Could use some help! My flat, horizontal, and even overhead welds are pretty decent. The more I practice, the better they get. Not so with vertical uphill with 7018. I have watched plenty of videos, I've emulated what I see (CLAMS) over and over and my results still look like a hemorrhoidal nightmare. Gloopy, runny, sags of metal everywhere. The videos all stress going slow. The slower I go the worse things get. I've tried varying rod angle, amperage, travel speed. I keep a tight arc. Oddly enough, when I try going downhill (I've heard this isn't supposed to work with 7018) the welds look a lot better. But I want to do it right. Please enlighten me about what I need to change to get some good looking flat welds. Here are some photos of a plate I tried to string up.
Stick Welding Tips, Certification tests, machines, projects
- MinnesotaDave
-
Weldmonger
-
Posts:
-
Joined:Sun Oct 27, 2013 10:57 pm
-
Location:Big Lake/Monticello MN, U.S.A.
Arbitrarily "going slow" didn't work for you with the other positions right?
Your speed is dictated by what you see happening, nothing more.
Keep it simple - make a puddle, keep going up at a variable rate that maintains the puddle.
When done, analyze the bead you made and determine what to change. Only change 1 thing at a time.
90 rod angle, don't point the tip up.
Your speed is dictated by what you see happening, nothing more.
Keep it simple - make a puddle, keep going up at a variable rate that maintains the puddle.
When done, analyze the bead you made and determine what to change. Only change 1 thing at a time.
90 rod angle, don't point the tip up.
Dave J.
Beware of false knowledge; it is more dangerous than ignorance. ~George Bernard Shaw~
Syncro 350
Invertec v250-s
Thermal Arc 161 and 300
MM210
Dialarc
Tried being normal once, didn't take....I think it was a Tuesday.
Beware of false knowledge; it is more dangerous than ignorance. ~George Bernard Shaw~
Syncro 350
Invertec v250-s
Thermal Arc 161 and 300
MM210
Dialarc
Tried being normal once, didn't take....I think it was a Tuesday.
Steve S.
- Steve S.
-
New Member
-
Posts:
-
Joined:Sat May 06, 2017 5:45 am
-
Location:Salt Lake City, Utah
I was running 1/8" 7018 at 120 amps. dcep
I tried rod angles from 90 to slight upward push angle
I tried amperage as low as 90 amps up to 135, but mostly 120
I varied travel speed from what I've seen people doing (in so many videos) to so fast it was ridiculous.
oddly enough when I worked it downhill, I got good results.
I tried rod angles from 90 to slight upward push angle
I tried amperage as low as 90 amps up to 135, but mostly 120
I varied travel speed from what I've seen people doing (in so many videos) to so fast it was ridiculous.
oddly enough when I worked it downhill, I got good results.
- MinnesotaDave
-
Weldmonger
-
Posts:
-
Joined:Sun Oct 27, 2013 10:57 pm
-
Location:Big Lake/Monticello MN, U.S.A.
Vertical down 7018 is incorrect.
Keep practicing, change one variable at a time.
I prefer 120-130 amps for stringers vertical up, 1/8" 7018.
Weaves I may run lower depending on steel thickness.
Keep reducing amps until you get a puddle that is too cold, then increase as you are able to control it.
You dial my not be accurate.
This is a good vertical video - there are many more good ones by him too.
http://welding-tv.com/2016/11/08/stick- ... -vertical/
Keep practicing, change one variable at a time.
I prefer 120-130 amps for stringers vertical up, 1/8" 7018.
Weaves I may run lower depending on steel thickness.
Keep reducing amps until you get a puddle that is too cold, then increase as you are able to control it.
You dial my not be accurate.
This is a good vertical video - there are many more good ones by him too.

http://welding-tv.com/2016/11/08/stick- ... -vertical/
Dave J.
Beware of false knowledge; it is more dangerous than ignorance. ~George Bernard Shaw~
Syncro 350
Invertec v250-s
Thermal Arc 161 and 300
MM210
Dialarc
Tried being normal once, didn't take....I think it was a Tuesday.
Beware of false knowledge; it is more dangerous than ignorance. ~George Bernard Shaw~
Syncro 350
Invertec v250-s
Thermal Arc 161 and 300
MM210
Dialarc
Tried being normal once, didn't take....I think it was a Tuesday.
I think too slow and too much amps (just a little), or and too long arc (or the rod in the puddle (?)MinnesotaDave wrote:Vertical down 7018 is incorrect.
