DM45R mill. Yup, it's a used import, but it came with a lot of tooling, multiple vises (1 rotary), power feed and 3-axis DRO, the price was right, previously owned by an engineer who maintained it quite well, and it was fairly local. Not the Bridgeport I wanted, but it will serve my shop nicely for it's needed purpose: helping to make fixtures for welding setups, mostly out of aluminum. But I'm sure it will see some customer-spec parts soon enough. We'll see how it holds up to that task.
Metal cutting - oxyfuel cutting, plasma cutting, machining, grinding, and other preparatory work.
TraditionalToolworks
- TraditionalToolworks
-
Weldmonger
-
Posts:
-
Joined:Mon Dec 18, 2017 7:49 am
-
Location:San Jose / Kelseyville
Got to play around with it quite a bit today just running some test passes with end mills and a 2.5" face mill on some big chunks of AL. It performed better than I expected. Was able to take 80 thou passes with that face mill without issue. Didn't try deeper, but i'll see what she can handle tomorrow, and also throw some steel at her.
The tram is off by 1 thou across five inches, so I'm contemplating whether or not to try to adjust it or not. Might take a lot of swearing to make what is essentially a 0.0005" adjustment to get the tram perfect, but I'll probably tackle it. It was only barely noticeable when running that face mill.
I did manage to hit the duty cycle on the power feed after running it for about 90 mins straight. It just stopped feeding mid cut and I was worried it may have broken. But then I felt how hot the motor box was and was hoping that it was just a temp cutout...and thankfully that's all it was.
The tram is off by 1 thou across five inches, so I'm contemplating whether or not to try to adjust it or not. Might take a lot of swearing to make what is essentially a 0.0005" adjustment to get the tram perfect, but I'll probably tackle it. It was only barely noticeable when running that face mill.
I did manage to hit the duty cycle on the power feed after running it for about 90 mins straight. It just stopped feeding mid cut and I was worried it may have broken. But then I felt how hot the motor box was and was hoping that it was just a temp cutout...and thankfully that's all it was.
TraditionalToolworks
- TraditionalToolworks
-
Weldmonger
-
Posts:
-
Joined:Mon Dec 18, 2017 7:49 am
-
Location:San Jose / Kelseyville
Alu good to play around with, that mill is probably suited well for Alu. Stainless can be a bear to mill.Spartan wrote:Got to play around with it quite a bit today just running some test passes with end mills and a 2.5" face mill on some big chunks of AL.
What type of face mill, was it a 45 degree SEET style? I use that style on my mills and it works well, has 4 edges per insert.
Shouldn't contemplate it at all, you should definitely do it and get familiar with it, you will need to tram a mill often, sometimes you will tram it on an angle to cut a specific taper, and then you will need to tram it back square. I personally wouldn't be concerned with changing it, you should be able to make it better than .001", but to be honest .001" is not bad for an import mill. I was able to get my mini-mill better than that when I owned it, but I completely disassembled the entire thing, cleaned it all and put it all back together properly...that was the first mill I bought off craigslist. Your mill is a slight step above a mini-mill, but you should learn how to set it up the best you can. Your mill though, so not trying to tell you what to do...I'd aim for getting it as close to perfect as you can, keep it well oiled, and if you can cover it when not in use (but I don't do that to mineSpartan wrote:The tram is off by 1 thou across five inches, so I'm contemplating whether or not to try to adjust it or not.

If the motor starts getting hot you should take a break, couldn't hurt to get a big glass of ice tea, my motto...

Collector of old Iron!
Alan
Alan
This guy here. Uses the TPGN inserts. Just bought some more SECO NOS ones off of ebay for pennies on the dollar. Better grade, also. I despise the uncoated carbide inserts for any material.TraditionalToolworks wrote:What type of face mill, was it a 45 degree SEET style? I use that style on my mills and it works well, has 4 edges per insert.
- IMG_2326.jpg (30.6 KiB) Viewed 2178 times
TraditionalToolworks
- TraditionalToolworks
-
Weldmonger
-
Posts:
-
Joined:Mon Dec 18, 2017 7:49 am
-
Location:San Jose / Kelseyville
Your pic didn't come through, but I will mention that for some harder steels, those triangle inserts could be useful, especially in regard to removing all insert except 1 which will act like a fly cutter. You will essentially have 1 contact edge for the entire face mill. That could be really useful on your mill with stainless, which is tougher than gorilla snot.Spartan wrote:This guy here. Uses the TPGN inserts. Just bought some more SECO NOS ones off of ebay for pennies on the dollar. Better grade, also. I despise the uncoated carbide inserts for any material.TraditionalToolworks wrote:What type of face mill, was it a 45 degree SEET style? I use that style on my mills and it works well, has 4 edges per insert.
