddle and then up travel speed,big rod dips not dabs
alum just more seat time
SS too cool for my type of welding
gas flow will affect weld puddle temp
welders need to be their own critique, last person to see the weld,is usally the welder
At my elder age every weld is a new adventure.
Last edited by rick9345 on Tue Aug 26, 2014 8:37 am, edited 2 times in total.
Everlast 250EX
Miller 250 syncrowave
Sharp LMV Vertical Mill
Takisawa TSL-800-D Lathe
Coupla Bandsaws,Grinders,surface grinder,tool/cutter grinder
and more stuff than I deserve(Thanks Significant Other)
Miller 250 syncrowave
Sharp LMV Vertical Mill
Takisawa TSL-800-D Lathe
Coupla Bandsaws,Grinders,surface grinder,tool/cutter grinder
and more stuff than I deserve(Thanks Significant Other)
- Braehill
-
Weldmonger
-
Posts:
-
Joined:Sat Jul 06, 2013 11:16 am
-
Location:Near Pittsburgh,Pennsylvania. Steel Buckle of the Rust Belt
Tom,
It's clear that you have a couple values misrepresented here. You stated that you're using 12 cubic feet a 'minute', and that should be 12 cubic feet an 'hour', no biggie, happens all the time. You also state that your using 3/16 filler on 1/8 plate, not likely, it's probably 1/16 or 3/32, again no biggie.
Something that most people fail to realize when welding Carbon steel is the fact that the steel is magnetic and that effects the puddle. It takes some seat time to master steel and some attention to how the puddle reacts to the magnetic field. A small weave goes a long way while welding mild steel. You're doing just fine, and I wouldn't try too hard for the stack of dimes look on steel. It's not really the best feature in a Carbon steel weld, it leaves too many stress risers in my opinion.
Len
It's clear that you have a couple values misrepresented here. You stated that you're using 12 cubic feet a 'minute', and that should be 12 cubic feet an 'hour', no biggie, happens all the time. You also state that your using 3/16 filler on 1/8 plate, not likely, it's probably 1/16 or 3/32, again no biggie.
Something that most people fail to realize when welding Carbon steel is the fact that the steel is magnetic and that effects the puddle. It takes some seat time to master steel and some attention to how the puddle reacts to the magnetic field. A small weave goes a long way while welding mild steel. You're doing just fine, and I wouldn't try too hard for the stack of dimes look on steel. It's not really the best feature in a Carbon steel weld, it leaves too many stress risers in my opinion.
Len
Now go melt something.
Instagram @lenny_gforce
Len
Instagram @lenny_gforce
Len
Sorry guys,, Im using 3/32" rod, not 3/16... typo there. I have noticed the magnetic effect, rod seems to want to stick if I do more than just touch the leading edge of the puddle. I will try some of your suggestions and we will see how it goes. I just like neat and pretty. Otherwise I would just push a mig over it. lol
Breahill is right on
attention to how the puddle reacts to the magnetic field. A small weave goes a long way while welding mild steel. You're doing just fine,
good grounds ,close to weld, not just flopped on table, I have a small jumper cable hooked to table that can clamp to work,close to weld for good arc incitation
attention to how the puddle reacts to the magnetic field. A small weave goes a long way while welding mild steel. You're doing just fine,
good grounds ,close to weld, not just flopped on table, I have a small jumper cable hooked to table that can clamp to work,close to weld for good arc incitation
Everlast 250EX
Miller 250 syncrowave
Sharp LMV Vertical Mill
Takisawa TSL-800-D Lathe
Coupla Bandsaws,Grinders,surface grinder,tool/cutter grinder
and more stuff than I deserve(Thanks Significant Other)
Miller 250 syncrowave
Sharp LMV Vertical Mill
Takisawa TSL-800-D Lathe
Coupla Bandsaws,Grinders,surface grinder,tool/cutter grinder
and more stuff than I deserve(Thanks Significant Other)
- TRACKRANGER
-
Weldmonger
-
Posts:
-
Joined:Wed Aug 06, 2014 12:48 am
-
Location:Melbourne, Australia
Hi TomTomVogel wrote:I have noticed the magnetic effect, rod seems to want to stick if I do more than just touch the leading edge of the puddle...
The sticking is probably not related to anything magnetic, I suggest it's the filler 'freezing' in the puddle, probably because of not enough heat.