Keep practicing, change one variable at a time.
I prefer 120-130 amps for stringers vertical up, 1/8" 7018.
Weaves I may run lower depending on steel thickness.
Keep reducing amps until you get a puddle that is too cold, then increase as you are able to control it.
You dial my not be accurate.
This is a good vertical video - there are many more good ones by him too.
http://welding-tv.com/2016/11/08/stick- ... -vertical/
Going up is always faster than I thought (particularily with a little waving) I had those sort of drops for a long time until I get to manage the puddle somehow and that induced way more speed up that I was using
When waving I can see the dark trace moving left right right left, too (with the adequate hood shade)
1 variable at a time is indeed a perfect method for improvments
Pianos , restorer and tuner
Dedicated to learn welding since april
slowly learning
not complaining of doing beads and beads
pro inverter PROGYS 200 FV PFC CEL+tig lift
OA Oxyflam 1000 cutting and welding gas torch
Dedicated to learn welding since april
slowly learning

pro inverter PROGYS 200 FV PFC CEL+tig lift
OA Oxyflam 1000 cutting and welding gas torch
Might be a little late but vertical 7018 is my preferred way to weld. If you haven’t yet possibly try practicing with 3/32 to get some control on vertical 7018 before moving to 1/8 rod. If that is not something you want to try then the best way I can describe it is almost like slowly painting left to right and watching as the puddle slowly crawls up under the rod. I keep a slight upward rod angle. keep the rod as close to the metal as possible without touching, and slowly move left pause for a second then move straight to the right and pause for a second while slowly moving upwards. A common mistake I made starting out was forgetting to breath and moving too fast. A tip that helped me was to count one onethousand move right one onethousand move left to get some consistency in my travel speed and slowed me down. Then slowly change your count to however long it takes for the puddle to fill in it may change depending on the metal being welded and the amount of heat you are using.
Why weaves may run lower ? I seem to discover quite the opposite, making small "hesitations" particularily if pausing in the root too, but then it does not rise as fast as with stringers indeed, but the 3 steps are not long spaced in time,when I could obtain that nice triangle without inclusions or undercuts, the motion was fluid, and with relatively short hesitations.MinnesotaDave wrote:Vertical down 7018 is incorrect.
Keep practicing, change one variable at a time.
I prefer 120-130 amps for stringers vertical up, 1/8" 7018.
Weaves I may run lower depending on steel thickness.
BTW it helped me as the motion is somewhat circular, it was easier to stay steady and to control it, than with a slower weave, for some unknown reason (may be I tend to hold the stringer too tight at some point, I need to doublecheck that.
Well "depending of thickness " may do all the difference
"puddle too cold" , how is it seen ? does it follow the rod too easily, or do not wash the sides correctly (or tend to stick ?)
As the heat accumulates I see 2 or 3 speeds along a vertical up , so counting is not always helping, it tend to keep you at the same pace.
Pianos , restorer and tuner
Dedicated to learn welding since april
slowly learning
not complaining of doing beads and beads
pro inverter PROGYS 200 FV PFC CEL+tig lift
OA Oxyflam 1000 cutting and welding gas torch
Dedicated to learn welding since april
slowly learning

pro inverter PROGYS 200 FV PFC CEL+tig lift
OA Oxyflam 1000 cutting and welding gas torch
- MinnesotaDave
-
Weldmonger
-
Posts:
-
Joined:Sun Oct 27, 2013 10:57 pm
-
Location:Big Lake/Monticello MN, U.S.A.
Weaves have a slower vertical progression than stringers so more heat gets concentrated in a small area.olek wrote:Why weaves may run lower ?MinnesotaDave wrote:Vertical down 7018 is incorrect.
Keep practicing, change one variable at a time.
I prefer 120-130 amps for stringers vertical up, 1/8" 7018.
Weaves I may run lower depending on steel thickness.
As a result, fewer amps may be used sometimes, depending on steel thickness.
For weaves and stringers I like to use enough amps for the puddle to wet out easily though - as a result I'm usually above 120 amps.
Dave J.
Beware of false knowledge; it is more dangerous than ignorance. ~George Bernard Shaw~
Syncro 350
Invertec v250-s
Thermal Arc 161 and 300
MM210
Dialarc
Tried being normal once, didn't take....I think it was a Tuesday.
Beware of false knowledge; it is more dangerous than ignorance. ~George Bernard Shaw~
Syncro 350
Invertec v250-s
Thermal Arc 161 and 300
MM210
Dialarc
Tried being normal once, didn't take....I think it was a Tuesday.