IMG_2326.jpg
What I was talking about with 45 degree inserts is this style.
https://www.latheinserts.com/45-DEGREE- ... S_c178.htm
Collector of old Iron!
Alan
Alan
I'll try reposting the pic below. Not sure how one would classify it in terms of degrees, though...
Edit: It looks like the insert tip is chipped, but it's not. Most likely just some galled AL on it. Part of the reason I hate those uncoated inserts.
Edit: It looks like the insert tip is chipped, but it's not. Most likely just some galled AL on it. Part of the reason I hate those uncoated inserts.
- IMG_2326.jpg (30.6 KiB) Viewed 2169 times
TraditionalToolworks
- TraditionalToolworks
-
Weldmonger
-
Posts:
-
Joined:Mon Dec 18, 2017 7:49 am
-
Location:San Jose / Kelseyville
Traingle is 120 degrees, but people don't usually talk abut them like that as it's just taken for granted. Some inserts like CNMG have 2 different angles, and you can use all of them if you have specific holders to reference the edges, but typically a holder will only allow for one angle. Face mills are different than lathe tools as an example.Spartan wrote:I'll try reposting the pic below. Not sure how one would classify it in terms of degrees, though...
In the case of what I was explaining to you, if you only use 1 insert in your face mill, it will act like a fly cutter which only uses a single cutter, those produce nice finish at higher speeds, than say a face mill with 3 or 4 inserts.
Doesn't look too bad, but this is where magnification comes in handy to look at the tip.Spartan wrote:Edit: It looks like the insert tip is chipped, but it's not. Most likely just some galled AL on it. Part of the reason I hate those uncoated inserts.
Even an OptiVisor can help a lot, say 2.5x magnification.
Rotate your inserts all at the same time so you can keep track of the worn edges. Not a bad idea to mark them after used.
Collector of old Iron!
Alan
Alan
Gotcha. I didn't know if the degrees you were talking about were for the inserts themselves, or a specific profile that the tool was meant to create. I'm still getting used to the milling terminology.TraditionalToolworks wrote:Traingle is 120 degrees, but people don't usually talk abut them like that as it's just taken for granted. Some inserts like CNMG have 2 different angles, and you can use all of them if you have specific holders to reference the edges, but typically a holder will only allow for one angle. Face mills are different than lathe tools as an example.Spartan wrote:I'll try reposting the pic below. Not sure how one would classify it in terms of degrees, though...
CNMGs (43x) are my go-to inserts for all of my lathe tooling on the Aloris tool post. Probably have a few hundred of them. If/when I buy more insert-capable tool holders for this mill, I will certainly be seeking out ones compatible with those CNMGs.
I also run other inserts on the lathe. Some TNMG, TCMT, DCMT, and VNMG, but those CNMGs are what I use probably 95% of the time. They're just great all-around.
TraditionalToolworks
- TraditionalToolworks
-
Weldmonger
-
Posts:
-
Joined:Mon Dec 18, 2017 7:49 am
-
Location:San Jose / Kelseyville
Depending on the ability of the lathe, CNMG might not be the best. Negative rake tooling requires more horsepower and faster speeds, so some lathes are not well suited for it and wold be best with positive rake and/or HSS tooling.Spartan wrote:CNMGs (43x) are my go-to inserts for all of my lathe tooling on the Aloris tool post. Probably have a few hundred of them. If/when I buy more insert-capable tool holders for this mill, I will certainly be seeking out ones compatible with those CNMGs.
You have a mix of negative and positive rake there. The N is negative, but I don't think it stands for negative specific, not sure...so TNMG is negative, but TCMT is positive. Both of those are Triangle. DCMT is also positive (diamond), and VNMG (narrow diamond) is negative as-is CNMG, which is a parallelogram. The W is interesting as it has a wide angle on 3 sides because of the geometry.Spartan wrote:I also run other inserts on the lathe. Some TNMG, TCMT, DCMT, and VNMG, but those CNMGs are what I use probably 95% of the time. They're just great all-around.
