
Started by removing the inside weld seam in a couple of square tubing pieces:
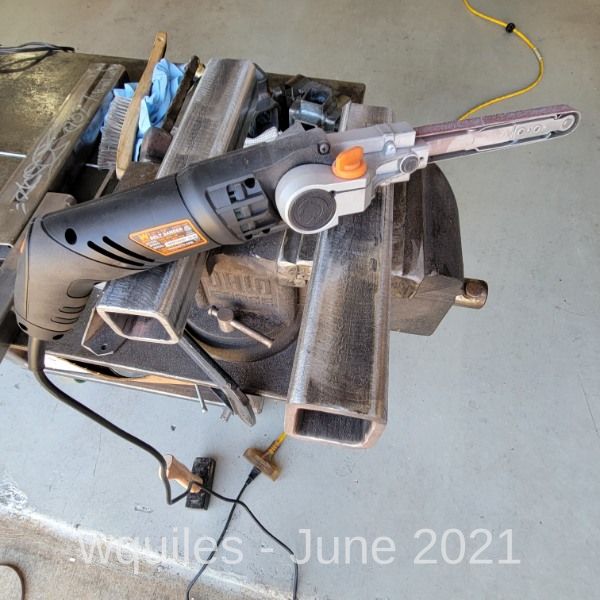
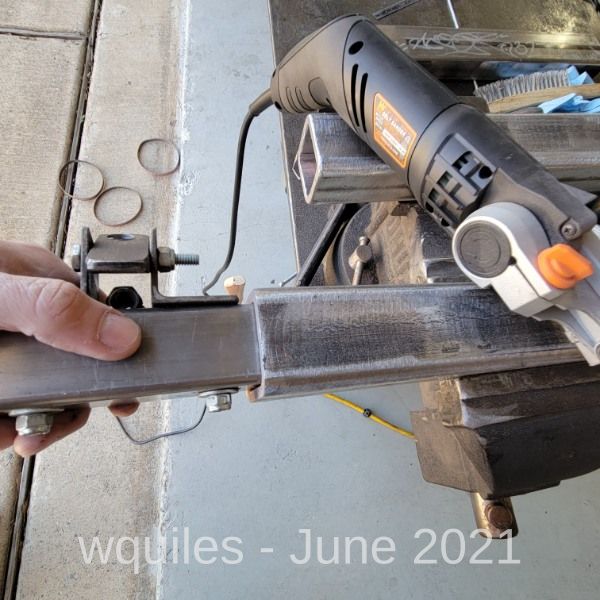
Although I did make most everything from scratch, I did buy the "C" bracket assembly from Origin Blade Maker. Since it is my own design, I have no plans - I adjusted as I went along. Here I am clamping everything to get an idea of spacing, length, etc..
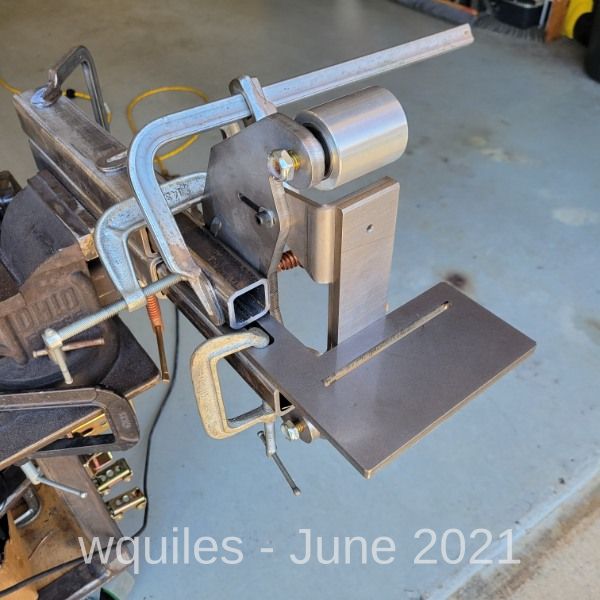
