Working with 2 different gas lens setups, doing a lap weld on 1/8" mild steel coupons with 1/16 filler, 1/16 tungsten, and about 130 amps:
[*]CK 17 series torch
[*]CK 4 series stubby gas lens (#4GL116) with a #8 screw-on cup. About 1/2" of stickout.
[*]CK 3 series large diamater #18 pyrex. About 1" of stickout.
I just can't get shiny/colored welds out of the #8 cup no matter what I do, even doing really small beads that are within the cup the entire time. I've tried 25cfh, 15cfh, and 8cfh. All give pretty much the same result although the puddle dances around a fair bit more at 25cfh than 8cfh.
I switch over to the #18 cup at 25cfh and get beautiful beads with exactly-as-expected straw-to-blue color depending on the temperature.
Am I doing something wrong? Are stubby gas lenses just not as good as short or regular gas lenses in shielding? Am I still getting solid welds but it's just cosmetic?
(some of these #18 welds are more "stacked" then I would like...my tungsten was a bit contaminated and I didn't want to regrind it)
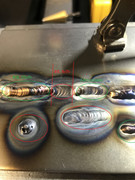