Triangle is one of the oldest carbide shape, and you can usually find them cheap on ebay. I happen to like them and have a few triangle holders, a couple came with one of my lathes from Hershey, they may have bought the holders in the 60s or 70s, but they work fine to this day. Those were ground down Sandvik. It's harder to get negative rake on smaller tool holders typically, because smaller lathes are not good with carbide. My Rivett lathe had an Aloris AXA on it from the factory in the 60s, so the holders were ground down by Hershey to fit in the tool post holders. I have replaced it with a Dorian BXA size as it gives more adjustment on the height.
Inserts are a whole can of worms in themselves, but nobody should be without HSS blanks and the ability to grind them, they are the safest to have, IMO, as you can grind any shape you need with the skill. These days too many people are lazy to learn to grind their own toolbits, and rely on carbide for that... That's a bad deal, IMO.
Collector of old Iron!
Alan
Alan
Agreed that HSS should still be in everyone's shop. I shifted to mostly carbide inserts for the lathe a few years ago, but still cut some HSS when needed.TraditionalToolworks wrote:Depending on the ability of the lathe, CNMG might not be the best. Negative rake tooling requires more horsepower and faster speeds, so some lathes are not well suited for it and wold be best with positive rake and/or HSS tooling.Spartan wrote:CNMGs (43x) are my go-to inserts for all of my lathe tooling on the Aloris tool post. Probably have a few hundred of them. If/when I buy more insert-capable tool holders for this mill, I will certainly be seeking out ones compatible with those CNMGs.
You have a mix of negative and positive rake there. The N is negative, but I don't think it stands for negative specific, not sure...so TNMG is negative, but TCMT is positive. Both of those are Triangle. DCMT is also positive (diamond), and VNMG (narrow diamond) is negative as-is CNMG, which is a parallelogram. The W is interesting as it has a wide angle on 3 sides because of the geometry.Spartan wrote:I also run other inserts on the lathe. Some TNMG, TCMT, DCMT, and VNMG, but those CNMGs are what I use probably 95% of the time. They're just great all-around.
Triangle is one of the oldest carbide shape, and you can usually find them cheap on ebay. I happen to like them and have a few triangle holders, a couple came with one of my lathes from Hershey, they may have bought the holders in the 60s or 70s, but they work fine to this day. Those were ground down Sandvik. It's harder to get negative rake on smaller tool holders typically, because smaller lathes are not good with carbide. My Rivett lathe had an Aloris AXA on it from the factory in the 60s, so the holders were ground down by Hershey to fit in the tool post holders. I have replaced it with a Dorian BXA size as it gives more adjustment on the height.
Inserts are a whole can of worms in themselves, but nobody should be without HSS blanks and the ability to grind them, they are the safest to have, IMO, as you can grind any shape you need with the skill. These days too many people are lazy to learn to grind their own toolbits, and rely on carbide for that... That's a bad deal, IMO.
You may be right that the "N" in CNMG is for negative, but I've always thought of it as "neutral" since the rake angle is at 0 degrees on the insert, and set by the tool itself. I use them on my BXA holders on my Grizzly 12x36" lathe (probably seen as a small, crappy import for most folks, but I like it). They work just fine on my lathe, but I will admit that they are probably meant for larger setups.
Edit: And yes, I have accumulated a lot of both positive and negative rake tooling, but the larger negative rake inserts seem to work just fine, even for the light finishing cuts, and seem to last quite a bit longer. I think it's more about the chip breakers for the inserts you choose then the insert size itself, at least IMO.
Today's adventure on the new mill: Cutting a clearance void in this piece of 1.5", .083" wall 4130 tubing for a customer setup. Turned out well, but took me about 2 hours to figure out the best way to do it with that 2-flute, 1/2" end mill. Going to try a 4-fluter next time and will also play around with using both smaller and larger diameter end mills to see what responds best to those unusual cuts. Opted to take only 60-80 thou passes each time to avoid chatter, but it was manageable to get it down to just under a total depth of 1/2". Learned a few tricks on cutting geometry along the way to reduce the chatter, though.
Also working on a MUCH better clamping solution
. Will be doing a lot more of these, and this run was largely just to prove the concept.