"wet out easily" is the sign that the process goes well is not it?MinnesotaDave wrote:Weaves have a slower vertical progression than stringers so more heat gets concentrated in a small area.olek wrote:Why weaves may run lower ?MinnesotaDave wrote:Vertical down 7018 is incorrect.
Keep practicing, change one variable at a time.
I prefer 120-130 amps for stringers vertical up, 1/8" 7018.
Weaves I may run lower depending on steel thickness.
As a result, fewer amps may be used sometimes, depending on steel thickness.
For weaves and stringers I like to use enough amps for the puddle to wet out easily though - as a result I'm usually above 120 amps.
Then I understand progression up is slower but if the wetting goes well, on the relatively thin steel I used up to now (maximum 6mm) it is soon time to move the wetting is instantaneous, it may be different with thicker base.
I probably would have experienced less trouble by using thick 10mm plates to work vertical up.
What worked for me is to remind how much to rise at each "turn" , the thickness of the rod, no more.
BTW is triangle or Christmas tree a progression used to make only one pass in a corner?
I was told to make a real triangle (circling) but have also seen welding left up right up (in the corner) is it also a "triangle" or a method used to cap? ....edit : I see, both are used, but the triangle should be preferably used with MIG I suppose, I could do it without inclusions but there is a risk . (the other is called "upside down V" by Jody)
[youtube]https://youtu.be/mxAHPJL_crU[/youtube]
Cheers , (that is what I call "fast " in the video, a little faster than what I do with the stick but no time to loose or all fall
down , is not it ?
her both techniques [youtube]https://youtu.be/lNe4fo6hxAQ[/youtube]
Pianos , restorer and tuner
Dedicated to learn welding since april
slowly learning
not complaining of doing beads and beads
pro inverter PROGYS 200 FV PFC CEL+tig lift
OA Oxyflam 1000 cutting and welding gas torch
Dedicated to learn welding since april
slowly learning

pro inverter PROGYS 200 FV PFC CEL+tig lift
OA Oxyflam 1000 cutting and welding gas torch
Mosrly I weld flat with 7018s but today I did some uphill as I was welding some square tubing together and man it was a disaster. I was probably at 100 amps with a 2.5mm rod (3/32nds) and the wall thickness was thinner on one side, 3mm or a little below 1/8" and it blew through that side. I eventually had to flip the part so I could weld it flat and repair the damage. I kept going down in amps as I welded until I hit 70 amps, but I never dared to try uphill welding again on this piece. I definitely need to train on this.
70 amps, I think maybe 75 could have worked too. The metal was getting pretty warm by this time so I guess this also has an effect on amperage. I have a hand held remote control for stick welding, but I would have to remove my TIG pedal to use it so I didn't. Think I should start using it though.
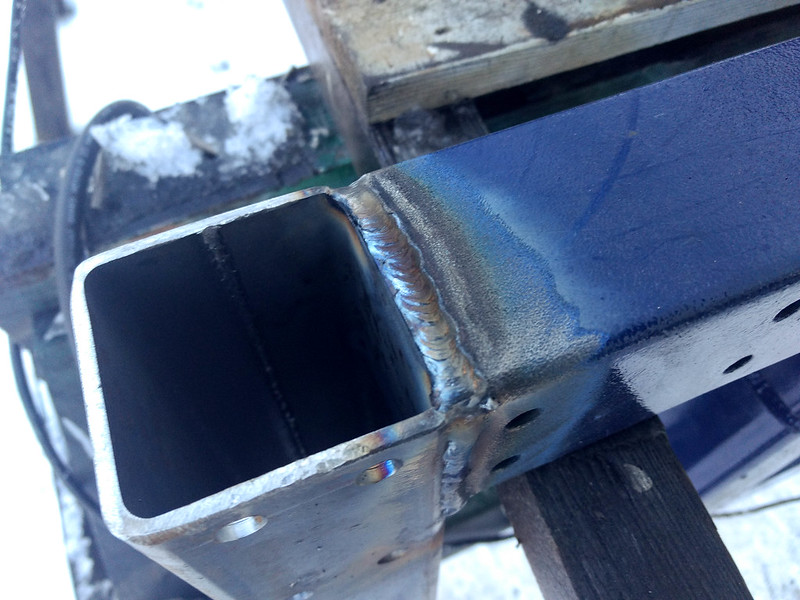
70 amps, I think maybe 75 could have worked too. The metal was getting pretty warm by this time so I guess this also has an effect on amperage. I have a hand held remote control for stick welding, but I would have to remove my TIG pedal to use it so I didn't. Think I should start using it though.