My rule of thumb for butt-welding 1/8" plate is 80 Amps and 3mm gap, 3/32" filler rod, maybe with a backing plate if possible, otherwise reduce the gap and use a vee joint as suggested also above by Noddy. The 3/32" filler rod is perfect for that size joint.
Check your gas flow again, but I think it must have been a typo.
Hope this helps, but let us know the outcome if possible
Cheers
Trevor
EWM Phonenix 355 Pulse MIG set mainly for Aluminum, CIGWeld 300Amp AC/DC TIG, TRANSMIG S3C 300 Amp MIG, etc, etc
Hi Tom
My rule of thumb for butt-welding 1/8" plate is 80 Amps and 3mm gap, 3/32" filler rod, maybe with a backing plate if possible, otherwise reduce the gap and use a vee joint as suggested also above by Noddy. The 3/32" filler rod is perfect for that size joint.
Cheers
Trevor[/quote]
Hi Trevor;
Do you mean .3 (three tenths) mm? 3mm is the thickness of the metal pretty much... right?
. Thanks, Tom
My rule of thumb for butt-welding 1/8" plate is 80 Amps and 3mm gap, 3/32" filler rod, maybe with a backing plate if possible, otherwise reduce the gap and use a vee joint as suggested also above by Noddy. The 3/32" filler rod is perfect for that size joint.
Cheers
Trevor[/quote]
Hi Trevor;
Do you mean .3 (three tenths) mm? 3mm is the thickness of the metal pretty much... right?
. Thanks, Tom
All I've ever done is mild steel so take my advice for what it's worth...
I agree with above that the rod sticking to the puddle is a combination of welding too low amps with too large a filler rod.
I would use 3/32" on my 1/8" fillet welds but would floor the peddle and weld pretty fast and hot.
Here's one I did tonight messing around with 1.125" x 0.065" tube to .125" plate.
100 amps, 1/8" 2% lanth, 1/16" rod
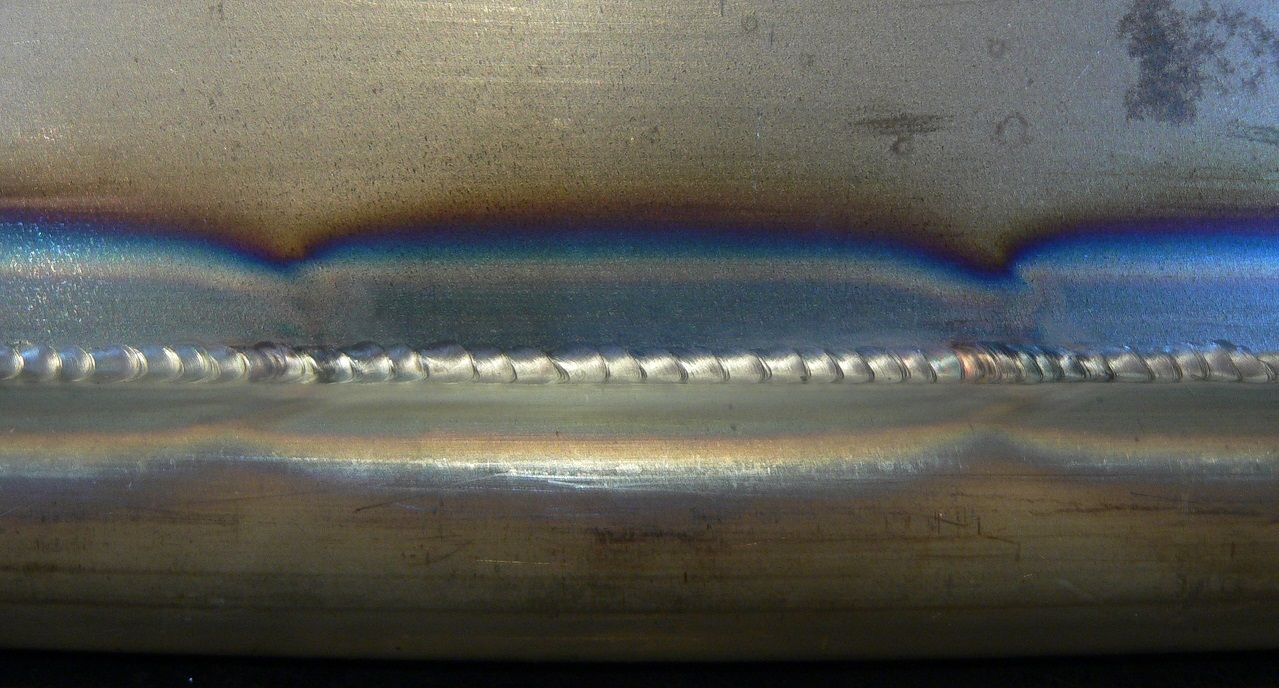
Lap joints followed by fillet joints, to me, seem to be the easiest joints to get the heat dialed in right. Then from there tackle the butt and outside corner.