Also working on a MUCH better clamping solution

- IMG_2324.jpg (92.72 KiB) Viewed 2148 times
TraditionalToolworks
- TraditionalToolworks
-
Weldmonger
-
Posts:
-
Joined:Mon Dec 18, 2017 7:49 am
-
Location:San Jose / Kelseyville
No, if you have 0 degree rake looking at the holder from the side, you have the wrong insert in the holder. The reason I say this is there is no relief on the cutting edge of a CNMG, that is the entire idea behind negative rake, the negative rake provides the clearance. CNMG is able to use both sides of the cutter, and in fact all negative rake tooling is, the front edge is 90 degree so there's no relief, but the holder provides the relief in use. WNMG as an example, has 3 cutting edges to index, but since you can use both sides as it's negative rake, you get 6 cutters off each insert. For CNMG you can only use 2 edges on the parallelogram but you get both sides so get 4. I have a holder I can use the other 2 edges on, so I can use all 8. Some people do that by using the other 2 in their mill, but you need the special tool for that also.Spartan wrote:You may be right that the "N" in CNMG is for negative, but I've always thought of it as "neutral" since the rake angle is at 0 degrees on the insert, and set by the tool itself.
Yes and No, IMO. As long as you have the correct insert in the tool holder you should be able to regulate the speed to break the chip. Some tools have better chip breakers by design, like on some of the D style inserts, some of those really have a deep chip breaker on them where the edge is dished out so that the chip curls up nicely.Spartan wrote:Edit: And yes, I have accumulated a lot of both positive and negative rake tooling, but the larger negative rake inserts seem to work just fine, even for the light finishing cuts, and seem to last quite a bit longer. I think it's more about the chip breakers for the inserts you choose then the insert size itself, at least IMO.
I'm not an expert machinist, but have been doing it for a while. I'm probably more comfortable on my lathe and mill than I am my welder...FWIW. The whole reason I wanted to tig weld was to make tools, it isolates the heat in the part so it's exceptionally good for tool makers.

Collector of old Iron!
Alan
Alan
Certainly. I think our words got lost in the text translation a bit. I simply meant that the insert itself is a 0 degree relief angle (or 90 degrees as you mentioned...same angle, different perspective) unlike the positive rake inserts, and that the tool holder takes that 0/90 degree insert and angles it down appropriately to provide the relief. I have the right inserts in the right tooling. At least for the lathe! You may need to to step in and stop me when it comes to the millTraditionalToolworks wrote:No, if you have 0 degree rake looking at the holder from the side, you have the wrong insert in the holder. The reason I say this is there is no relief on the cutting edge of a CNMG, that is the entire idea behind negative rake, the negative rake provides the clearance. CNMG is able to use both sides of the cutter, and in fact all negative rake tooling is, the front edge is 90 degree so there's no relief, but the holder provides the relief in use. WNMG as an example, has 3 cutting edges to index, but since you can use both sides as it's negative rake, you get 6 cutters off each insert. For CNMG you can only use 2 edges on the parallelogram but you get both sides so get 4. I have a holder I can use the other 2 edges on, so I can use all 8. Some people do that by using the other 2 in their mill, but you need the special tool for that also.Spartan wrote:You may be right that the "N" in CNMG is for negative, but I've always thought of it as "neutral" since the rake angle is at 0 degrees on the insert, and set by the tool itself.

TraditionalToolworks
- TraditionalToolworks
-
Weldmonger
-
Posts:
-
Joined:Mon Dec 18, 2017 7:49 am
-
Location:San Jose / Kelseyville
I think you're right. I was referring to the actual insert, if the front is 90 degrees it would have no clearance if using it on a CCMT toolholder, which would be positive rake. Positive rake is really neutral, i.e. flat, when viewed from the side, in most but not all cases. Sometimes the insert rises above neutral and the relief is angled back. On a CCMT insert, it has about 5 degree of angle on the leading edge, that's where the relief is provided. Where on a CNMG the insert is actually angled downward toward the nose so that the front edge of the cutter has relief. Something else to keep in mind. Negative rake tooling doesn't really cut, it actually tears the material off, that's why it needs speed.Spartan wrote:Certainly. I think our words got lost in the text translation a bit. I simply meant that the insert itself is a 0 degree relief angle (or 90 degrees as you mentioned...same angle, different perspective) unlike the positive rake inserts, and that the tool holder takes that 0/90 degree insert and angles it down appropriately to provide the relief. I have the right inserts in the right tooling. At least for the lathe! You may need to to step in and stop me when it comes to the mill
Keep in mind, positive rake is good for anything you don't have rigidity on, could be a long boring bar sticking out 10" from the toolholder, or a low powered machine, and any number of other reasons you want to reduce the amount of force on the toolholder. I wasn't trying to mince your words, maybe you explained it wrong, so I was just trying to explain it to you how I view negative vs. positive rake tooling. I use both CMNG and CCMT on my lathe. I try not to use negative tooling on my South Bend 9A or the South Bend Heavy 10 I don't have in operation yet, it's going to the new shop. I will use positive rake and HSS for it.