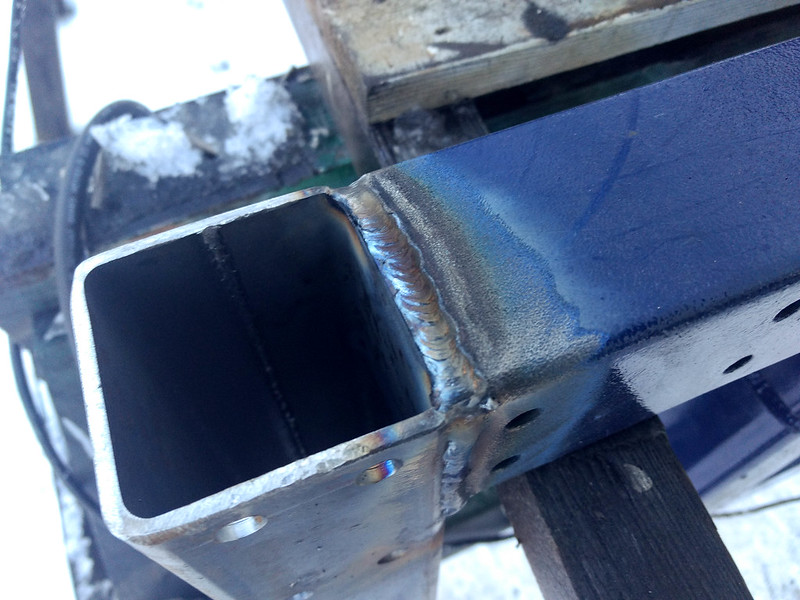
Vertical up puts more heat in the material. Heat rises and heats up the material above a lot quicker than when welding flat.
Welding the small gap at the rounded edge of the tubing makes it even more difficult.
I use 2mm (5/64) 7018 at 65-70 amps DCEP on 3mm tubing and if there is a small gap I use 2mm 7016 on 40-50 amps DCEN for the root sometimes followed by a second pas with 7018 on DCEP.
Welding 3mm tube with 2.5mm rods is not really a problem, but 2mm rods make it easier to control.
Eric
Welding the small gap at the rounded edge of the tubing makes it even more difficult.
I use 2mm (5/64) 7018 at 65-70 amps DCEP on 3mm tubing and if there is a small gap I use 2mm 7016 on 40-50 amps DCEN for the root sometimes followed by a second pas with 7018 on DCEP.
Welding 3mm tube with 2.5mm rods is not really a problem, but 2mm rods make it easier to control.
Eric
Vertical up with 3/32 7018 on 1/8” thick material is a challenge, especially if your inexperienced. Vertical up separates the men from the boys when stick welding with 7018.
If all I had for this job was 3/32 7018, I would run one pass vertical down. Then go vertical up the second pass. There’s nothing wrong with running 7018 vertical down as long as it’s done properly. This isn’t easy for a new welder neither. You might get it in without burning through this way.
Most new vertical up 7018 welders don’t understand that your stacking weld metal on itself. This builds a lot of heat as you work your way upwards. You need some meat for base metal to do this cleanly.
If all I had for this job was 3/32 7018, I would run one pass vertical down. Then go vertical up the second pass. There’s nothing wrong with running 7018 vertical down as long as it’s done properly. This isn’t easy for a new welder neither. You might get it in without burning through this way.
Most new vertical up 7018 welders don’t understand that your stacking weld metal on itself. This builds a lot of heat as you work your way upwards. You need some meat for base metal to do this cleanly.
On joints like that, I always put a large tack weld right at the spots that build up/accumulate heat, so when I actually get to it, it acts as a sponge to absorb the arc energy without obliterating the corner all to hell. When I get to that tack weld, there is so much heat alread that just running over the tack melts it out pretty quick and right when it does, I then break the arc.DennisCA wrote:Mosrly I weld flat with 7018s but today I did some uphill as I was welding some square tubing together and man it was a disaster. I was probably at 100 amps with a 2.5mm rod (3/32nds) and the wall thickness was thinner on one side, 3mm or a little below 1/8" and it blew through that side. I eventually had to flip the part so I could weld it flat and repair the damage. I kept going down in amps as I welded until I hit 70 amps, but I never dared to try uphill welding again on this piece. I definitely need to train on this.