I agree with above that the rod sticking to the puddle is a combination of welding too low amps with too large a filler rod.
I would use 3/32" on my 1/8" fillet welds but would floor the peddle and weld pretty fast and hot.
Here's one I did tonight messing around with 1.125" x 0.065" tube to .125" plate.
100 amps, 1/8" 2% lanth, 1/16" rod
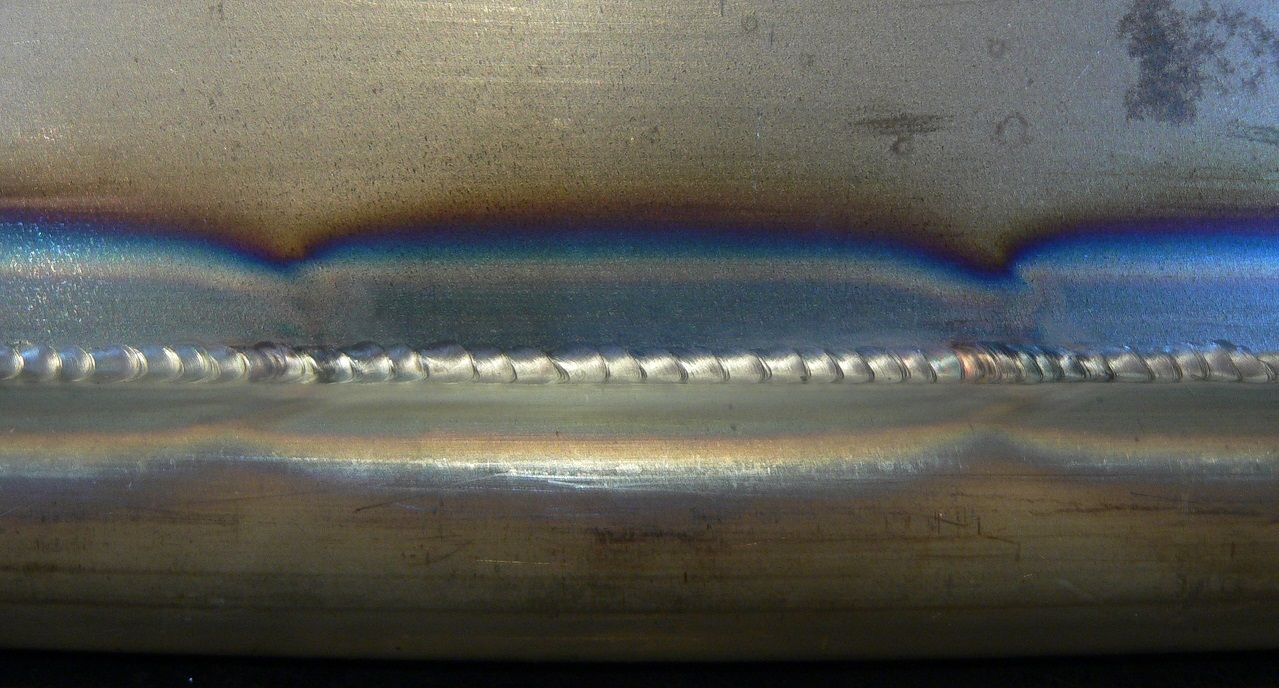
Lap joints followed by fillet joints, to me, seem to be the easiest joints to get the heat dialed in right. Then from there tackle the butt and outside corner.