Whatever type of tooling you use that provides a decent finish is the right tool, IMO. If you have success with negative rake tooling on your 12" Grizzly lathe, more power to you. I would use positive rake and/or HSS on it myself. One other key point to keep in mind...carbide like speed, HSS doesn't. When you need to cut something at slow speeds, HSS is your friend, but if you can use higher speeds, carbide is your friend. If you're not getting a good finish with carbide it doesn't hurt to try and turn the speed up. OTOH, if you're getting a crappy finish with HSS, it usually doesn't hurt to turn the speed down. Of course these are just generalizations as there are hundreds of conditions that come into play for both.
Collector of old Iron!
Alan
Alan
TraditionalToolworks
- TraditionalToolworks
-
Weldmonger
-
Posts:
-
Joined:Mon Dec 18, 2017 7:49 am
-
Location:San Jose / Kelseyville
As a follow up to Spartan's thread, I did mention to him in a PM that I saw they do refer to the CNMG inserts as being neutral for the insert, which actually makes sense as there is no rake on the insert themselves, but the holders have the negative rake on them, or in the case of the CCMT as an example, rake is incorporated into the insert itself. I took a couple pics to show a couple things.
This is a top view to show the wide vs narrow angle. On the right side are CCMT cutters and both are using the small angle, I often use the bottom one to add a chamfer to a part, the top one is a typical CCMT RH cutter, just upside down. These holders can only use the small angle, but can use only 2 edges on each insert, 2 on top and that's it because they have relief cut into them and the other side won't allow it to be used, the relief would be in the wrong orientation. On the left is a CNMG and it's in a special holder that allows the use of the wide angle. This cutter can only use the wide angle, but it can use top and bottom as there is no relief on the cutting edge, the negative rake holder provides the rake by orientation. This holder can use 4 edges, 2 wide angles on top and 2 wide angles on the bottom. I couldn't find my CNMG RH cutter for this pic.

This pic shows a side view, to show how the insert is angled down on the left (CNMG) and flat for the right (CCMT). This is purely to do with the holder and either creates the relief as on the CNMG (left) or not as on the CCMT (right). If there was no relief on the CCMT insert, the front of the insert would possibly rub on the material. However, that is slightly subjective also as in theory if setup correctly only the top edge will come in contact with the material.

Probably more info that anyone wanted, but a picture says a thousand words as they say...
This is a top view to show the wide vs narrow angle. On the right side are CCMT cutters and both are using the small angle, I often use the bottom one to add a chamfer to a part, the top one is a typical CCMT RH cutter, just upside down. These holders can only use the small angle, but can use only 2 edges on each insert, 2 on top and that's it because they have relief cut into them and the other side won't allow it to be used, the relief would be in the wrong orientation. On the left is a CNMG and it's in a special holder that allows the use of the wide angle. This cutter can only use the wide angle, but it can use top and bottom as there is no relief on the cutting edge, the negative rake holder provides the rake by orientation. This holder can use 4 edges, 2 wide angles on top and 2 wide angles on the bottom. I couldn't find my CNMG RH cutter for this pic.

This pic shows a side view, to show how the insert is angled down on the left (CNMG) and flat for the right (CCMT). This is purely to do with the holder and either creates the relief as on the CNMG (left) or not as on the CCMT (right). If there was no relief on the CCMT insert, the front of the insert would possibly rub on the material. However, that is slightly subjective also as in theory if setup correctly only the top edge will come in contact with the material.

Probably more info that anyone wanted, but a picture says a thousand words as they say...
Collector of old Iron!
Alan
Alan
TraditionalToolworks
- TraditionalToolworks
-
Weldmonger
-
Posts:
-
Joined:Mon Dec 18, 2017 7:49 am
-
Location:San Jose / Kelseyville
Spartan,
I have some DNMG inserts that are almost identical to those other than shape. They work well, that black finish is primarily for steel, at least my understanding. The gold finish is often slightly more durable, but similar, and there's a shiny silver that is often used for aluminum. As you may know, you can mix/match the inserts on various metals, even if they don't specify them specific, but the black works well for cast iron also.
These were the ones with the chip breaker I was telling you about, I haven't tried them but saw them on Abom79's channel some time ago, he was hogging off some stainless at about .400" per rev on a Pacemaker, big honkin' 6s and 9s poppin' off it.