70 amps, I think maybe 75 could have worked too. The metal was getting pretty warm by this time so I guess this also has an effect on amperage. I have a hand held remote control for stick welding, but I would have to remove my TIG pedal to use it so I didn't. Think I should start using it though.
I do the same on other joints, even in non vertical-up situations. Basically on all corners, whether it be part of flat plate/bar/angle/channel connecting to something else, or corners of tubing.
You say vertical up separates the men from the boys with 7018, but running 7018 vertical down is the next level.snoeproe wrote:Vertical up with 3/32 7018 on 1/8” thick material is a challenge, especially if your inexperienced. Vertical up separates the men from the boys when stick welding with 7018.
If all I had for this job was 3/32 7018, I would run one pass vertical down. Then go vertical up the second pass. There’s nothing wrong with running 7018 vertical down as long as it’s done properly. This isn’t easy for a new welder neither. You might get it in without burning through this way.
Most new vertical up 7018 welders don’t understand that your stacking weld metal on itself. This builds a lot of heat as you work your way upwards. You need some meat for base metal to do this cleanly.
I know it can be done, and I have done it, but it's not for a beginner. These rods are not made for downhill and You have to manipulate the rod so when the slag drops it will drop down the side instead of straight down the middle and mess up the puddle.
Why run vertical down if you can run vertical up?E T wrote:You say vertical up separates the men from the boys with 7018, but running 7018 vertical down is the next level.snoeproe wrote:Vertical up with 3/32 7018 on 1/8” thick material is a challenge, especially if your inexperienced. Vertical up separates the men from the boys when stick welding with 7018.
If all I had for this job was 3/32 7018, I would run one pass vertical down. Then go vertical up the second pass. There’s nothing wrong with running 7018 vertical down as long as it’s done properly. This isn’t easy for a new welder neither. You might get it in without burning through this way.
Most new vertical up 7018 welders don’t understand that your stacking weld metal on itself. This builds a lot of heat as you work your way upwards. You need some meat for base metal to do this cleanly.
I know it can be done, and I have done it, but it's not for a beginner. These rods are not made for downhill and You have to manipulate the rod so when the slag drops it will drop down the side instead of straight down the middle and mess up the puddle.
My thoughts exactly.Oscar wrote: Why run vertical down if you can run vertical up?
You can use it in pinch when the rods you have are to big for the material thickness your welding because you put less heat in the material welding downhill but 7018 is not really the rod for that.
It takes a lot of practice to get good at welding 7018 vertical down. Your better off using that time to pop out and get some 7018 in the right size and weld it vertical up. Or mayby some fast freeze 6012 on DCEN which are perfect for welding vertical down in thin stuff.
- MinnesotaDave
-
Weldmonger
-
Posts:
-
Joined:Sun Oct 27, 2013 10:57 pm
-
Location:Big Lake/Monticello MN, U.S.A.
I've found a quick pass vertical down with 6010 or 6011 seals up the piece with very little fuss.
A vertical up pass with 3/32" 7018 works fine after, if needed.
A vertical up pass with 3/32" 7018 works fine after, if needed.
Dave J.
Beware of false knowledge; it is more dangerous than ignorance. ~George Bernard Shaw~
Syncro 350
Invertec v250-s
Thermal Arc 161 and 300
MM210
Dialarc
Tried being normal once, didn't take....I think it was a Tuesday.
Beware of false knowledge; it is more dangerous than ignorance. ~George Bernard Shaw~
Syncro 350
Invertec v250-s
Thermal Arc 161 and 300
MM210
Dialarc
Tried being normal once, didn't take....I think it was a Tuesday.
Thin sheet metal can be a challenge welding vertical up. Even with a 3/32 rod. Closing up a gap can be a challenge running vertical up, even with 3/32 rod.Oscar wrote:Why run vertical down if you can run vertical up?E T wrote:You say vertical up separates the men from the boys with 7018, but running 7018 vertical down is the next level.snoeproe wrote:Vertical up with 3/32 7018 on 1/8” thick material is a challenge, especially if your inexperienced. Vertical up separates the men from the boys when stick welding with 7018.
If all I had for this job was 3/32 7018, I would run one pass vertical down. Then go vertical up the second pass. There’s nothing wrong with running 7018 vertical down as long as it’s done properly. This isn’t easy for a new welder neither. You might get it in without burning through this way.
