Page 1 of 1
sleeving a 90 degree joint?
Posted: Sun Jul 20, 2014 3:18 pm
by danielbuck
I'm wondering if such a piece exists already (pre-made), a 90 degree (and possibly other degrees as well) "inner sleeve" piece that would slip into the tubing?
My problem is, I don't always cut perfect 45s. And even if I do, the outside edge is difficult to weld without punching through sometimes. I know I can turn the power down or tack-tack-tack it, but I like the welds on my furniture to be wide and flat, which means I need to turn up the heat a bit. (I'm talking MIG welding here). The wide flat welds make it look heavy, even though it's only 16 gauge. I think with an inner sleeve piece like this, I could turn up the heat a good bit. And as a side benefit, it would also help with assembling the piece, since it's usually just me, I end up using lots of clamps and things before I start tacking. These sleeves would kind of keep things together a bit (a little bit) before tacking.
I know I could make something like this, but I'm wondering if something like this exists already, for sale? I've searched around a bit, but I can't seem to find something like this, maybe I'm not using the right search term
For my furniture, I usually use 1" square tubing (mild steel) that is 16 gauge thick. I've greatly exaggerated the wall thickness in these images, so you can better see what I'm talking about.
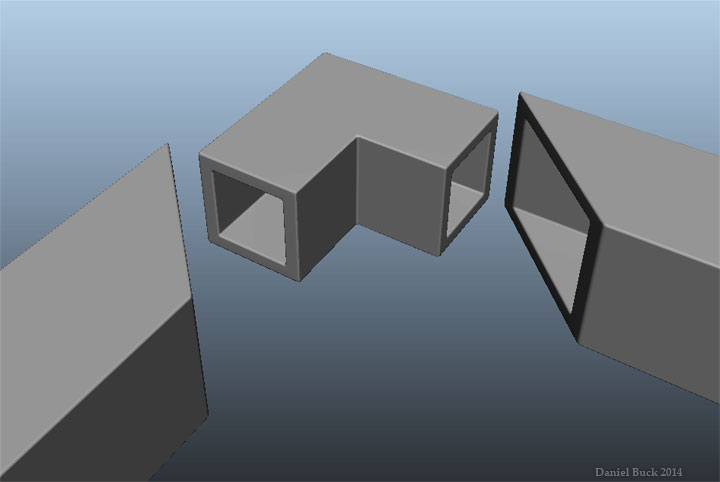
Re: sleeving a 90 degree joint?
Posted: Mon Jul 21, 2014 12:14 am
by TamJeff
I don't know about the sleeves but as far as getting a flat weld on the outside corner, grind the corner flat to the weld size, or close to what you want AND turn the amps down. Bevel the face ends accordingly. Making your own fittings that fit well, would be likely more work than building your furniture twice.
Re: sleeving a 90 degree joint?
Posted: Mon Jul 21, 2014 8:25 am
by aeroplain
IMO, the fittings would be a waste of your time and money, not to mention, the high probability of your furniture to have a nice rattle when you're done.
Kent
Re: sleeving a 90 degree joint?
Posted: Mon Jul 21, 2014 9:00 am
by AndersK
I agree with the others but you can use a square profile , hollow or solid, and insert from one direction. That wil give same support but much easier with only straight cuts.
Re: sleeving a 90 degree joint?
Posted: Mon Jul 21, 2014 11:50 am
by MinnesotaDave
AndersK wrote:I agree with the others but you can use a square profile , hollow or solid, and insert from one direction. That wil give same support but much easier with only straight cuts.
I agree - just use a straight piece as a backer for welding and run hot enough to weld all three together.
Also, on the outside corner, grind the knife edge off before welding.
Or switch to tig - much more control on what your finished weld looks like.
Re: sleeving a 90 degree joint?
Posted: Mon Jul 21, 2014 11:53 am
by danielbuck
I am learning TIG right now, it's slow going though!

That's actually why I picked up a TIG machine, so that I can hopefully have nice looking welds on my future furniture projects.
As for grinding flat, and backing off on the power, I've tried that, and I never seem to get a flat looking weld that doesn't punch through. It's always on the outside corner, even if I weld it down-hill to try and keep from punching through or stacking up to much.
Re: sleeving a 90 degree joint?
Posted: Mon Jul 21, 2014 11:57 am
by rick9345
AndersK wrote:I agree with the others but you can use a square profile , hollow or solid, and insert from one direction. That wil give same support but much easier with only straight cuts.
what I was thinking
Re: sleeving a 90 degree joint?
Posted: Mon Jul 21, 2014 12:29 pm
by MinnesotaDave
danielbuck wrote:I am learning TIG right now, it's slow going though!

That's actually why I picked up a TIG machine, so that I can hopefully have nice looking welds on my future furniture projects.
As for grinding flat, and backing off on the power, I've tried that, and I never seem to get a flat looking weld that doesn't punch through. It's always on the outside corner, even if I weld it down-hill to try and keep from punching through or stacking up to much.
Keep after your tig practice - it's awesome
I tell people to hammer through the first 100 hours as quickly as you can - much easier after that

Re: sleeving a 90 degree joint?
Posted: Mon Jul 21, 2014 2:47 pm
by danielbuck
MinnesotaDave wrote:danielbuck wrote:I am learning TIG right now, it's slow going though!

That's actually why I picked up a TIG machine, so that I can hopefully have nice looking welds on my future furniture projects.
As for grinding flat, and backing off on the power, I've tried that, and I never seem to get a flat looking weld that doesn't punch through. It's always on the outside corner, even if I weld it down-hill to try and keep from punching through or stacking up to much.
Keep after your tig practice - it's awesome
I tell people to hammer through the first 100 hours as quickly as you can - much easier after that

100 hours will take me a year at least, haha! I only have time to tinker on the weekends, inbetween getting other stuff done. I can tell that it'll definitely be nice once I get the hang of it though.