You can't use the wide angle on these, but you get 4 edges, 2 per side. I use DNMG a lot, the shape let's me get into pretty tight spaces and if I can't get a corner/shoulder with them, I switch to V as it's narrower and longer.
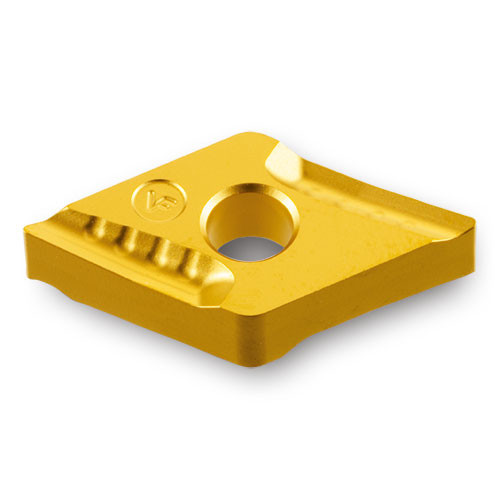
I have some DNMG inserts that are almost identical to those other than shape. They work well, that black finish is primarily for steel, at least my understanding. The gold finish is often slightly more durable, but similar, and there's a shiny silver that is often used for aluminum. As you may know, you can mix/match the inserts on various metals, even if they don't specify them specific, but the black works well for cast iron also.
These were the ones with the chip breaker I was telling you about, I haven't tried them but saw them on Abom79's channel some time ago, he was hogging off some stainless at about .400" per rev on a Pacemaker, big honkin' 6s and 9s poppin' off it.
You can't use the wide angle on these, but you get 4 edges, 2 per side. I use DNMG a lot, the shape let's me get into pretty tight spaces and if I can't get a corner/shoulder with them, I switch to V as it's narrower and longer.
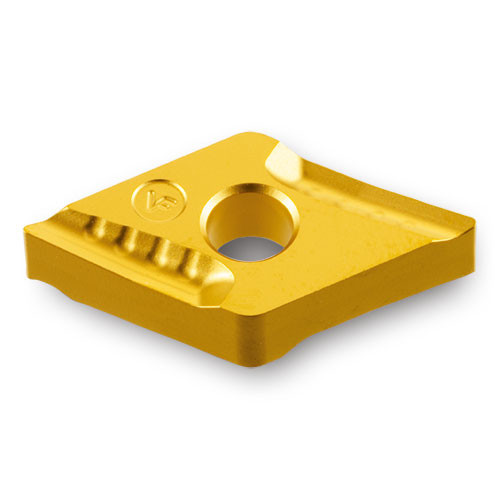
Collector of old Iron!
Alan
Alan
Some more tubing cuts. Had to make up a custom riser to hold this tubing which had already been bent, so couldn't fixture it flush to the table. Still waiting on those 4 flute end mills to arrive, but starting to get the knack of this. Added some mist coolant which makes things easier. The mag base for the coolant nozzle doesn't hold well to the head area, so have it just on the table right now which is not ideal. Need to make a fixture point on the head for it. Loving this mill so far.
- IMG_2341.jpg (105.24 KiB) Viewed 2026 times
Jump to
- Introductions & How to Use the Forum
- ↳ Welcome!
- ↳ Member Introductions
- ↳ How to Use the Forum
- ↳ Moderator Applications
- Welding Discussion
- ↳ Metal Cutting
- ↳ Tig Welding - Tig Welding Aluminum - Tig Welding Techniques - Aluminum Tig Welding
- ↳ Mig and Flux Core - gas metal arc welding & flux cored arc welding
- ↳ Stick Welding/Arc Welding - Shielded Metal Arc Welding
- ↳ Welding Forum General Shop Talk
- ↳ Welding Certification - Stick/Arc Welding, Tig Welding, Mig Welding Certification tests - Welding Tests of all kinds
- ↳ Welding Projects - Welding project Ideas - Welding project plans
- ↳ Product Reviews
- ↳ Fuel Gas Heating
- Welding Tips & Tricks
- ↳ Video Discussion
- ↳ Wish List
- Announcements & Feedback
- ↳ Forum News
- ↳ Suggestions, Feedback and Support
- Welding Marketplace
- ↳ Welding Jobs - Industrial Welding Jobs - Pipe Welding Jobs - Tig Welding Jobs
- ↳ Classifieds - Buy, Sell, Trade Used Welding Equipment
- Welding Resources
- ↳ Tradeshows, Seminars and Events
- ↳ The Welding Library
- ↳ Education Opportunities