If I turn down the settings to accomodate the 18ga, it's hard to penetrate the rod but if I crank it up to penetrate the rod, I burn up the levers. Any suggestions on the best way to weld these together? I have both a MIG and TIG available to me
This is a picture of the final piece:
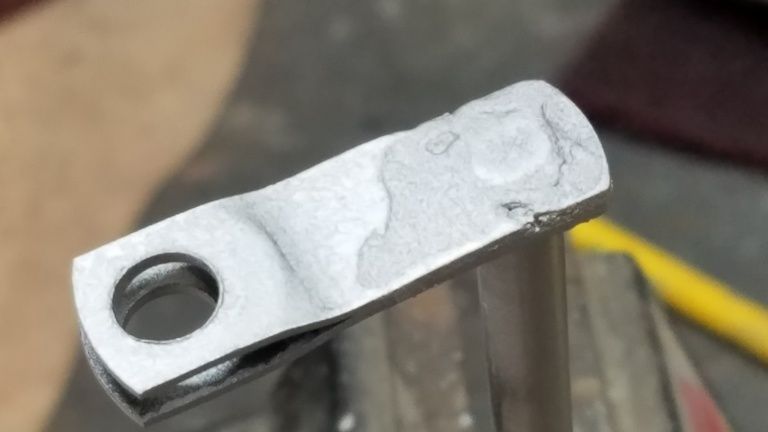
Not an expert welder by any stretch and this is really testing my skills.
Thanks
Paul