Ok! I'm not expert by any means. I'm still trying to figure out tig. I've learned a lot by trial and error, and Jody's videos. The aluminum weld in the first picture looks pretty good for a noob. You kind of rushed it at the end. Ruined the spacing on the ripples. The T-joint looks like you started cold, then at the end you were too hot. Watch your puddle, and adjust your travel speed, and /or amps.
The butt weld looks like you were running to cold. And you were doing what my buddy calls "drunk driving"! Do some dry runs where you can follow the joint without getting in a bind, or getting into an uncomfortable position. It doesn't matter good the weld looks, if you don't follow the joint!
If your machine has pulse, try a low speed pulse to train you hands to get into the habit of speed and feed. 1 pps or less works great when I am training myself!
The butt weld looks like you were running to cold. And you were doing what my buddy calls "drunk driving"! Do some dry runs where you can follow the joint without getting in a bind, or getting into an uncomfortable position. It doesn't matter good the weld looks, if you don't follow the joint!
If your machine has pulse, try a low speed pulse to train you hands to get into the habit of speed and feed. 1 pps or less works great when I am training myself!
- TRACKRANGER
-
Weldmonger
-
Posts:
-
Joined:Wed Aug 06, 2014 12:48 am
-
Location:Melbourne, Australia
Hi Trevor;TomVogel wrote:Hi Tom
My rule of thumb for butt-welding 1/8" plate is 80 Amps and 3mm gap, 3/32" filler rod, maybe with a backing plate if possible, otherwise reduce the gap and use a vee joint as suggested also above by Noddy. The 3/32" filler rod is perfect for that size joint.
Cheers
Trevor
Do you mean .3 (three tenths) mm? 3mm is the thickness of the metal pretty much... right?
. Thanks, Tom[/quote]
Hi Tom
Yes, I mean 3 millimeters (call it 1/8")
Yes, the gap for 1/8" plate should be about the same thickness as the parent metal.
The gap is not your problem though, get some more heat into it. 80Amps (maybe slightly higher) with 3/32" filler rod should put you in the ball-park.
For butt welding with small gauge material, use the filler rod as a guide for the material gap. If you use 3/32" filler rod, have a 3/32" gap in the plates - it's a good starting point. Also, use a backing plate (e.g. copper)
It looks like you're close, I think more amps is your best first adjustment.
Cheers
Trevor
EWM Phonenix 355 Pulse MIG set mainly for Aluminum, CIGWeld 300Amp AC/DC TIG, TRANSMIG S3C 300 Amp MIG, etc, etc
forrestderp
- forrestderp
-
Workhorse
-
Posts:
-
Joined:Tue Nov 26, 2013 2:51 am
-
Location:Saint Cloud/Duluth MN
If you can just use your foot peddle as a switch, your rod hand has much more effect on your bead than your torch hand. Just start padding beads and be very critical of the effects from your input, and once you get it down without a peddle the puddle will feel like cheat mode.
Sean
Sean
Return to “Tig Welding - Tig Welding Aluminum - Tig Welding Techniques - Aluminum Tig Welding”
Jump to
- Introductions & How to Use the Forum
- ↳ Welcome!
- ↳ Member Introductions
- ↳ How to Use the Forum
- ↳ Moderator Applications
- Welding Discussion
- ↳ Metal Cutting
- ↳ Tig Welding - Tig Welding Aluminum - Tig Welding Techniques - Aluminum Tig Welding
- ↳ Mig and Flux Core - gas metal arc welding & flux cored arc welding
- ↳ Stick Welding/Arc Welding - Shielded Metal Arc Welding
- ↳ Welding Forum General Shop Talk
- ↳ Welding Certification - Stick/Arc Welding, Tig Welding, Mig Welding Certification tests - Welding Tests of all kinds
- ↳ Welding Projects - Welding project Ideas - Welding project plans
- ↳ Product Reviews
- ↳ Fuel Gas Heating
- Welding Tips & Tricks
- ↳ Video Discussion
- ↳ Wish List
- Announcements & Feedback
- ↳ Forum News
- ↳ Suggestions, Feedback and Support
- Welding Marketplace
- ↳ Welding Jobs - Industrial Welding Jobs - Pipe Welding Jobs - Tig Welding Jobs
- ↳ Classifieds - Buy, Sell, Trade Used Welding Equipment
- Welding Resources
- ↳ Tradeshows, Seminars and Events
- ↳ The Welding Library
- ↳ Education Opportunities