The start of my welding was when I bought a lincoln pro mig 135 from my job at lowes when I was 18yo, started with just flux core and did ok and everything held together but I had 0 direction and 0 influencs at the time so it collected dust for a couple years til I moved up to oregon and got a classic truck to build on. Barely getting started on the project had a friend of a roomate steal my welder and bottle while I was gone.
That forrced me to trafe the 454 I built for my 66 Chevrolet for a millermatic 175 and bottle to keep the project going but the motor was the heart so it died shortly sfter that. Movet to a house where I had to sell my truck so again the welder sat and no learning or projects to do.
Recently I got a yota 4x4 to have fun with and im ready to het back to practicing and learing so my truck doesnt fall apart on the trail haha.
Heres some of the few practice wlelds ive done since pickin up the gun.
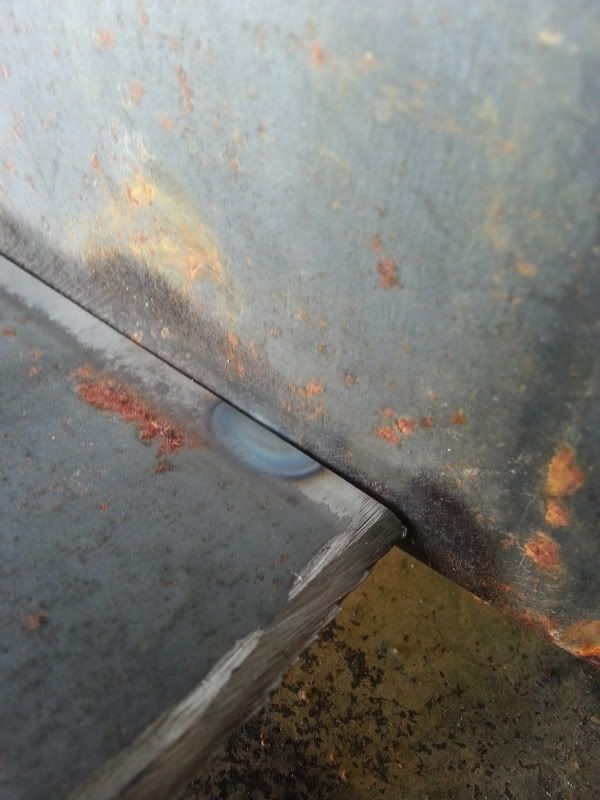
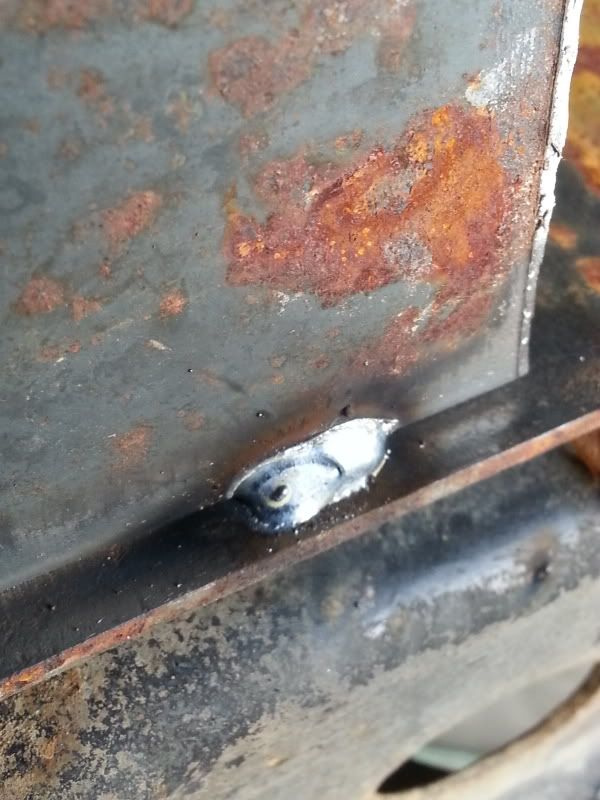
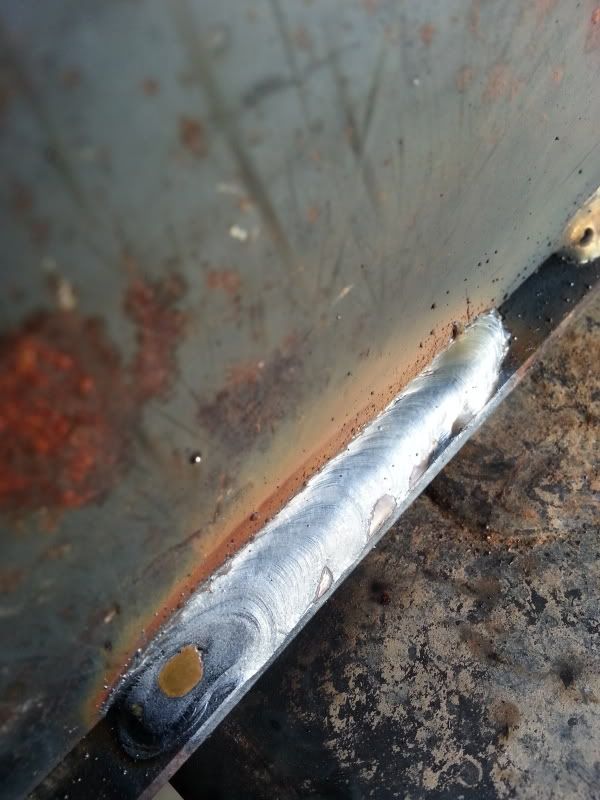
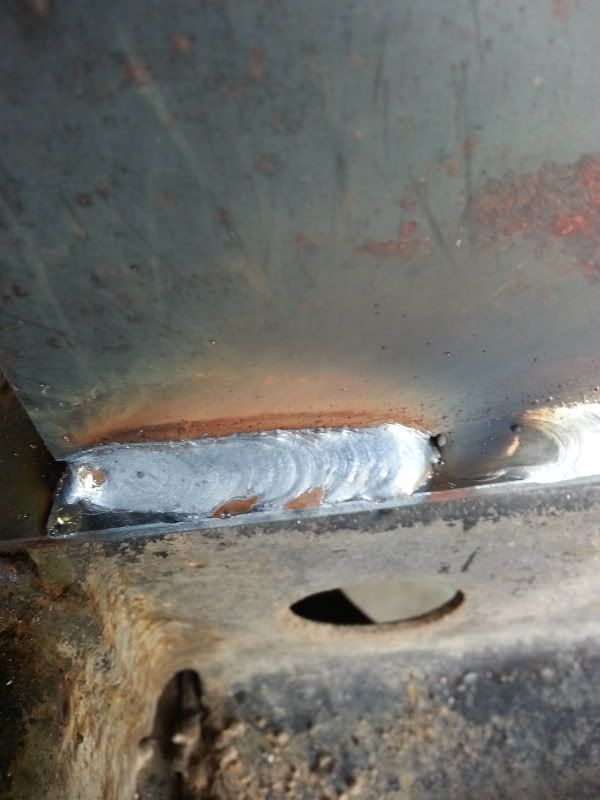
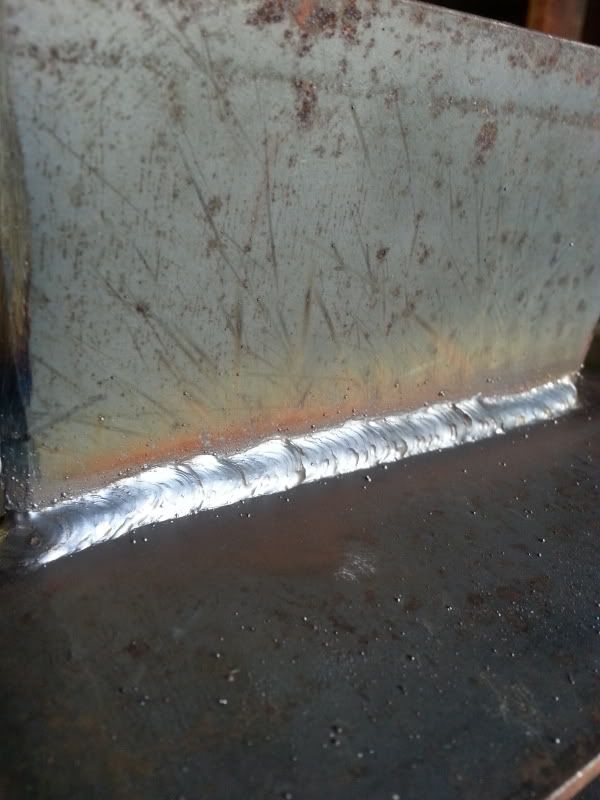
Would be awesome for a pro to let me know if im on the right track or if im way off.
Thanks guys and really appreciate all the info you put on this site.