Most new vertical up 7018 welders don’t understand that your stacking weld metal on itself. This builds a lot of heat as you work your way upwards. You need some meat for base metal to do this cleanly.
I know it can be done, and I have done it, but it's not for a beginner. These rods are not made for downhill and You have to manipulate the rod so when the slag drops it will drop down the side instead of straight down the middle and mess up the puddle.
Tmancannon
- Tmancannon
-
New Member
-
Posts:
-
Joined:Mon Mar 11, 2019 8:13 pm
I actually teach all the new guys when they come in the shop, I remember when I was learning, vertical up was the hardest and most discouraging. my suggestion is to use 1/8 rod 3/32 imo is harder to see whats actually happening, and realistically you need to learn 1/8 anyways.
Try tuning the machine on a flat plate first, you want to get the heat so the rod just stays lit with a tight arc, secondly you may have beast luck running a corner joint vertical up, flat plate will be more difficult, the corners help kind of catch the puddle so u can see it better.
Go straight in maybe even the slightest, and i do mean slight, rod angle up.
People say hold a tight arc, this messed me up for the longest time because if you hold it too tight it will punch deeper and make the weld look saggy, i would say keep 1/8 - 3/32 arc gap, go about half the speed of flat and just trust the puddle wont drip, it will feel very unnatural at first, once you get moving you'll be able to see the puddle and make adjustments accordingly, just make sure you're comfortable and can see the underside of your rod.
Try tuning the machine on a flat plate first, you want to get the heat so the rod just stays lit with a tight arc, secondly you may have beast luck running a corner joint vertical up, flat plate will be more difficult, the corners help kind of catch the puddle so u can see it better.
Go straight in maybe even the slightest, and i do mean slight, rod angle up.
People say hold a tight arc, this messed me up for the longest time because if you hold it too tight it will punch deeper and make the weld look saggy, i would say keep 1/8 - 3/32 arc gap, go about half the speed of flat and just trust the puddle wont drip, it will feel very unnatural at first, once you get moving you'll be able to see the puddle and make adjustments accordingly, just make sure you're comfortable and can see the underside of your rod.
On vertical up 7018 you may see the flux/slag drip away, but that’s not the weld puddle. After some practice you will be able to see the difference between the weld puddle and the slag on top.
I have more questions than answers
Josh
Josh
I have a different issue with 7018 vert, or maybe the same who knows..... i can run it weave like I’ve been doing it all my life, but I can’t do stringers. I know and understand that I’m building a weld puddle onto itself, but just don’t seem to have a technique that works. When I’m weaving I’m stacking on top of a puddle that has hardened and it’s fine. When doing a stringer you have to find a way to cool it so you can build on it. Totally understand all that, but have yet to master it. The only way I’ve successfully did it is to pull up and drop back down. The split second gives the puddle just enough time to start cooling. Never looks as good as i think it should though.
1957 Lincoln Idealarc 300, Miller 211 v1 mig, Lincoln 3350, CK Worldwide CK17FV, 9FV
Return to “Stick Welding/Arc Welding - Shielded Metal Arc Welding”
Jump to
- Introductions & How to Use the Forum
- ↳ Welcome!
- ↳ Member Introductions
- ↳ How to Use the Forum
- ↳ Moderator Applications
- Welding Discussion
- ↳ Metal Cutting
- ↳ Tig Welding - Tig Welding Aluminum - Tig Welding Techniques - Aluminum Tig Welding
- ↳ Mig and Flux Core - gas metal arc welding & flux cored arc welding
- ↳ Stick Welding/Arc Welding - Shielded Metal Arc Welding
- ↳ Welding Forum General Shop Talk
- ↳ Welding Certification - Stick/Arc Welding, Tig Welding, Mig Welding Certification tests - Welding Tests of all kinds
- ↳ Welding Projects - Welding project Ideas - Welding project plans
- ↳ Product Reviews
- ↳ Fuel Gas Heating
- Welding Tips & Tricks
- ↳ Video Discussion
- ↳ Wish List
- Announcements & Feedback
- ↳ Forum News
- ↳ Suggestions, Feedback and Support
- Welding Marketplace
- ↳ Welding Jobs - Industrial Welding Jobs - Pipe Welding Jobs - Tig Welding Jobs
- ↳ Classifieds - Buy, Sell, Trade Used Welding Equipment
- Welding Resources
- ↳ Tradeshows, Seminars and Events
- ↳ The Welding Library
- ↳ Education Opportunities