Cut and milled the top arm, and even made some delrin spacers for a slight press fit:
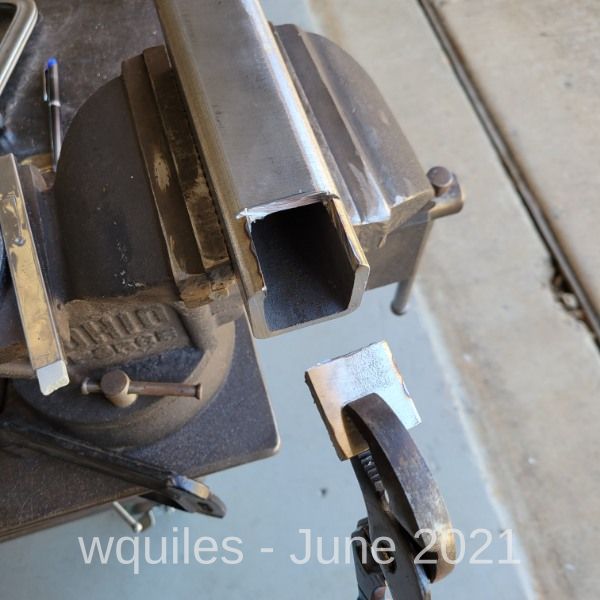

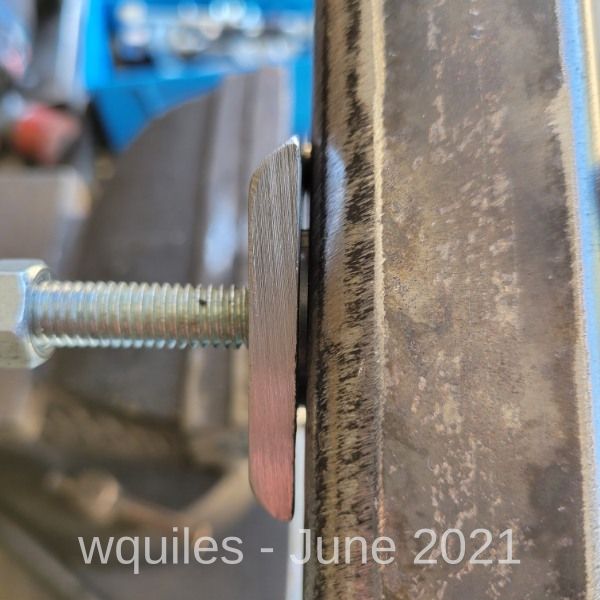
This is the mockup (clamped in early April) - nothing welded yet:
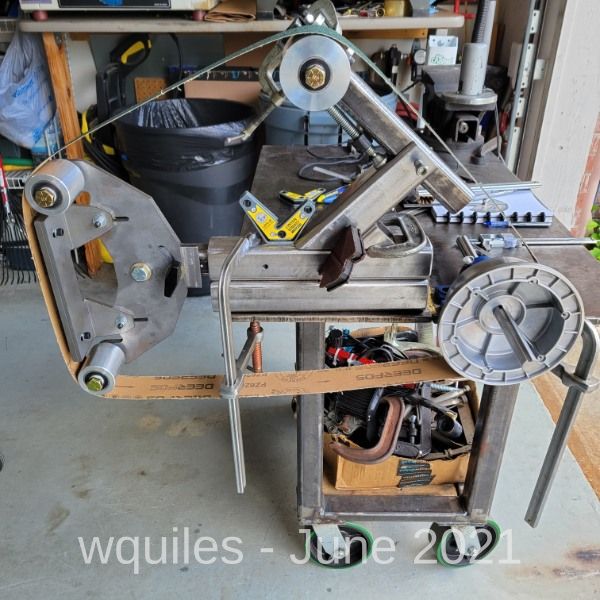
Once I figured the spacing to get all wheels aligned, I started welding - 100% with my new to me HTP 201 water-cooled Tig Machine:
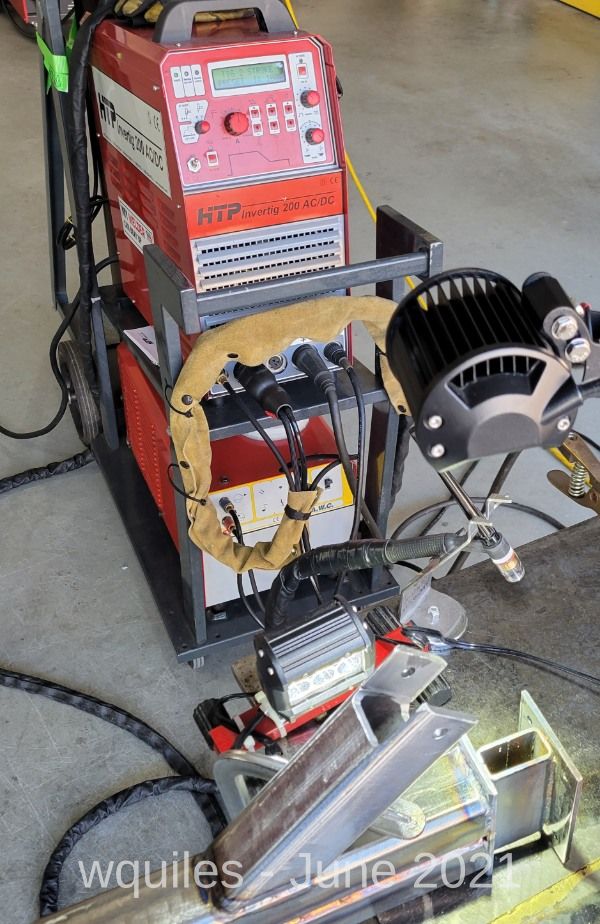