
i'm a guitar builder and am thinking of picking up welding to create truss rods for my guitars. A truss rod is a device that is built into the neck of a guitar under the fretboard to counteract string tension and control/remove up- and back-bow of the neck. Here is a simplified diagram of the principle:

It's a pretty simple device and the problem i have is that i need specific lengths and adjustment screws and i'm tired having to adapt my builds to what is available on the market. Being able to make my own truss rods to MY specs would be awesome .. and of course more economical.
One of the most promising materials i've tried so far is Titanium on steel since the titanium truss rods weigh only half as much as the steel ones (which is important for the balance of the final instrument), but unfortunately there is only one variant available on the market as of today (made in Japan i think) and once again i can't find it with the right length and adjustment screw. The other reason i would like to make my own titanium truss rods is the price, these retail for around 45€/USD a piece which is a lot considering the base material cost of less than 5€. I've asked around here where i live if someone could make custom rods for me but welders are either not interested in such a small job or are asking for a lot of money (which i understand but just isn't workable for me).
I've been reading up and watching youtube about welding to get a basic understanding but am overwhelmed by the amount of information and different options.
So i was wondering if some of you could help me identify what kind of welding would be most apropriate to do these tiny welds.
There are two different welds: the weld connecting the flat steel bar to the threaded block holding the rod and the weld (possibly a braze ?) connecting the adjustment screw to the threaded rod:
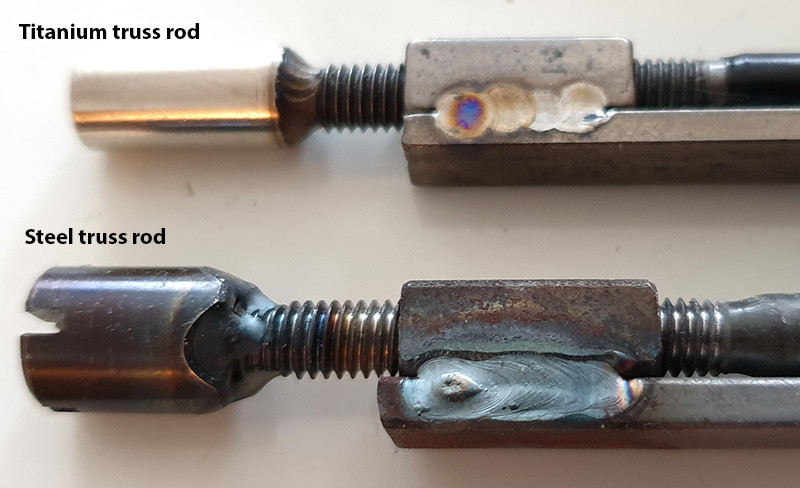
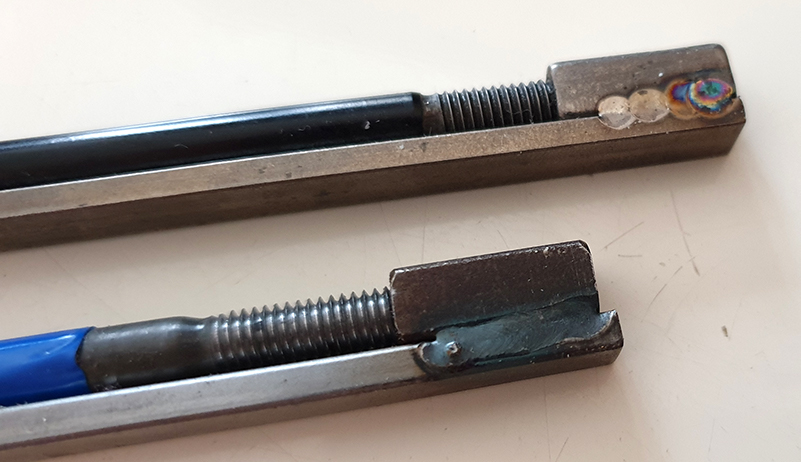
I think on the titanium truss rod the flat bar and the threaded block is actually steel. I'm not sure about the grade of titanium either, someone said somewhere on the web it was grade 2.
So the questions i'm asking myself at this point are:
1. Is it realistic for someone who has absolutely no experience/knowledge about welding to undertake such an enterprise ?
2. Is it even a good idea/safe to try to learn welding on my own (there are only lengthy and expensive courses for welding in my area and i don't really want to weld anything else than those tiny dot welds and connect an adjustment screw to the threaded rod) ?
3. What kind of welding technique(s) are most apropriate for welding titanium to steel ?
4. Would a cheap-ish welding machine be adequate for this or does titanium welding require 'proper' gear ?
5. If titanium welding for me isn't realistic then what kind of welding technique would i need to make the traditional steel rods ?
Many thx in advance for your help

PS: i've used many different steel truss rods from various manufacturers and sometimes the welds look a bit shoddy to my untrained eye. Can you tell from the pictures above if these are quality welds ?